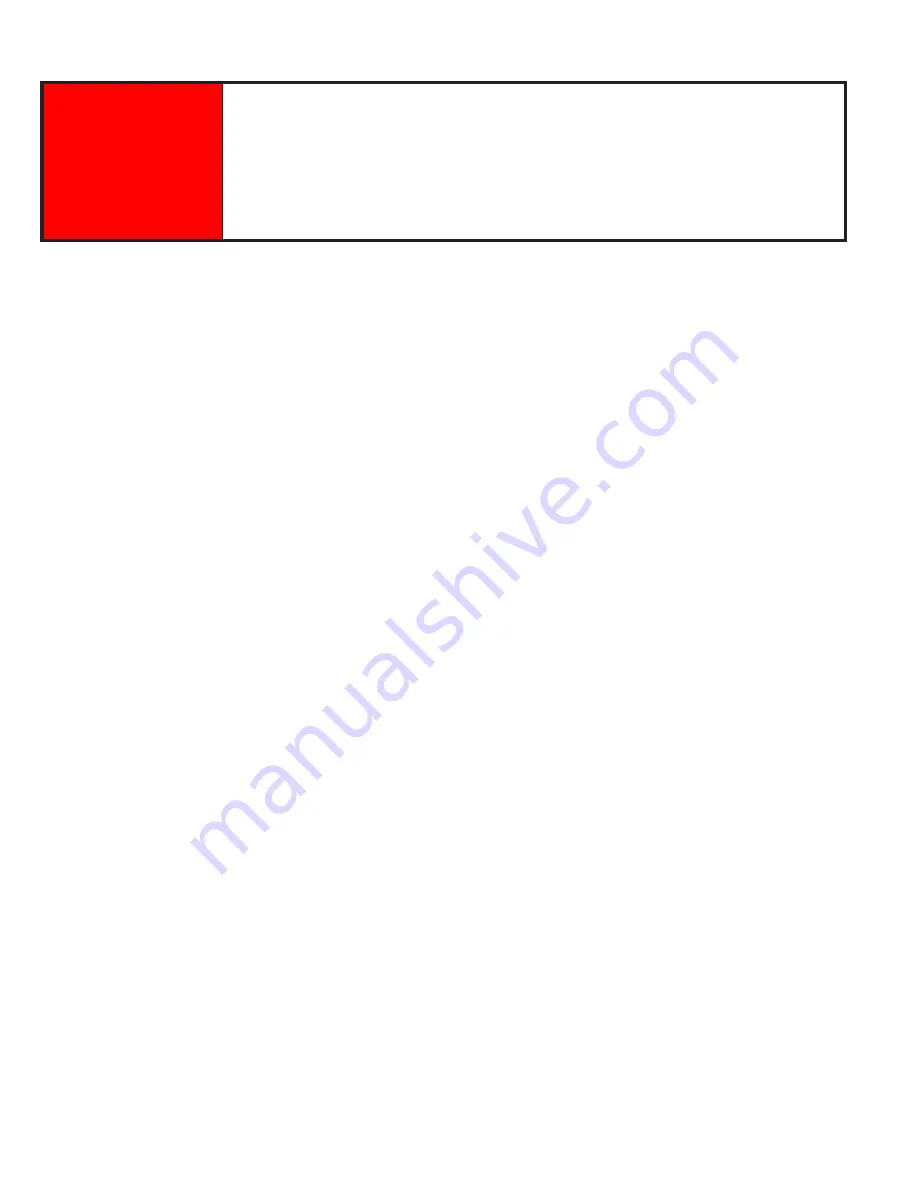
AIR/OIL SEPARATOR
The air/oil separator should be changed every 2000
hours, or when there is excessive oil vapor in the
discharge air.
SEPARATOR ELEMENT REPLACEMENT
1. Switch off the unit and disconnect the power to
prevent accidental starting.
2. Allow one minute after stopping for the system to
settle and the pressure to be relieved.
3. Using a strap wrench, remove the old element and
gasket.
4. Clean the gasket surface with a clean rag.
5. Apply a light film of oil to the new gasket.
6. Hand tighten the new element until the new gasket
is seated in the gasket groove.
7. Continue tightening by hand and additional
½ to ¾ turn.
8. Reconnect power and restart the machine
to check for leaks
9.
10.
LUBRICANT
Your compressor has been filled and tested with CAS
RS8000, a high quality compressor lubricant. It is
a PAO with the advantage of extended service life,
high temperature operation, easy start-up when cold,
reduced sludge and lacquer buildup, and is completely
compatible with all seals, gaskets, and other compressor
materials.
LUBRICANT SPECIFICATIONS
If you choose not to use CAS RS8000, for optimum life
and warranty service your lubricant must meet the
following specification:
Grade ISO
46
Viscosity@100oF,cST 46
Viscosity@210oF,cST 7.93
Viscosity Index
100 or more
Pour Point, F
-20 or less
Flash Point, F
400 or more
Fire Point, F
450 or more
Rust Test ASTM-FG-665 A&B
Pass
Oxidation Test, ASTM0-D943
1500
Emulsion Test, ASTM-D1401
10 Min.
Foam Test, ASTM
Pass
OIL ANALYSIS
Oil analysis is an excellent tool to add to your
compressor maintenance program. At regular intervals
you submit lubricant samples to a qualified laboratory.
From this you receive a detailed report showing the
lubricant condition, wear metals, and contaminants.
Changes in this information over time provides the
basis for predictive compressor maintenance. Saving
you unplanned machine downtime and unnecessary oil
changes.
CAUTION
DANGER
!!
!
Hot oil under pressure will cause severe injury, death, or property
damage.
Be sure the compressor is shutdown and pressure relieved before
attempting to remove the oil filter, separator, oil fill, or change the oil.
Compressed Air Systems, LLC 1-800-531-9656 Fax 972-352-6364 www.compressed-air-systems.com
5-15 HP Electric Rotary Screw Compressors