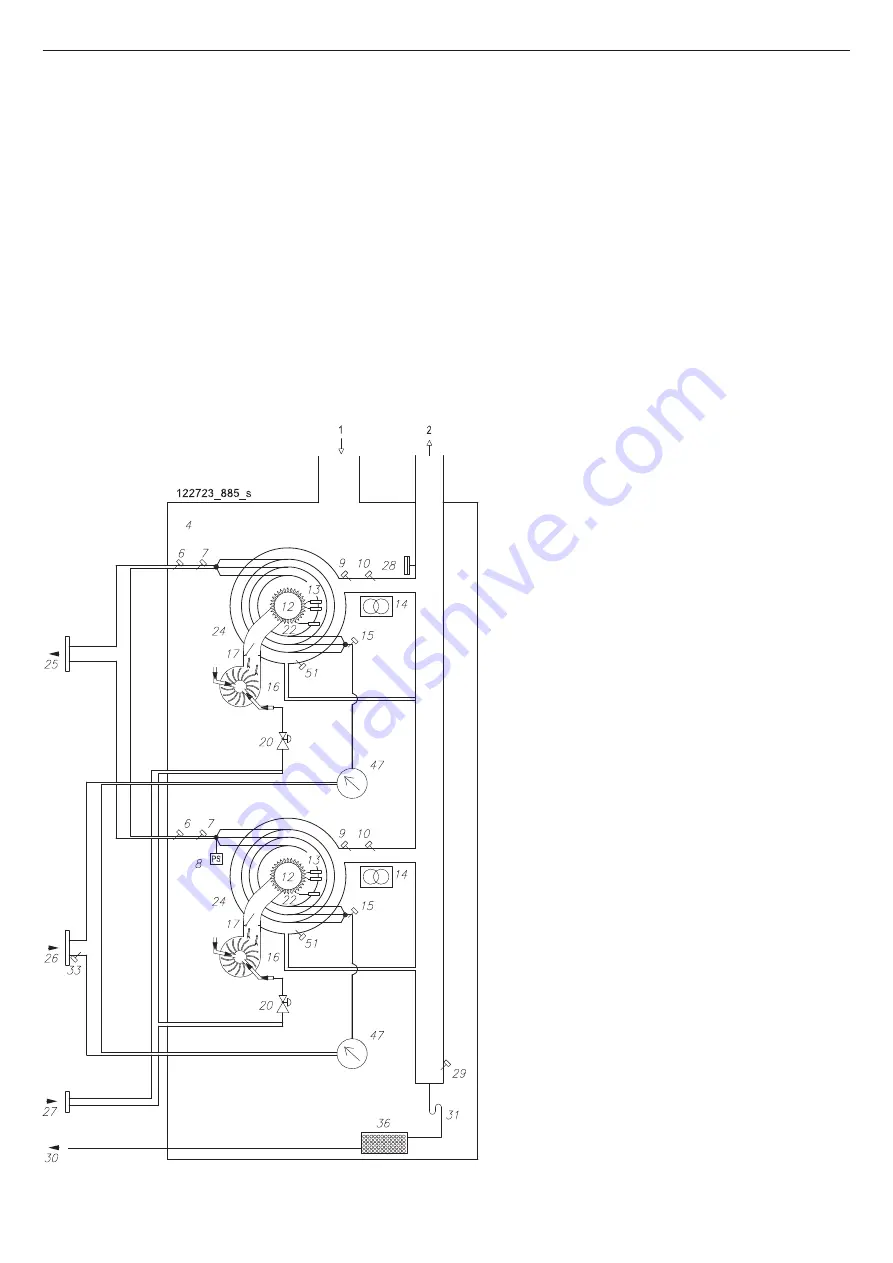
17
POOLDENS
COSMOGAS
4 - OPERATION
Figure 4-2 - Hydraulic operating diagram for models 100T, 115T and 140T
Figure 4-2 Key:
1 - Air intake
2 - Exhaust gases outlet
4 - Sealed chamber
6 - Water outlet temperature safety thermostat
7 - Water outlet temperature sensor
8 - Water pressure gauge
9 - Exhaust gases temperature sensor
10 - Exhaust gases temperature safety fuse
12 - Pre-mixed burner
13 - Ignition electrodes
14 - Sparks generator
15 - Water inlet temperature sensor
16 - Fan
17 - Back flue preventer valve
20 - Gas valve
22 - Detection electrode
24 - VRC heat exchanger
25 - Water outlet
26 - Water inlet
27 - Gas inlet
28 - Pressure switch against outlet blockage
29 - Condensate level sensor
30 - Condensate outlet
31 - Condensate outlet siphon
33 - Pool return temperature sensor
36 - Condensate neutraliser
47 - Water flow rate gauge
51 - Primary heat exchanger temperature fuse
Summary of Contents for POOLDENS 100T
Page 2: ......
Page 95: ......
Page 96: ...COSMOGAS s r l Via L da Vinci 16 47014 MELDOLA FC ITALY info cosmogas com www cosmogas com ...