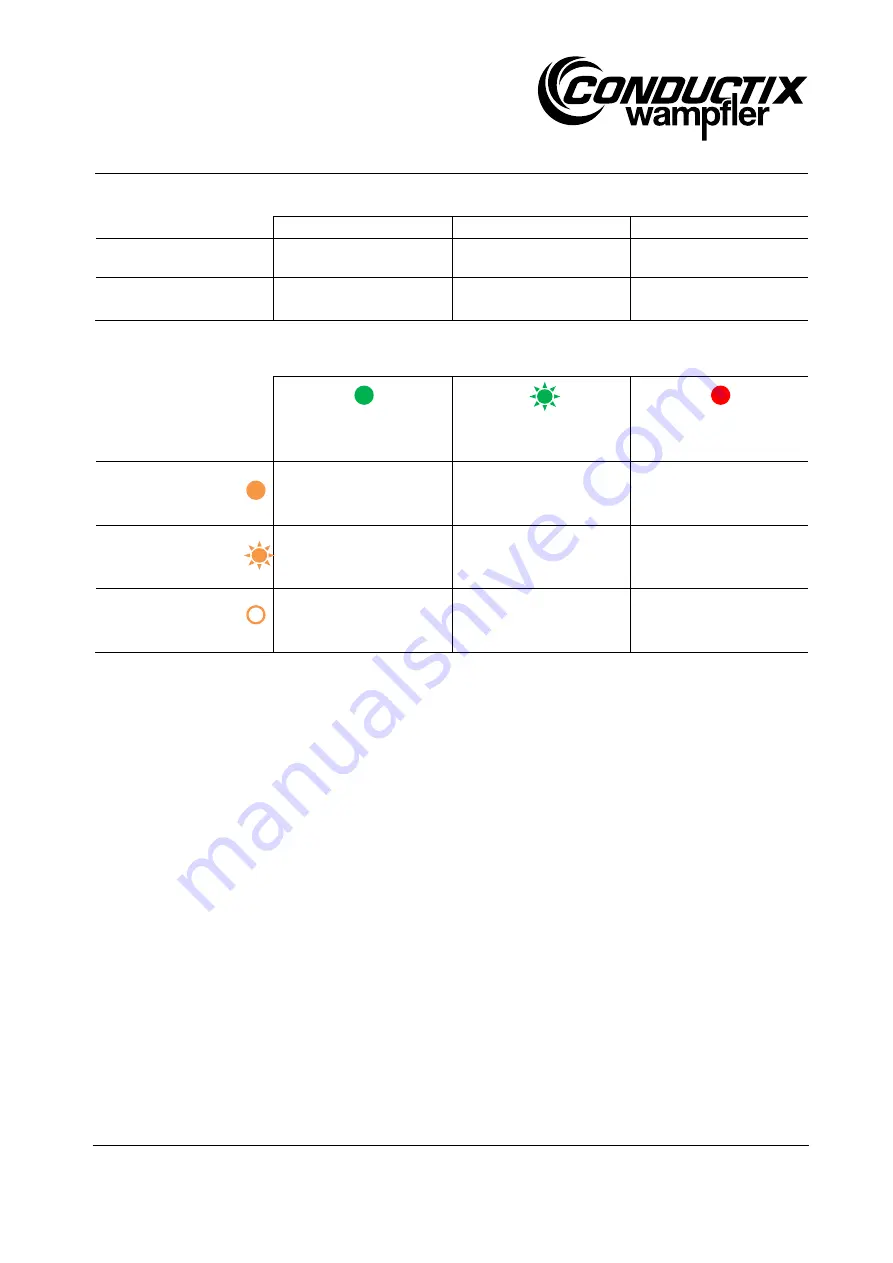
Operating Instructions
750 W 27 V pickup
CQF 04/2 + Interface M12
BAL9100-0145a-EN
www.conductix.com
translated document
Page 34 of 40
Status relay closed
Status relay open
Error relay open
Alert relay closed
See a) or b)
See c)
See d)
Alert relay open
Normal operation:
See chapter 10.2
Normal operation:
See chapter 10.2
See e)
Table 1 Relay outputs and their meaning
Green LED on
(Status relay closed)
Green LED flashes
(Status relay open)
Red LED on
Orange LED
on
(Alert relay closed)
See a)
--
--
Orange LED
flashes
(Alert relay closed)
See b)
See c)
See d)
Orange LED
off
(Alert relay open)
Normal operation:
See chapter 10.2
Normal operation:
See chapter 10.2
See e)
Table 2 LED displays and their meaning
a)
The maximum available peak power has been exceeded. Set according to the chapters 4.1. 7.5 and 8.3 ensure the
retrieved performance matches the possible performance.
b)
The internal device temperature is approaching the maximum. If the average retrieved performance does not exceed the
specified values according to the sections 4.1, 4.2, 7.5, the alert will have no immediate consequences and operation will
continue. If, on the other hand, such an alert persists for a long period of time and has never been present before, this can
be indicative, for example, of severe soiling of the heat sink (note also chapter 11). Without corrective action, this can result
in a temperature error (see case d).
c)
Automatic shutdown via the pilot contact function, with disconnected connecting cable.
d)
The max. permissible internal device temperature has been exceeded. The alert (LED flashing and alert relay closed)
persists until it falls below a reasonable temperature value. The device itself remains in error status until a reset has
occurred (see chapter 10.4). Set according to the chapters 4.1. 4.2 and 7.5 ensure the retrieved performance matches the
possible performance.
e)
The device has been shut down automatically. More about this in the chapter 4.3. If the cause of the error is detected and
eliminated, carry out a reset (see chapter 10.4). If the error cannot be attributed to external influences, the device is not
ready for operation and must be examined by a specialist. Details on the procedure can be found in the chapter 12.