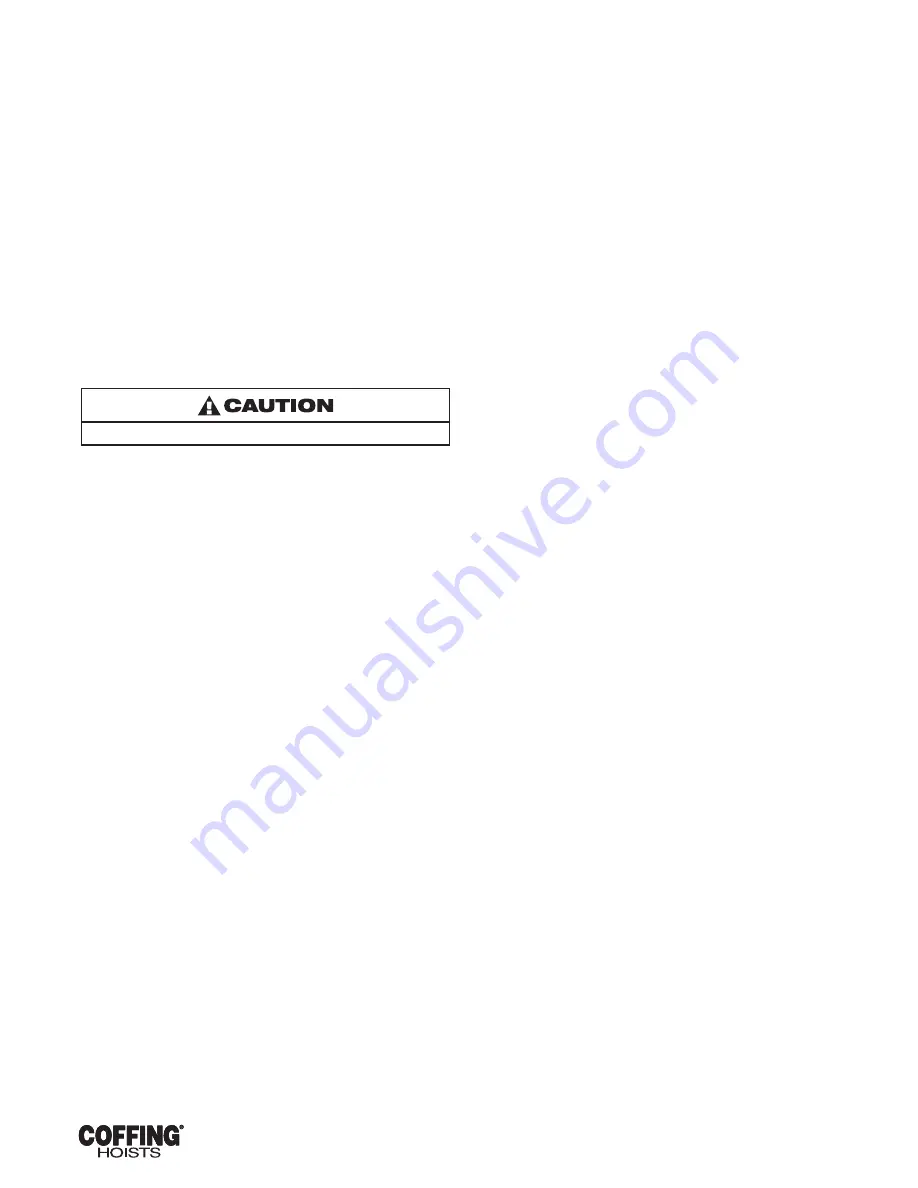
7
EC3-680-3 February 2017
Order # 5041558-0 & 5041679-0
2-3. POWER SUPPLY CONNECTION
a. Disconnect power before making connections.
b. Voltage supplied to the hoist should be within plus or minus
10% of the voltage specified for the hoist. Hoists are tagged
at the factory with a tag indicating the voltage for which the
hoist is wired. Standard single-speed, three-phase hoists are
convertible from 460 volts to 230 volts. See the Wiring section
(paragraph 7-1) for voltage conversion instructions.
c. National Electrical Code (ASME C2) and local electrical codes
should be consulted and proper disconnects, branch circuit
protectors, and wiring provided.
d. Power cables furnished with the hoist have a green colored
ground wire which must be securely connected to the electrical
system ground.
e. When installing a three-phase hoist, make only temporary
connections at the power line. Push the “’UP” button and observe
the direction of the hook. If it raises, the phasing is correct and
permanent connections may be made at the power line. If the load
block lowers when the “UP” button is pushed, release the button
immediately since the limit switches will not operate to protect
the hoist from overtravel. Reverse the red and black wires at the
power line connection to correct the hook direction.
Do not change connections in the hoist or the pushbutton assembly.
2-4. VENT PLUG
This hoist is shipped with a factory installed pressure relief fitting. This
fitting needs no adjustments or maintenance before operating the hoist.
2-5. CHAIN LUBRICATION
The hoist chain should be liberally oiled before placing the hoist into
operation. For lubrication instructions, see paragraph 5-6.a.
2-6. TESTING
a. Before placing the hoist into operation, check for proper limit
switch operation. Push the ‘”UP” button and verify that the
hook block stops at least 2 inches from the bottom of the hoist.
Run the hoist down to its lower limit. At least 12 links of chain
should remain on the slack end. If either switch is not correct.
adjust according to the procedure outlined in paragraph 5-2.
NOTE: The upper and lower limit switches are factory set
to provide the maximum allowable hook travel. This travel
adjustment should not be increased. However, the switches
may be adjusted to stop the hook sooner at either end of
its travel.
b. Attach a light load to the hook and check the hoist for proper
operation. The load should stop without noticeable drift when
the pushbutton is released. Increase the load to near rated
load. The hoist should still lift the load without hesitation and
stop with no more than one-inch drift.
2-7. TROLLEY INSTALLATION
Coffing
®
CT Series trolleys can be mounted on American Standard
I Beams from 6 to 18 inches high (8-inch minimum on 4- or 5-ton
models). Adjustment for different beam dimensions is accomplished
with the proper placement of spacer washers as described below in
paragraph 2-7.a.
a. “I” Beam Adjustment. Adjustment for “I” beam sizes and
tolerances is accomplished by locating the spacer washers as
shown in Figure 2-1. Normal placement of washers is given in
Table 2-2. Refer to Table 2-1 for identification of part names and
numbers.
BEAM MANUFACTURING TOLERANCES ALLOW WIDE
VARIATIONS FROM HANDBOOK FLANGE WIDTHS, AND SLIGHT
CHANGES TO RECOMMENDED WASHER DISTRIBUTION MAY
BE NECESSARY TO SUIT SPECIFIC INSTALLATIONS.
The particular beam on which your hoist is to be installed should
be measured and trolley spacer washers adjusted as required to
achieve a clearance of 3/32” to 1/8”.
b. Periodic Inspection. The trolley should be inspected periodically
for evidence of excess wear or overload. Parts should be
replaced as required.
c. Lubrication. Trolley wheels are equipped with sealed, lifetime
lubricated, precision ball bearings which should not require
lubrication for the normal service of the trolley.