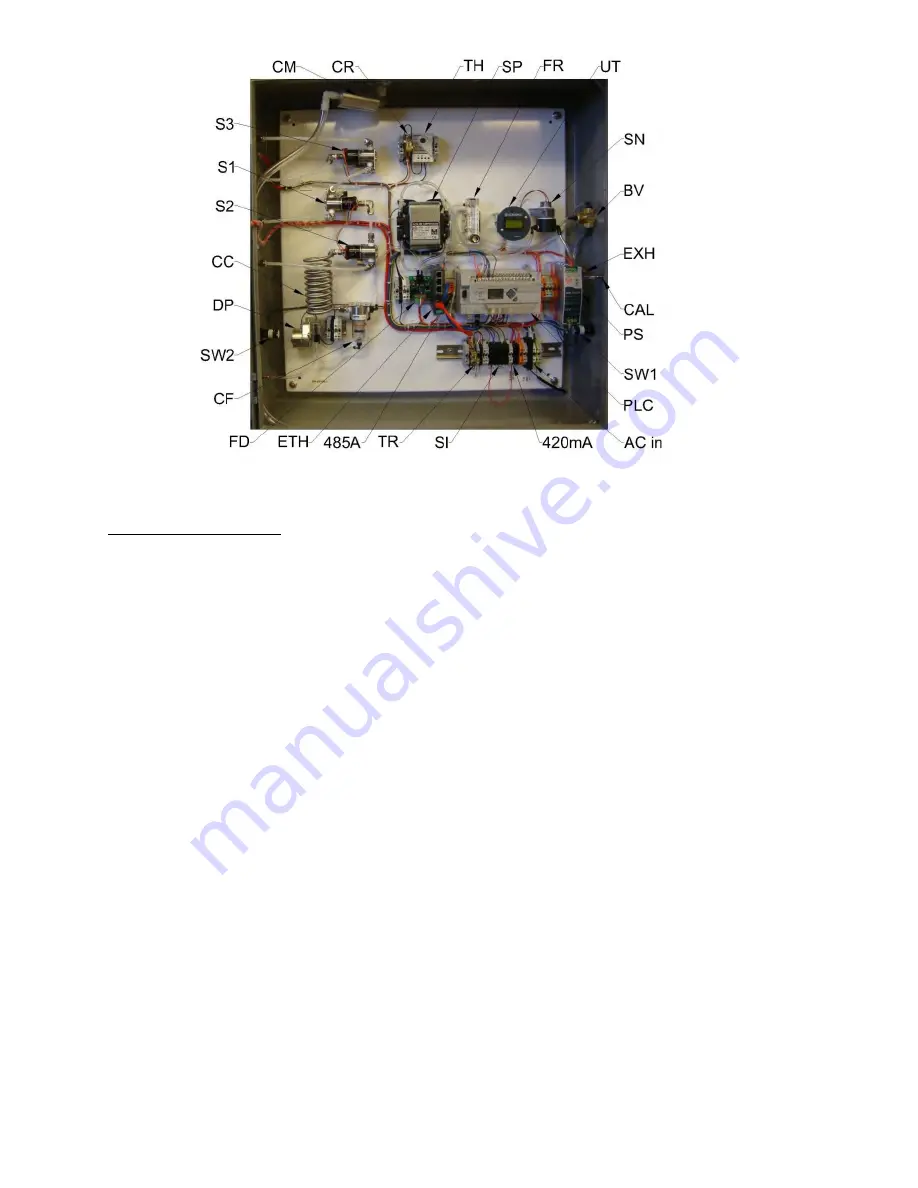
2
Figure 1: CS0352-MP Components
CS0352-MP Components – Labels, Descriptions, and Part Numbers
PLC
PS
UT
SN
FD
SP
SW1
DP
SW2
ETH
485A
S1
S2
S3
TH
TR
CR
FR
CF
CC
BV
CAL
EXH
ACin
SI
420mA
Allen Bradley 1400
Meanwell 24VDC 5A Supply
500PPM CO Detector Card
1000PPM CO Sensor
Flow Detector Card
120Vac 12 LPM Sample Pump
Sample Pump Switch
115Vac Peristaltic Drain Pump
Drain Pump Switch
Moxa Ethernet Switch
RS485 to Serial Adaptor
Probe Select Solenoid
Pressure Release Solenoid
H.P. Blow Back Solenoid
Thermostat
Trouble Relay
Cooler Solenoid Relay
.4-5.0LPM Flow Regulator
Coalescing Filter
Cooling Coil
3-way Ball Valve (Calibration)
Calibration Port
Exhaust Port
120VAC Supply Input
System Inputs
4-20mA CO Level Output
1766-L32BWA
SDR-120-24
900732-03
P2261-3
900724
AL-6SB
P1907-SL
SP101R.104
P1907-SL
EDS-205
1763-NC01
3CBX4S-Y-24VDC
3CBX4S-Y-24VDC
3CBX4S-Y-24VDC
Vortex 747 System
814-3028
814-3028
FL2013
2383T47
Non Inventory Item
46095K41
DMA3
DMA3
N/A
N/A
N/A