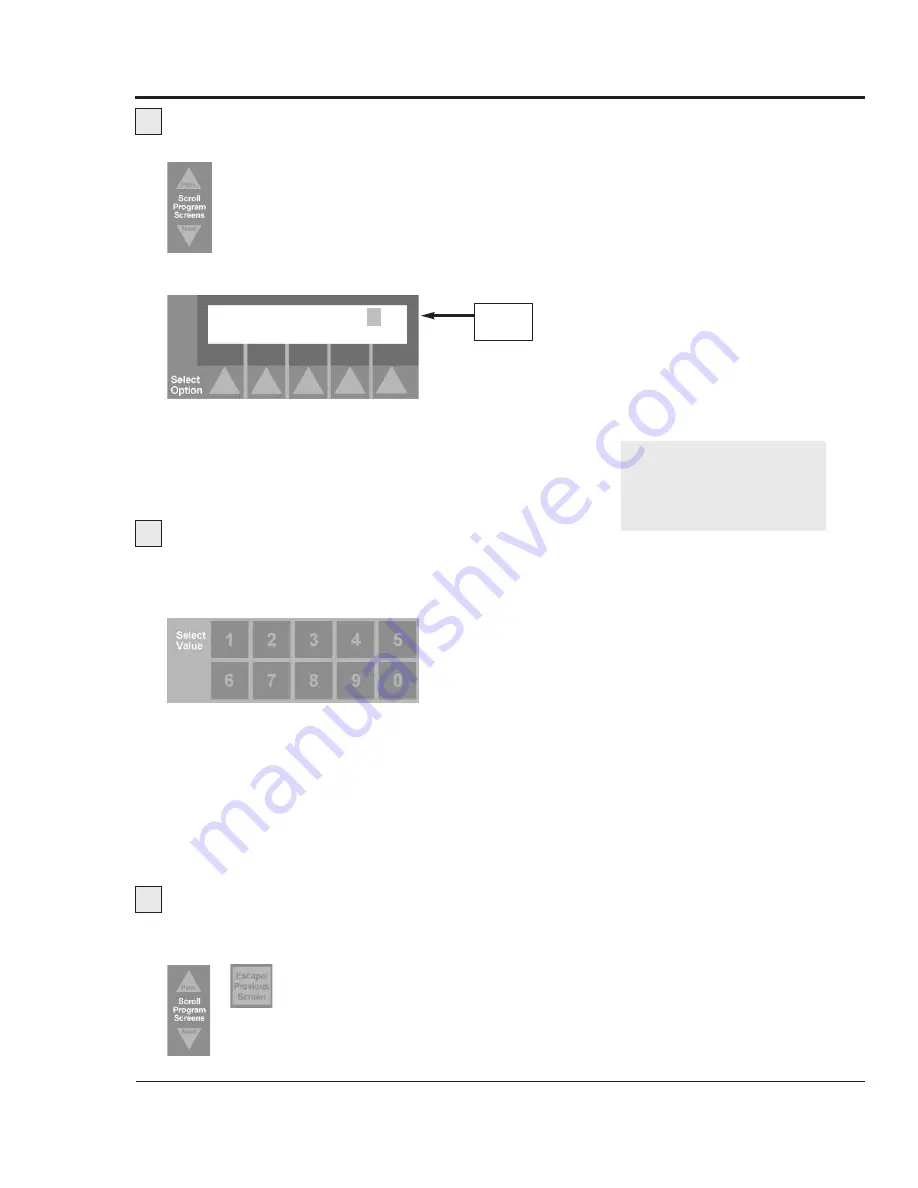
UGH017/0500
Series 1 Portable Chillers, PLC Control
O
PERATION
4-13
Press the Up/Down Scroll arrows to scroll
through the setup screens.
Stop when you get to the Percent Glycol screen:
NOTE: If you are using
water as the coolant, set
the Percent Glycol to
zero on the control.
NOTE: This screen has password protection. You can
change the percent glycol only if you have clearance. A
screen displays:
$316 Password level invalid...
The password screen then displays, asking for the pass-
word. Enter the password, then press the Enter button.
You now have password access for five minutes.
Otherwise, press the Escape button to return to the Main
screen.
Press the Scroll arrows to scroll to the
next Setup screen, or press the Escape/Previous Screen
button to return to the main screen.
4
The screen displays the percent of glycol by volume cur-
rently used. This number is flashing. The screen also dis-
plays the low temperature cutout (If the To Process fluid
drops below this temperature, an alarm condition occurs
and the compressor shuts off.)
Use the numeric keypad to set the percent
glycol. Make sure the percent you enter is the same as the
percent mixture you added to the chiller. See Filling with
Glycol Coolant, in the Installation section.
2
number
flashes
% E.G. BY VOL
0
%
Low Temp Cutout 36F
3
S
ETTING
P
ERCENT
G
LYCOL
CONT
’
D