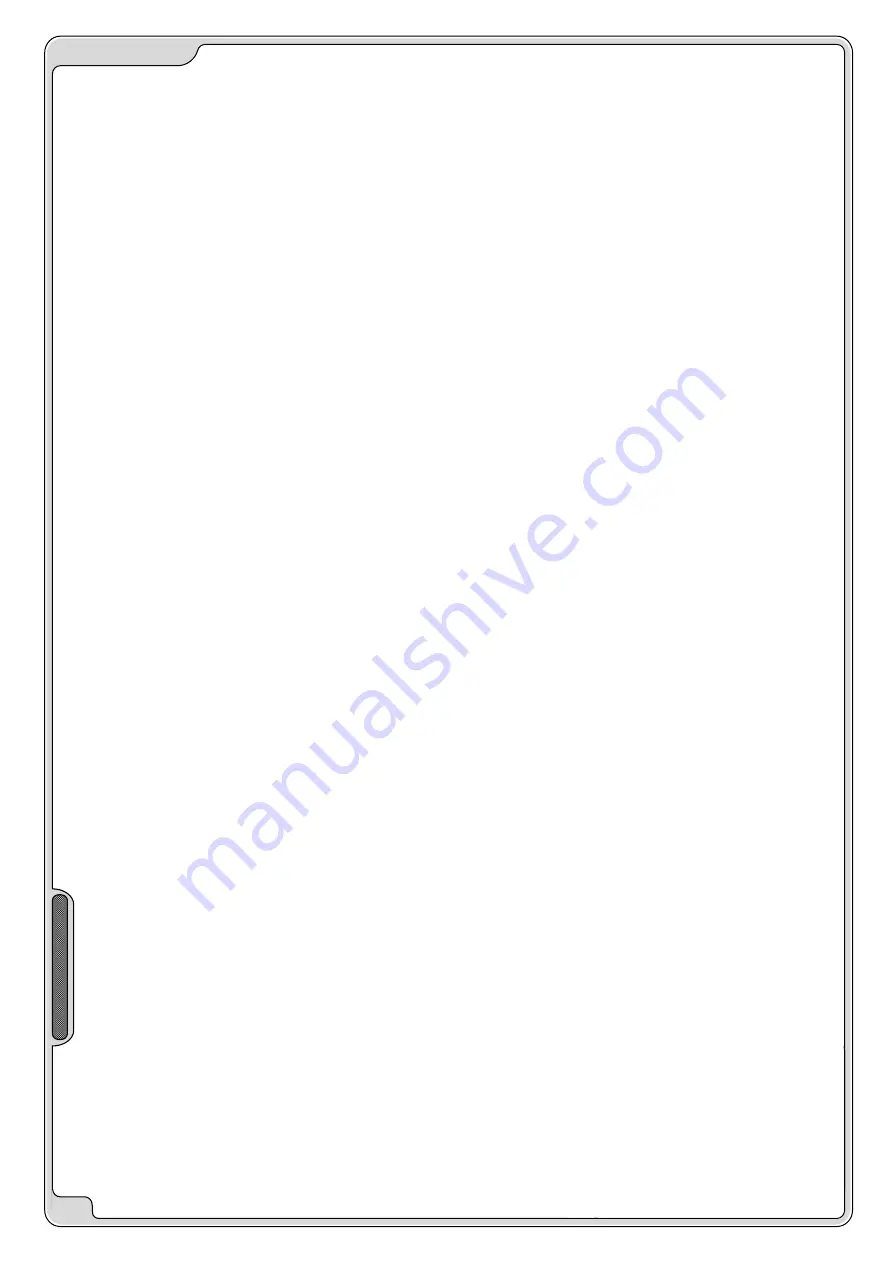
M02
J40
M6-
04
WDAT-3
2.160-3.660
- T R O U B L E S H O O T I N G -
58
- T R O U B L E S H O O T I N G -
THE OPERATIONS MUST BE CARRIED OUT BY TECHNICAL QUALIFIED PERSONNEL HAVING THE
REQUISITES UNDER LAW REQUISITES AND IN CONFORMITY WITH THE SAFETY REGULATIONS IN FORCE.
THE INTERVENTIONS WITHIN THE WARRANTY PERIOD WILL BE CARRIED OUT BY AUTHORIZED SERVICE
CENTERS.
BEFORE RESETTING AN ALARM, IDENTIFY AND ELIMINATE ITS CAUSE.
REPEATED RESETS MAY CAUSE SERIOUS DAMAGES.
Below is a list of the possible causes of alarms.
PROBE BROKEN
1. Identify the part on the wiring diagram.
2. Are the electric contacts/terminals loose? Are the leads broken or damaged?
3. Check the correct probe ohmic level using a tester.
4. Change the probe.
5. Check the electronic module configuration (only an authorised service centre can do this)
6. Change the electronic module
PRESSURE TRANSDUCER BROKEN
1. Identify the part on the wiring diagram
2. Are the electric contacts/terminals loose? Are the leads broken or damaged?
3. Check the pressure test points are in working order
4. Change the part
5. Check the electronic module configuration (only an authorised service centre can do this)
6. Change the electronic module
IN CERTAIN MACHINE CONFIGURATIONS, CERTAIN SAFETY DEVICES MAY BE IN SERIES AND REPORT TO A
SINGLE INPUT ON THE ELECTRONIC MODULE.
CHECK THE WIRING DIAGRAM TO SEE IF THE DEVICE RELATIVE TO THE ALARM IS CONNECTED IN SERIES
TO OTHER DEVICES OR SAFETY DEVICES.
HUGH PRESSURE
1. Is water temperature within the operating limits? (See paragraph: GENERAL - limits)
2. Is air temperature within the operating limits? (See paragraph: GENERAL - limits)
3. Is the coil clean?
4. Do the fans work?
5. Manostat/transducer: are the electric contacts/terminals loose? Are the wires broken or damaged?
6. Anti-condensation gas in the cooling circuit?
7. Too much refrigerant in the circuit?
8. Check the trigger point for the manostat and transducer.
9. Check the manostat or transducer pressure control point (deposits of oil, dirt, pin blocked mechanically)
LOW PRESSURE
1. Is air temperature within the operating limits? (See paragraph: GENERAL - limits)
2. Is water temperature within the operating limits? (See paragraph: GENERAL - limits)
3. Check the water flow to the exchanger (and the thermal jump between intake and outlet)
4. Is flow CONSTANT or does it change in certain situations? (For example, if the pumps are turned off, certain areas
of the plant are excluded or included, other uses are isolated, etc.).
5. Water filter clean / valves open /air bubbles in the plant?
6. Check the exchanger is clean
7. Manostat/transducer: are the electric contacts/terminals loose? Are the wires broken or damaged?
8. Is the cooling circuit pressurised? Are there visible leaks of coolant? Is it correctly filled?
9. Blocked
dehydrator
filter?
10. The expansion valve works correctly?
11. Check the trigger point for the manostat and transducer.
12. Check the manostat or transducer pressure control point (deposits of oil, dirt, pin blocked mechanically)
COMPRESSOR PROTECTION
1. Identify the part on the wiring diagram
2. Are the electric contacts/terminals loose? Are the leads broken or damaged?
3. Check electric coil continuity using a tester.
4. Is vacuum power voltage below the limits?
5. Check the power contactors and relative contacts.
6. Is start-up power voltage lower than the limits?
7. Check electric input
8. Compressor discharge temperature higher than 120°C? Yes > check the thermostat and the coolant level.
FAN PROTECTION
1. Identify the part on the wiring diagram
2. s the fan blocked manually? Check the bearings and drive belt (if fitted)
3. Are the electric contacts/terminals loose? Are the leads broken or damaged?
4. Check electric coil continuity using a tester
5. Is vacuum power voltage below the limits?
6. Check electric input
Summary of Contents for WDAT-3 2.160
Page 2: ......