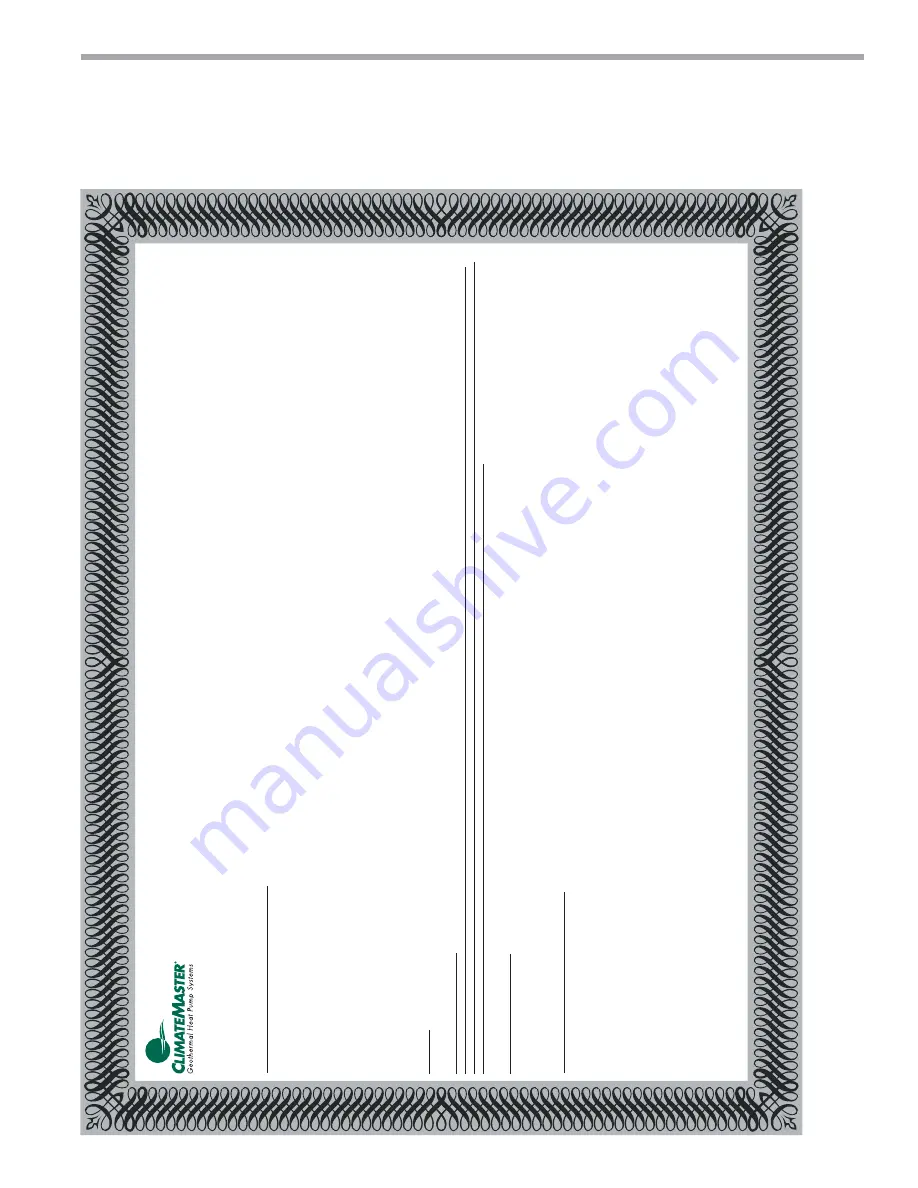
T H E S M A R T S O L U T I O N F O R E N E R G Y E F F I C I E N C Y
Vertical Stack
R e v. : 0 4 / 2 4 / 2 0 1 9
67
c l i m a t e m a s t e r. c o m
Warranty
CLIMA
TE MASTER, INC.
LIMITED EXPRESS
W
ARRANTY/ LIMIT
A
TION OF
REMEDIES
AND LIABILITY
It is expressly understood that unless a statement is speci
À
cally
identi
À
ed as a warranty
, statements made by Climate Master
, Inc., a Delaware corporation, (“CM”) or its representatives, relating to
CM’
s products, whether oral,
written or contained in any sales literature, catalog or any other agreement, are not express warranties and do not form a part
of the basis of the bar
g
ain, but are merely CM’
s opinion or commendation of CM’
s products.
EXCEPT
AS SPECIFICALL
Y
SET
FOR
TH HEREIN,
THERE IS NO EXPRESS
W
ARRANTY
AS
T
O
ANY
OF
CM’S PRODUCTS. CM MAKES NO
W
ARRANTY
AGAINST
LA
TENT
DEFECTS. CM MAKES
NO
W
ARRANTY
OF
MERCHANT
ABILITY
OF
THE GOODS OR OF
THE FITNESS OF
THE GOODS FOR
ANY
P
A
R
T
ICULAR PURPOSE.
GRANT
OF
LIMITED EXPRESS
W
ARRANTY
CM warrants CM products purchased and retained in the United States of
America and Canada to be free from defects in material a
nd workmanship under normal use and maintenance as follows: (1)
All complete air condition-
ing, heating and/or heat pump units built or sold by CM for twelve (12) months from date of unit start up or eighteen (18) mont
hs from date of shipment (from factory), whichever comes
À
rst; (2) Repair and replacement parts,
which are not supplied under warranty
, for nintey (90) days from date of shipment (from factory).
All parts must be returned t
o CM’
s factory in Oklahoma City
, Oklahoma, freight prepaid, no later than sixty (60) days after
the date of the failure of the part; if CM determines the part to be defective and within CM’
s Limited Express
W
arranty
, CM sha
ll, when such part has been either replaced or repaired, return such to a factory recognized dealer
,
contractor or service or
ganization, F
.O.B. CM’
s factory
, Oklahoma City
, Oklahoma, freight prepaid.
The warranty on any parts re
paired or replaced under warranty expires at the end of the original warranty period.
This warranty does not cover and does not apply to: (1)
Air
À
lters, fuses, refrigerant,
Á
uids, oil; (2) Products relocated after initial installation; (3)
Any portion or component of any system that is not supplied
by CM, regardless
of the cause of the failure of such portion or component; (4) Products on which the unit identi
À
cation tags or labels have been removed or defaced; (5) Products on which payment to CM is or has been in default; (6) Product
s
which have defects or damage which result from improper installation, wiring, electrical imbalance characteristics or maintenan
ce; or are caused by accident, misuse or abuse,
À
re,
Á
ood, alteration or misapplication of the prod-
uct; (7) Products which have defects or damage which result from a contaminated or corrosive air or liquid supply
, operation at
abnormal temperatures, or unauthorized opening of refrigerant circuit; (8) Mold, fungus or bacteria
damages; (9) Products subjected to corrosion or abrasion; (10) Products manufactured or supplied by others; (1
1) Products which
have been subjected to misuse, negligence or accidents; (12) Products which have been operated
in a manner contrary to CM’
s printed instructions; or (13) Products which have defects, damage or insuf
À
cient performance as a result of insuf
À
cient or incorrect system design or the improper application of CM’
s products.
CM is not responsible for: (1)
The costs of any
Á
uids, refrigerant or other system components, or associated labor to repair or replace the same, which is incurred as a result
of a defective part covered by CM’
s Limited Express
W
arranty; (2)
The costs of labor
, refrigerant, materials or service incurred in removal of the defective part, or in obtaining
and replacing the new or repaired part; or
, (3)
T
ransportation costs of the defective part from the installa-
tion site to CM or of the return of any part not covered by CM’
s Limited Express
W
arranty
.
Limitation:
This Limited Express
W
arranty is given in lieu of all other warranties. If, notwithstanding the disclaimers contained herein,
it is determined that other warranties exist, any such warranties, including without limita-
tion any express warranties or any implied warranties of
À
tness for particular purpose and merchantability
, shall be limited to the duration of the Limited Express
W
arranty
.
LIMIT
A
TION OF
REMEDIES
In the event of a breach of the Limited Express
W
arranty
, CM will only be obligated at CM’
s option to repair the failed part or
unit or to furnish a new or rebuilt part or unit in exchange for the part or unit which has failed. If
after written notice to CM’
s factory in Oklahoma City
, Oklahoma of each defect, malfunction or other failure and a reasonable n
umber of attempts by CM to correct the defect, malfunction or other failure and the remedy fails
of its essential purpose, CM shall refund the purchase price paid to CM in exchange for the return of the sold good(s). Said re
fund shall be the maximum liability of CM.
THIS REMEDY
IS
THE SOLE
AND EXCLUSIVE
REMEDY
OF
THE BUYER OR
THEIR PURCHASER
AGAINST
CM FOR BREACH OF
CONTRACT
, FOR
THE BREACH OF
ANY
W
ARRANTY
OR FOR CM’S NEGLIGENCE
OR IN STRICT
LIABILITY
.
LIMIT
A
TION OF
LIABILITY
CM shall have no liability for any damages if CM’
s performance is delayed for any reason or is prevented to any extent by any e
vent such as, but not limited to: any war
, civil unrest, government restrictions or restraints, strikes
or work stoppages,
À
re,
Á
ood, accident, shortages of transportation, fuel, material, or labor
, acts of God or any other reason beyond the sole control
of CM.
CM EXPRESSL
Y
DISCLAIMS
AND EXCLUDES
ANY
LIABIL-
ITY
FOR CONSEQUENTIAL
OR INCIDENT
AL
DAMAGE IN CONTRACT
, FOR BREACH OF
ANY
EXPRESS OR IMPLIED
W
ARRANTY
, OR IN
T
O
R
T
,
WHETHER FOR
CM’
s NEGLIGENCE OR
AS
STRICT
LIABILITY
.
OBT
AINING W
ARRANTY
PERFORMANCE
Normally
, the contractor or service or
ganization who installed the products will provide warranty performance for the owner
. Sh
ould the installer be unavailable, contact any CM recognized dealer
, contractor or service or
ganiza-
tion. If assistance is required in obtaining warranty performance, write or call:
Climate Master
, Inc. • Customer Service • 7300 S.W
. 44th Street • Oklahoma City
, Oklahoma 73179 (405) 745-6000
NOTE: Some states or Canadian provinces do not allow limitations on how long an implied warranty lasts, or the limitation or ex
clusions of consequential or incidental damages, so the foregoing exclusions and limitations may
not apply to you.
This warranty gives you speci
À
c legal rights, and you may also have other rights which vary from state to state and from Canadian province to Canadian provi
nce.
Please refer to the CM Installation, Operation and Maintenance Manual for operating and maintenance instructions.
*LC083*
Rev
.: 1
1
/09
LC083