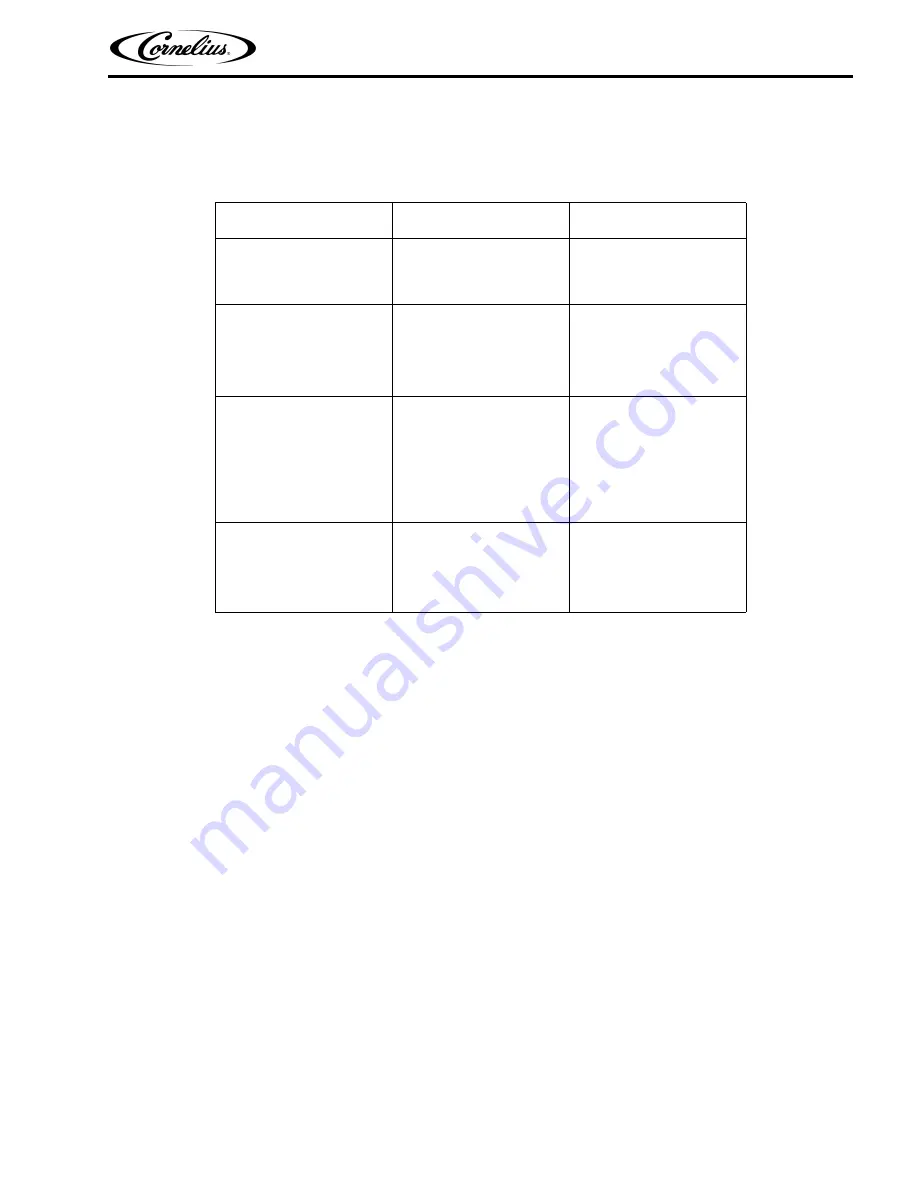
Viper Installation Manual
© 2010-2016, Cornelius Inc.
- 29 -
Publication Number: 621360041TBINS
TROUBLESHOOTING
Table 20.
Problem
Probable Cause
Remedy
Unit will not run.
A.
Unit not plugged in
B.
Circuit breaker
A.
Plug in unit.
B.
Reset/replace circuit
breaker
“Sleep” display on Bar-
rel Status menu
A.
Sleep time set
B.
Clock incorrectly set
C.
No or incorrect
wakeup time set
A.
Check programming
B.
Check programming
C.
Check programming
Barrel Status OFF
A.
Not activated
B.
Error has shut down
barrels
C.
Unit in diagnostics
A.
Turn barrels to ON or
SPIN
B.
Correct error & turn
barrels to ON
C.
Exit diagnostics &
turn barrels ON
No water pressure
A.
Water source not
turned on
B.
Filter blocked
C.
Other
A.
Turn on water
B.
Change filter
C.
Call Service
Summary of Contents for VIPER 3 FLAVOR
Page 35: ......