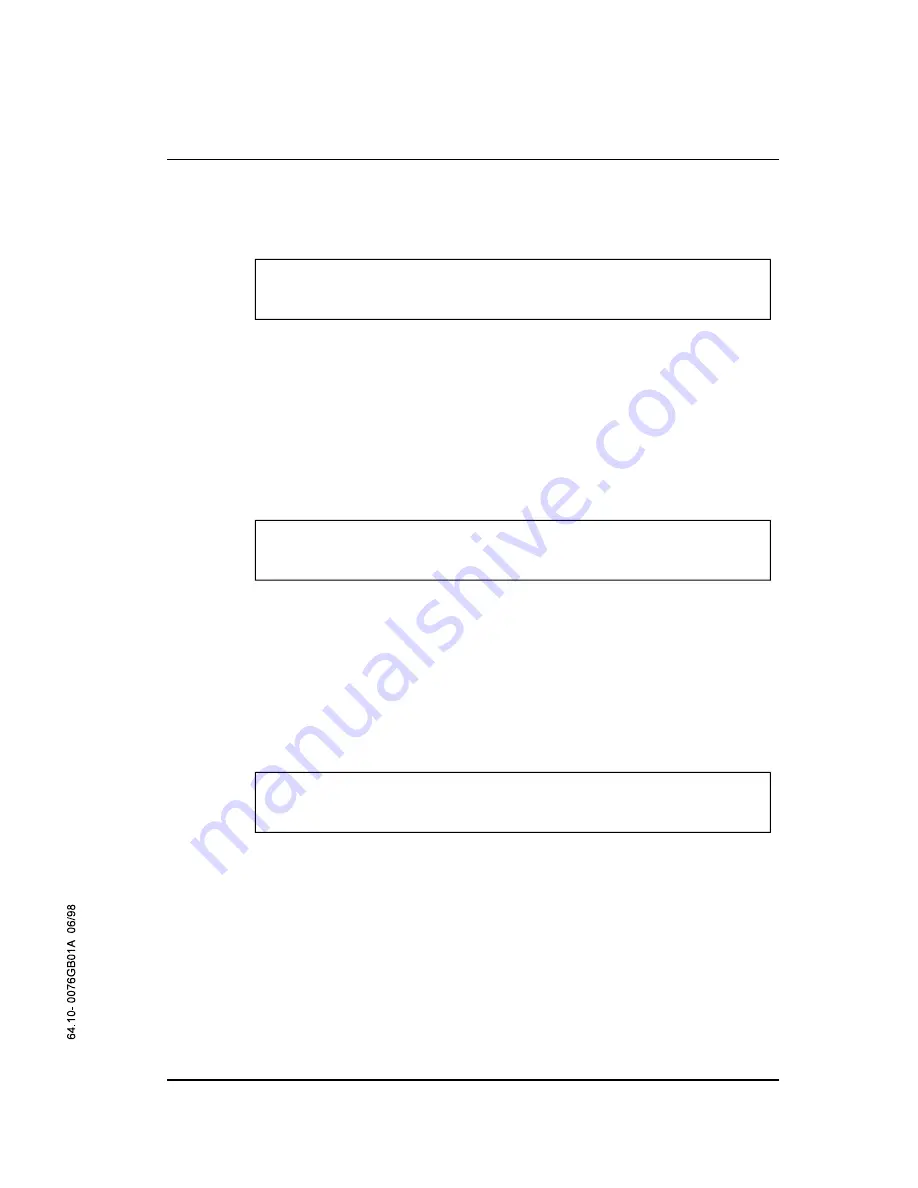
4.2. Con tin u ous Op er a tion
F
Fill at least half of the dry ing hop per with ma te rial.
4.2.1. Switching the Dryer on
Switch on the main switch of the dryer.
&
The green sig nal lamp goes on and the blower is run ning.
For op er a tion with timer clock:
Set the re lease switch at “au to matic” po si tion.
For op er a tion with out timer clock:
Set the re lease switch at “hand” po si tion.
F
Read the op er at ing man ual of the timer clock.
CTT 30 / CTT 60 / CTT 120
Start up 32