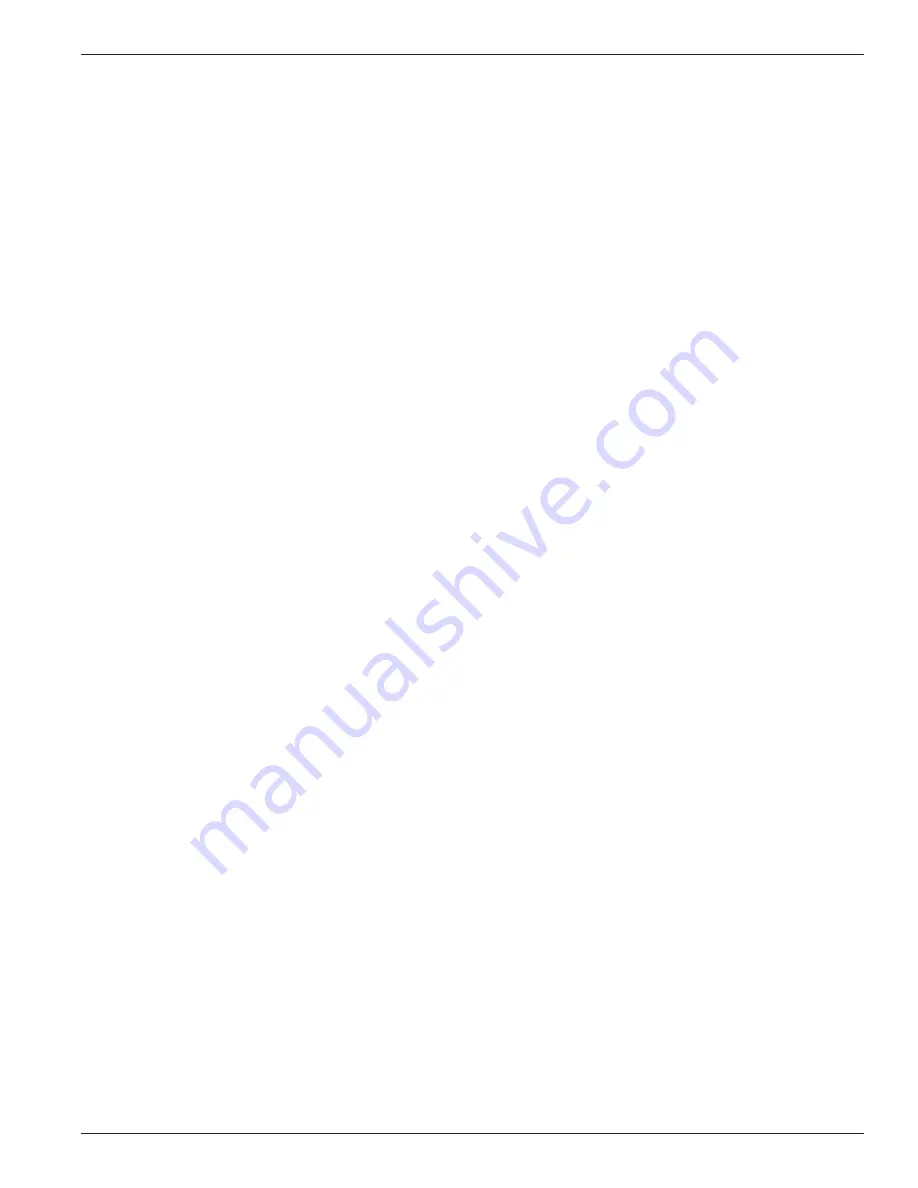
Ammonia Service
Compressing ammonia presents particular challenges
from a lubrication standpoint. Never use a detergent
oil in a compressor in ammonia service. Ammonia will
react with the detergent and cause lubrication failure.
Fortunately, some oils are specifically blended for use in
ammonia compressors — though some of these are best
suited only for cooler climates.
Consult these charts or the oil manufacturer’s product
data sheet for information regarding the oil’s viscosity,
viscosity index, pour point, etc. This information is
generally available on line or from the oil supplier. Do not
use an oil if it’s critical properties can not be confirmed,
of if there is any other reason to doubt its suitability.
Contact Corken if additional assistance is needed when
selecting a crankcase oil.
Oil Change Intervals
Oil change intervals can vary significantly depending
on local environmental conditions, the gas being
compressed, and the oil being used. Unless there are
factors that shorten the life of the oil, the following
recommendations apply:
Conventional oil: 2200 hours or 6 months—whichever
comes first
Synthetic oil: 6000–8000 hours* or one year—whichever
comes first
* Oil change intervals in this range should be confirmed via oil analysis.
Environmental or operational issues such as dirty/dusty or
humid conditions will require more frequent oil changes.
Contamination/dilution of the oil by liquids in the gas stream
can also shorten the life of the oil. Visually check the oil level
and the oil condition at least monthly (compare to unused oil).
Indications that dictate more frequent oil changes:
• Unusually dirty or discolored oil (or unusual smell)
• Oil dilution by condensation or other liquids in the gas
stream (see below)
• Change in viscosity for any reason (various oil additives
can break down over time)
• Changing ambient temperature may cause the need for
a different viscosity
The oil should be changed as often as necessary to
maintain clean, undiluted oil of the proper viscosity. Each
time the oil is changed, the oil filter (Corken part number
4225) should also be changed.
Oil analysis
The best way to determine the needed oil change interval
for any particular compressor is to have an oil analysis
conducted. Numerous labs can analyze a used oil sample
and advise its condition. After 2–3 such tests, a determination
can be made for a recommended oil change interval for a
particular compressor in its specific environmental situation
and operating conditions. Regular oil analysis can help
improve the compressor durability and decrease oil usage
by maximizing the oil change intervals. Based on the oil
analysis, the oil can be changed when it is needed, and not
changed when it is not yet necessary.
Oil dilution
Crankcase oil can be diluted by various products in the
gas stream. As an example, when compressing butane
in winter, the vapor pressure is very low and there can
be a lot of entrained liquid butane with the gas stream.
This liquid can collect in the compressor and dilute the
crankcase oil. This thins the oil and reduces its ability to
properly lubricate the compressor.
Hydrocarbon mixtures containing heavy hydrocarbons
such as butane, pentane, hexane, etc. often operate
at pressure above the vapor pressure of these heavier
constituents. Thus, they often produce a “wet” gas which
can dilute the crankcase oil.
Long term storage
When a compressor is removed from long term
storage, the oil should be changed before putting the
compressor back into service. Specifically, if it has
been unused over a season (such as over a winter), the
oil should be changed.
Crankcase Oil Heater Option
Corken offers a crankcase oil heater as an option on
all models except the small model 91. This heater is
available in 110V and 220V versions and is rated for Class
1, Division 1 and 2, Group B, C, D service. The heater
includes a thermostat set at 70°F (21.1°C). The heater
alleviates concerns about cold weather startup. When
using the heater, an ISO 100 viscosity oil will do well
regardless of low ambient temperature.
Note that all Corken HG600 compressors come ready to
accept the optional heater.
Cylinder Lubricating Oil
All Corken gas compressors are designed to operate
without cylinder lubrication. However, many Corken
Customers, particularly in the oil and gas industry, use
lubricated compressor cylinders to extend the service
life of the compressor’s valves, piston rings, and packing.
Compressor cylinders operate at higher temperatures
than the crankcase, so oils used in this service often have
a higher viscosity than the crankcase oil. A viscosity of
ISO 150 (or higher) is common for cylinder lube oil. Several
companies make oil specifically designed for this service
and many of these oils have properties that inhibit dilution
or washing away of the oil by condensates in the process
11