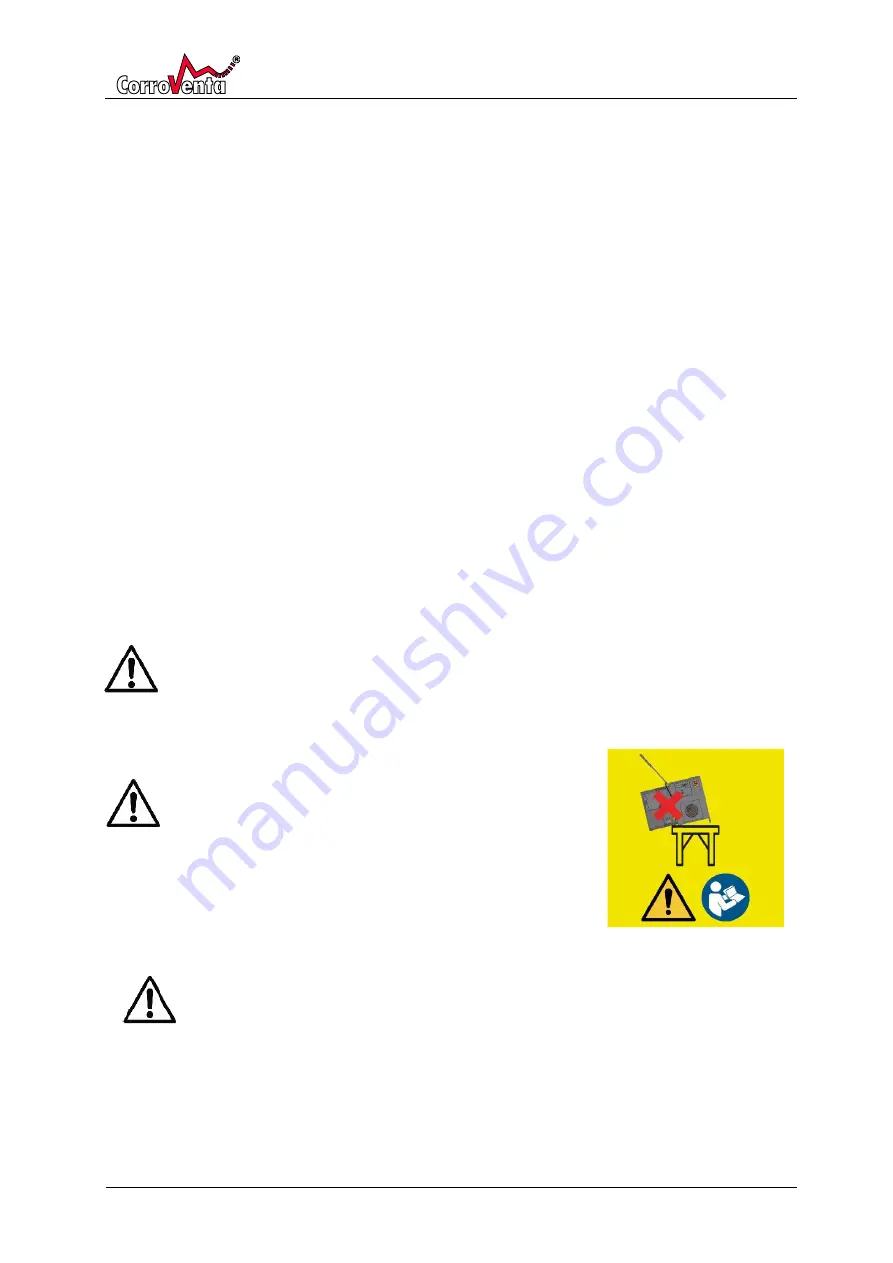
A15ES
© Corroventa Avfuktning AB
2022.05
40 (67)
Filter replacement
Filter replacement is performed as follows:
1.
Stop the machine by pushing Stop on the control panel so that the machine enters the
automatic cooling sequence.
2.
Allow the cooling sequence to finish and wait until the count down on the display has
disappeared and the fans have stopped.
3.
Turn off the mains power switch by turning it anti clockwise to position 0.
4.
Open the filter hatches and remove the old filters.
5.
Clean the filter compartments, preferably with a vacuum cleaner, so that the dust and dirt
that have fallen off the filters is removed. If left in the machine, the dust and dirt will clog the
new filters
6.
Insert the new filters and close and lock the filter hatches.
7.
Push Resume to have the machine start up with the same settings and adjustments as
before. Preferably wait by the machine a few minutes to see that the operation is normal
and that there are no alarms presented on the control panel.
Service and repair work including cleaning
For service and repair, at all times, the power must be disconnected from the
machine. Stop the machine and let it cool down. Proceed by turning off the mains
power switch and remove the power cable from the power intake. Ensure that no
other personnel reconnect power to the machine while the work is ongoing.
The rotor cassette must not be extracted when the
machine is in elevated position, such as on a lift table.
The rotor cassette is provided with a support to prevent
the machine from falling over and this feature will not
help prevent accidents if the machine is raised from the
floor.
While cleaning the machine, as dust and particles collected from the air flows are
likely to be present, use appropriate protective equipment.
The machine exterior is cleaned with a moist cloth. For the interior, use a vacuum cleaner with a
brush head to remove dust and particles. Carefully and still with the brushed head to prevent
damage to surface, the rotor is from both sides.
Summary of Contents for A15ES
Page 1: ...A15ES Corroventa Avfuktning AB 2021 11 1 67 USER MANUAL ADSORPTION DEHUMIDIFIER A15ES ...
Page 3: ...A15ES Corroventa Avfuktning AB 2021 11 3 67 ...
Page 46: ...A15ES Corroventa Avfuktning AB 2022 05 46 67 APPENDIX 1 WIRING DIAGRAM ...
Page 47: ...A15ES Corroventa Avfuktning AB 2022 05 47 67 ...
Page 48: ...A15ES Corroventa Avfuktning AB 2022 05 48 67 ...
Page 49: ...A15ES Corroventa Avfuktning AB 2022 05 49 67 ...
Page 50: ...A15ES Corroventa Avfuktning AB 2022 05 50 67 ...
Page 51: ...A15ES Corroventa Avfuktning AB 2022 05 51 67 ...
Page 52: ...A15ES Corroventa Avfuktning AB 2022 05 52 67 ...
Page 53: ...A15ES Corroventa Avfuktning AB 2022 05 53 67 ...
Page 54: ...A15ES Corroventa Avfuktning AB 2022 05 54 67 ...
Page 55: ...A15ES Corroventa Avfuktning AB 2022 05 55 67 ...
Page 56: ...A15ES Corroventa Avfuktning AB 2022 05 56 67 ...
Page 57: ...A15ES Corroventa Avfuktning AB 2022 05 57 67 ...
Page 58: ...A15ES Corroventa Avfuktning AB 2022 05 58 67 ...
Page 59: ...A15ES Corroventa Avfuktning AB 2022 05 59 67 ...
Page 60: ...A15ES Corroventa Avfuktning AB 2022 05 60 67 ...
Page 61: ...A15ES Corroventa Avfuktning AB 2022 05 61 67 ...
Page 62: ...A15ES Corroventa Avfuktning AB 2022 05 62 67 ...
Page 63: ...A15ES Corroventa Avfuktning AB 2022 05 63 67 ...
Page 64: ...A15ES Corroventa Avfuktning AB 2022 05 64 67 ...
Page 65: ...A15ES Corroventa Avfuktning AB 2022 05 65 67 ...
Page 66: ...A15ES Corroventa Avfuktning AB 2022 05 66 67 ...
Page 67: ...A15ES Corroventa Avfuktning AB 2022 05 67 67 ...