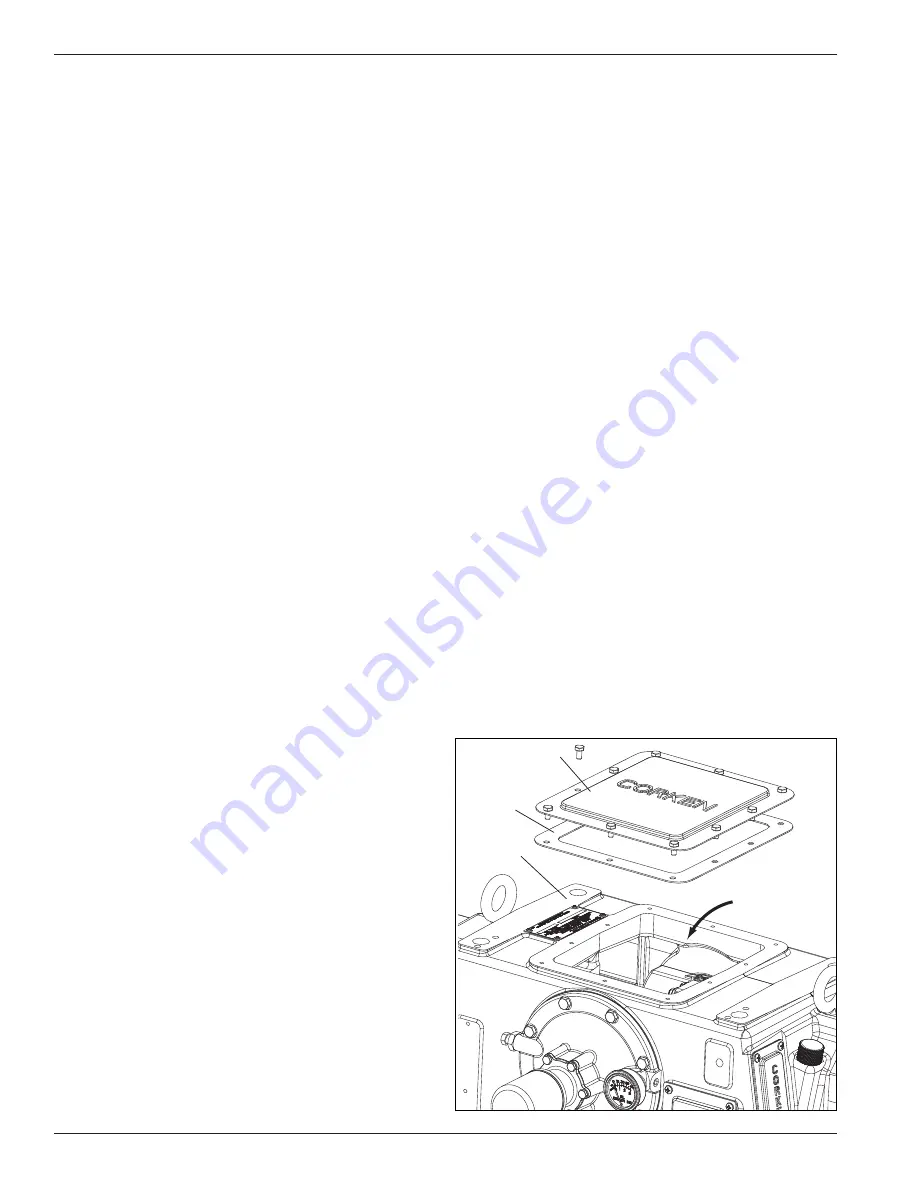
If the compressor is equipped with a liquid trap not
manufactured by Corken, make sure it is adequately
sized; otherwise, it may not be able to remove the liquid
entrained in the suction stream.
Corken’s liquid trap provides the most thorough liquid
separation (see figure 1.4) and is American Society of
Mechanical Engineers (ASME) code stamped. It contains:
• Manual drain valve.
• Relief valve designed according to the ASME code to
protect the vessel
• Pressure gauge with isolation needle valve
• Two (2) level switches: one for alarm and one for
shutdown. In some cases, the alarm switch is used to
activate a dump valve (not included with trap) or sound
an alarm so the operator can drain the trap using the
manual drain valve at the bottom of the trap.
• This trap also contains a mist pad. A mist pad is a mesh
of interwoven wire designed to remove fine liquid mists.
NOTE: The liquid level switches MUST be removed
from the trap before grounding any welding devices
to the trap or associated piping . Failure to do so will
damage the switch contacts!
2 .5 Driver Installation and Flywheels
Corken compressors may be driven by either electric
motors or internal combustion engines (e.g. gasoline,
diesel, natural gas, etc.). They are usually V-belt driven.
The fly wheel has dual purpose it is sheave for the
V-belts and for compressor speed variation reduction.
The electric motor wiring is extremely important and
must be done by a competent electrician. Low voltage
or improper wiring of the motor will result in expensive
consequences. If there is a low voltage problem, call the
power company.
Humid climates can cause problems with explosion
proof motors. Explosion proof and TEFC motors are
designed to expand and contract due temperature
changes. This allows air to enter and exit the enclosures.
The moist air inside the motor can condense and if
enough water accumulates, the motor will fail.
To prevent this two method can be followed
• Make a practice of running the motor at least once
a week on a bright, dry day for an hour. During this
period of time, the motor will heat up and vaporize the
condensed moisture.
• Motor space heaters are recommended which need to
be powered at all times to vaporize the any moisture.
NOTE: No motor manufacturer will guarantee their
explosion proof or totally enclosed (TEFC) motor
against damage from moisture .
Drivers should be selected so the compressor operates
between 400 and 1200 RPM. The unit must not
be operated without the flywheel or severe torsional
imbalances will result causing vibration and a high
horsepower requirement. The flywheel should never
be replaced unless it has a higher wk2 value than the
flywheel supplied from factory.
For installation with engine drivers, thoroughly review
instructions from the engine manufacturer to assure the
unit is properly installed.
2 .6 Crankcase Lubrication
The crankcase was drained before shipment. Before
starting the machine, fill the crankcase to the full mark
on the oil bayonet and not above. To ensure proper
lubrication of the crankcase parts, the crankcase should
be filled through the crankcase inspection plate (see
figure 2.6A for the proper oil filling location).
General Notes on Crankcase Oil
Corken gas compressors handle a wide variety of
gases in a multitude of operating conditions. They
are used in all areas of the world from hot dusty
deserts, to humid coastal areas, to cold arctic climates.
Some compressors may be lightly loaded and run
only occasionally, while others may be heavily loaded
and operate 24/7. Thus, no single crankcase oil or
maintenance schedule is right for every compressor.
Availability of brands and grades of oil can vary from
one location to another. These factors can make it
Figure 2.6A
Inspection plate
Inspection plate
gasket
Crankcase
Fill crankcase
through this opening
8