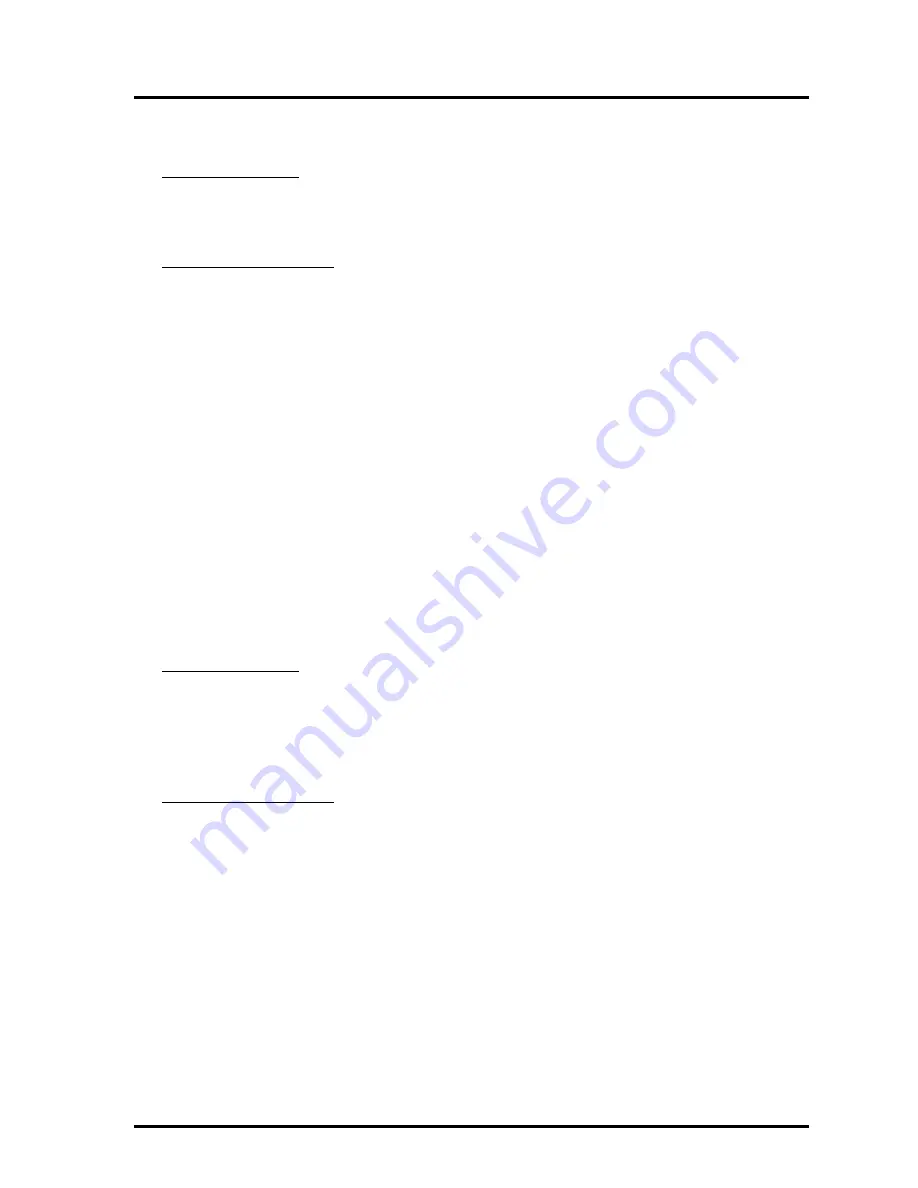
Automated Beverage System
© 1999 The Coca-Cola Company, Cornelius and
McDonald’s Corporation. All Rights Reserved.
49
22. Syrup Tank Systems.
A. Connect a syrup tank filled with potable water and pressurized at 60 to 80 PSI, into one of the
syrup systems.
23. Bag-In-Box Syrup System.
A. Place all syrup outlet tubes, with bag valves on, into a container of potable water.
24. Flush the sanitizing solution from the syrup system and the dispensing valve as follows:
A. Place a waste container under dispensing valve.
B. Place the ABS unit in the TEST/VALVE TEST mode and press each flavor button until all the
sanitizer is expelled and water fills the tubing. Activate the dispensing valve for one minute to
purge all the sanitizing solution out of the syrup system and the dispensing valve.
C. Continue to activate each dispensing valve in cycles (ON for 15 seconds, OFF, then ON for 15
seconds). Repeat ON and OFF cycles for 15 cycles.
25. Repeat Steps 22, 23 and 24 to flush sanitizing solution out of the remaining syrup systems and
dispensing valve.
26. Remove the potable water source from the syrup system.
S
TEP
5: P
URGE
THE
W
ATER
O
UT
OF
THE
S
YRUP
S
YSTEMS
TO
R
ESTORE
U
NIT
O
PERATION
27. Syrup Tank Systems.
A. Noting syrup tanks CO
2
regulator pressure setting observed in Step 4 preceding, re-adjust
CO
2
regulator to the observed pressure setting.
B. Connect the tanks containing the syrup into the syrup systems.
28. Bag-In-Box Syrup System.
A. Remove all bag valves from syrup outlet tubes.
B. Connect bag-in-box syrup containers into the syrup systems.
29. Place a waste container under the dispensing valve. dispense from all dispensing valve to permit
the syrup to purge all the potable water from the syrup systems and the dispensing valves.
Continue to dispense from the dispensing valves until only the syrup is dispensed from the syrup
systems and valve.
30. Dispose of waste sanitizing solution in a sanitary sewer, not in a storm drain, then thoroughly rinse
the inside and outside of the container that was used for sanitizing solution to remove all sanitizing
solution residue.
Quarterly Cleaning/Sanitation Procedures