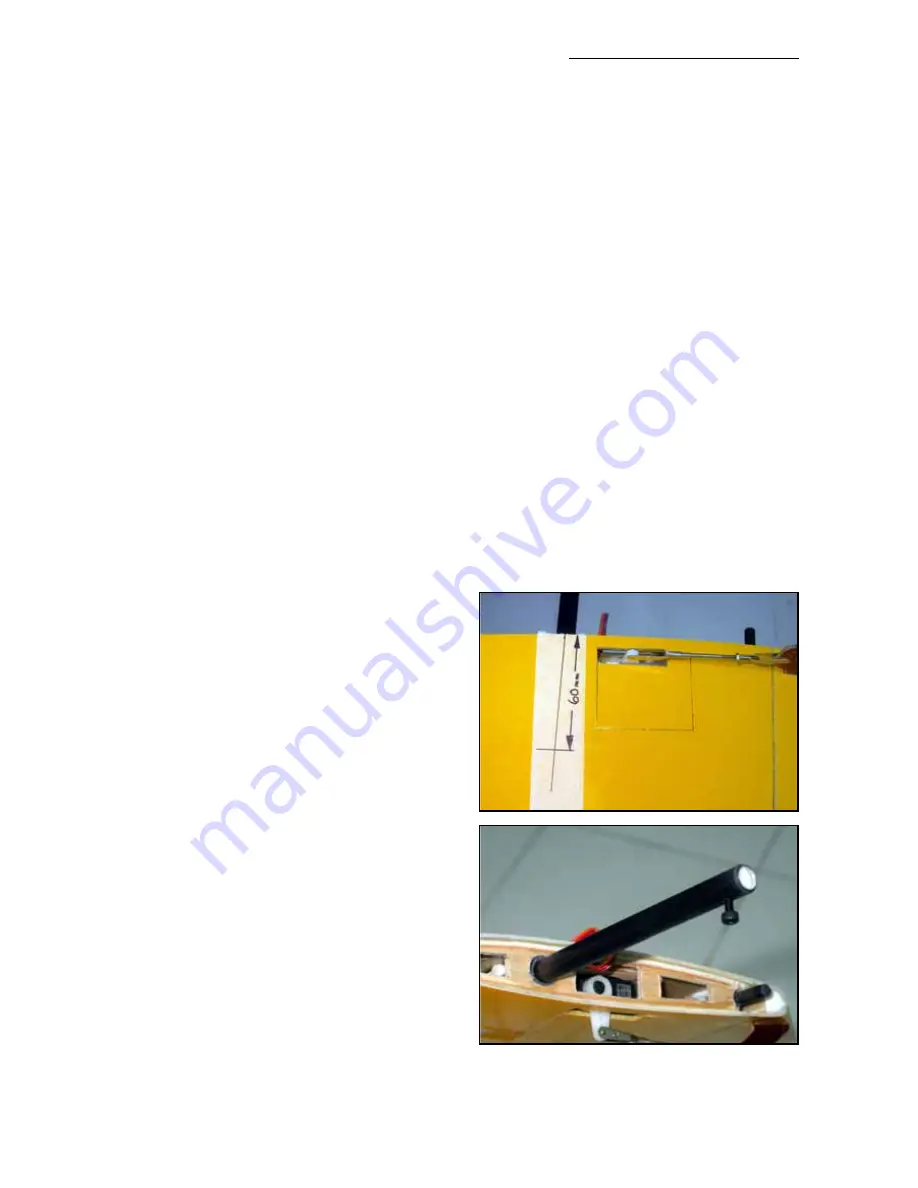
plastic nuts until cured. Open up the milled holes in the back of the root ribs of both wings so
that the short 12mmØ carbon tubes fit in easily. Wax both ends of the 10mm anti-rotation tube
where it projects outside the fuselage, the inside surface of the 2 short 12mmØ carbon tubes,
and the outside of the fuselage in this area. Sand the outer surface of the tubes to prepare for
gluing.
With the fuselage still set with the stabs at exactly 0° check the incidence of the wings. If you
milled to marked hole positions accurately on the marks set during manufacture you will find
that the wings are between 0° and +0.5° incidence. Nominally the correct incidence should be
about +0.25°. Adjust the position of the hole in the root rib until you get one wing set correctly,
apply a very thick 30 min epoxy/microballoon mix to the outside of the 12mm carbon tube and
push the wing fully into position. Secure with the plastic nut until completely cured (min. 2 hrs)
After both wing incidences are finally set correctly, remove the wings and check the glue joint
around the carbon tubes. Apply more epoxy mix as needed to secure properly.
0° - 0° Datum line:
While C-ARF prefer and advise to use the above method for setting the incidences, as an
alternative, you can use the horizontal 0° datum line of the fuselage to set the stab and wing
incidences. This imaginary line is positioned from the
front
edge of the cowl to fuselage joint,
to a dimension of exactly 37mm below the centreline of the 10 mmØ stab tube.
While the fuselage is set up with the stab at 0° you can also check the vertical front face of the
fuselage for the downthrust angle which should be between -2° and -2.5°.
Now you can go on to complete the wing and
stab servos and linkages as follows.
Horizontal Stabs
The stabs are 95% finished at the factory and
are elastic-hinged during manufacture, so you
only need to install servos, horns and linkages.
Glue a 20mm length of hardwood dowel into
both ends of the carbon stab tube with epoxy
and microballoons mix. Inside the stabs you will
see a small plywood reinforcement plate
between the carbon spar sleeve and the bottom
surface of the stab. Mark the bottom of both
stabs exactly in line with the centre of the carbon
tube, and in this ply plate. Nominally the centre
of the plate is 60mm from the root rib.
Install the carbon spar tube fully into 1 stab, and
drill a 2.4mm hole through the stab, the plywood
plate, sleeve and into the centre of carbon spar
tube. You will need to drill 15mm deep. Do NOT
drill right thru’ the stab tube - only through one
side of the tube into the hardwood dowel. Tap
M3, and counterbore the hole in the underside of the stab so that the M3 x 12mm bolt fits flush
with the surface and bears on the plywood plate - NOT on the composite stab structure.
Composite-ARF IMPACT
16