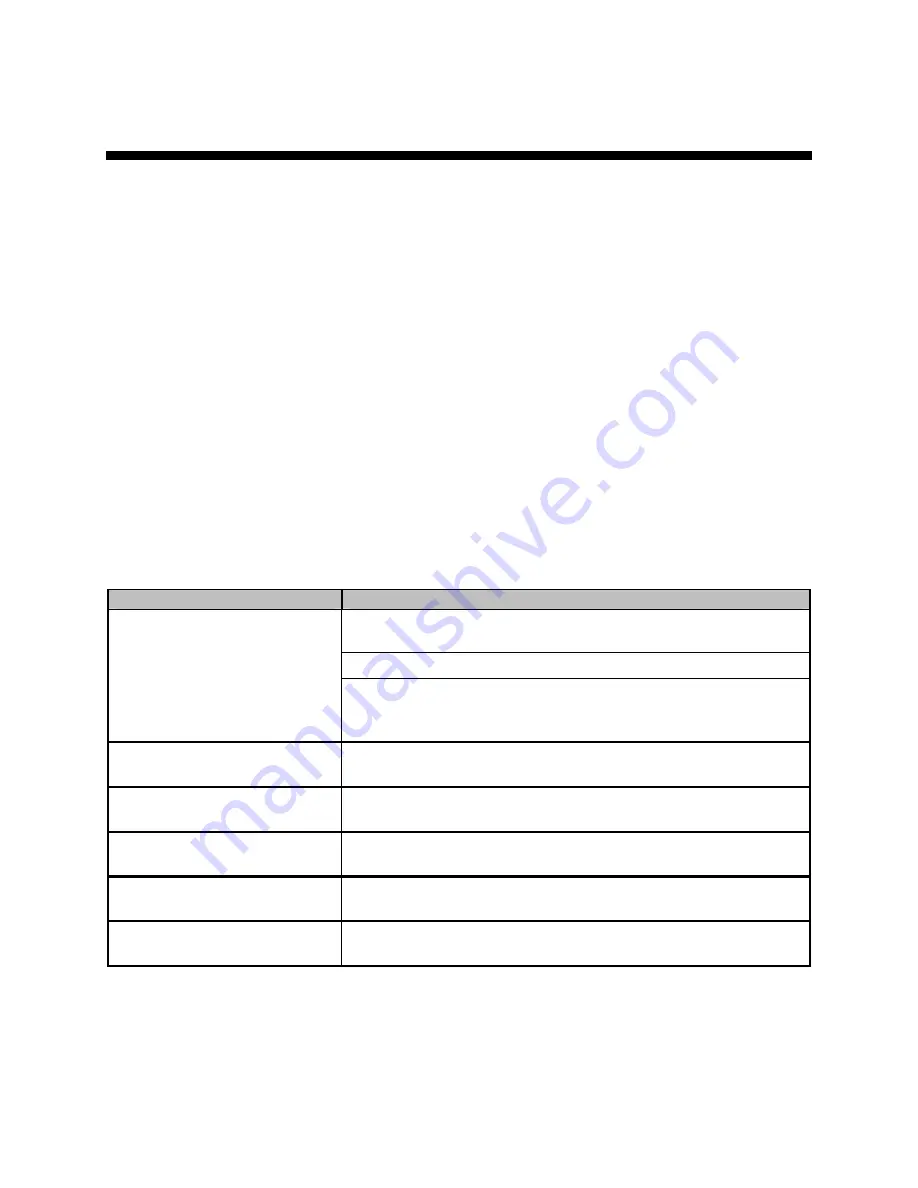
Chapter 6: Troubleshooting
6-1 Introduction
The utmost in safety precautions should be observed at all times when working on or around
the machine and the electrical components. All normal trouble-shooting must be
accomplished with the power off, line fuses removed, and with the machine tagged as out of
service.
The use of good quality test equipment cannot be over-emphasized when troubleshooting is
indicated. Use a good ammeter that can measure at least twice the AC and DC current that
can be encountered for the machine. Be sure that the voltmeter has at least minimum
impedance of 5,000 OHMS-per-volt on AC and 20,000 OHMS-per-volt on DC scales.
Popular combination meters, VOM and VTVM can be selected to provide the necessary
functions.
Before making haphazard substitutions and repairs when defective electrical components are
malfunctioning, we recommend that you check the associated circuitry and assemblies for
other defective devices. It is common to replace the obviously damaged component without
actually locating the real cause of the trouble. Such hasty substitutions will only destroy the
new component. Refer to wiring diagrams and schematics.
Locating mechanical problems, should they occur, is relatively straightforward. When
necessary, refer to the parts catalog section.
Figure 51: Typical Troubleshooting Problems and Suggested Corrective Actions
Problem
Corrective action
Check to make sure that air is hooked up and the regulator gauge
reads at precisely 60 PSI.
Check that the access door to the mixer is shut properly.
Nothing happens when I push
“Start Blender”
Look on the Recipe Screen. If you see “Mixer Full”, then check
the mixer. If the mixer is not full, then check that the mixer prox
is adjusted properly (small screw on back).
“E-STOP has been Activated”
is shown
Check the E-Stop located on the front of the blender panel.
“Interface has been Locked” is
shown
Click “Unlock” and enter in your User Password.
I’ve forgotten my User
Password
Contact the Service Department.
POWER INTERRUPTION
ALARM
Power was lost during a batch. Check your power source unless
you intentionally killed the power during the batch.
PLC Battery Low
Change out the PLC with your spare and reprogram new unit.
Send old PLC back to manufacturer for repair.
BF1-615.3
Chapter 6: 5BTroubleshooting
67 of 101
Summary of Contents for 882.00273.00
Page 22: ...Figure 11 Typical Operator Screens BF1 615 3 Chapter 2 1BFunctional Description 22 of 101...
Page 23: ...Figure 12 Typical Setup Screens BF1 615 3 Chapter 2 1BFunctional Description 23 of 101...
Page 24: ...BF1 615 3 Chapter 2 1BFunctional Description 24 of 101...
Page 75: ...Mixer Sub Assembly BF1 615 3 Chapter 7 6BAppendix 75 of 101...