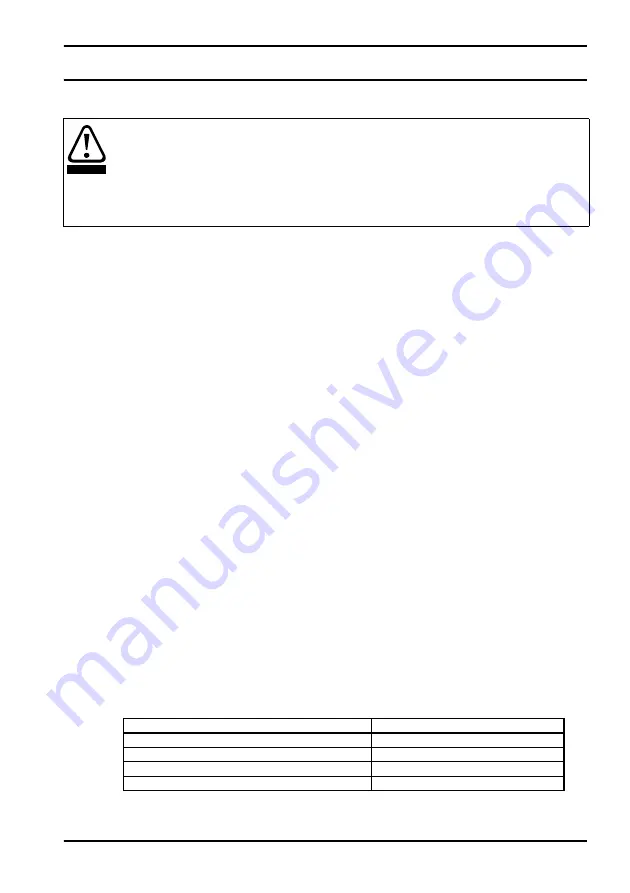
SM-Universal Encoder Plus User Guide
37
Issue Number: 6
www.controltechniques.com
6
Getting Started
6.1
Installation
Encoder connections
In order to ensure correct operation there are a number of checks which should be
carried out:
•
Ensure the encoder is securely mounted to the motor as spurious operation can
result due to the encoder slipping whilst the motor is rotating.
•
Ensure encoder connections to both the encoder and the Solutions Module
terminals are secured, intermittent connections can result in spurious operation or
the Solutions Module not detecting the feedback signals.
•
Ensure screen and grounding recommendations as specified in Chapter
5.5
on page 28, Encoder, Shield connections of this
User guide are followed to prevent noise being induced on the encoder feedback
signals. Noise induced on encoder feedback cables cannot only result in spurious
operation but in extreme cases can result in encoder failure and/or damage to the
Solutions Modules encoder input.
Encoder feedback and communications data is transmitted from an encoder as low
voltage analogue or digital signals. Ensure that electrical noise from the drive or motor
does not adversely affect the encoder feedback. Also refer to drive and motor
instructions given in Chapter 4
Electrical Installation
in the
Unidrive SP User Guide
, and
that the encoder feedback wiring and shielding recommendations are followed in
section 5.5
Encoder initialisation
Encoder initialisation will occur as follows: at drive power-up, when requested by the user
via Pr
3.47
or when trips in this module (which are option module specific) are reset.
Initialisation causes an encoder with comms to be re-initialised and auto-configuration to
be performed if selected. After initialisation Ab.SErvo, Fd.SErvo, Fr.SErvo and SC.SErvo
encoders will use the UVW commutations signals to give position feedback for the first
120
°
(electrical) of rotation when the motor is restarted.
A delay is provided during initialisation for some encoders to allow the encoder to be
ready to provide position information after it has powered up. The delay is provided
during initialisation because this occurs during drive power-up and after encoder power
supply trips are reset. The delays are as follows:
The control circuits are isolated from the power circuits in the drive by basic insulation
only, as specified in IEC60664-1. The installer must ensure that the external control
circuits are insulated from human contact by at least one layer of insulation rated for use
at the AC supply voltage.
If the control circuits are to be connected to other circuits classified as Safety Extra Low
Voltage (SELV) (e.g. to a personal computer) an additional isolating barrier must be
included in order to maintain the SELV classification.
WARNING
Encoder type
Initialisation delay
Ab, Fd, Fr, Ab.SErvo, Fd.SErvo, Fr.SErvo, SC.SErvo 250ms
SC.HiPEr
150ms, then encoder reset, then 400ms
SC.EndAt, EndAt
1.25s
All other types
1.45s