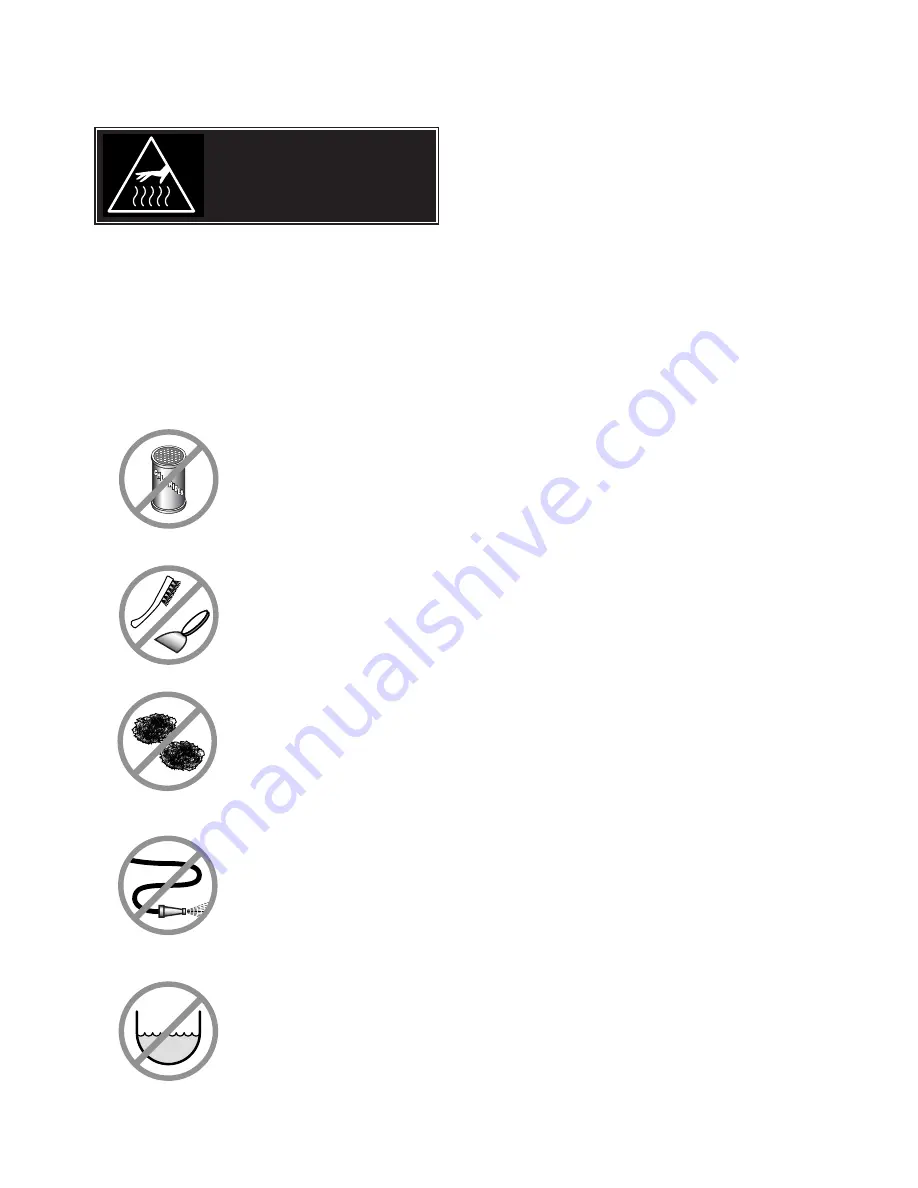
CARE AND CLEANING
Cooking equipment must be cleaned regularly to
maintain its fast, efficient cooking performance and
to ensure its continued safe, reliable operation. The
best time to clean is shortly after each use (allow
unit to cool to a safe temperature).
WARNINGS
➩
Do not use detergents or
cleansers that are chloride
based or contain quaternary
salt.
➩
Do not use a metal bristle
brush or scraper.
➩
Steel wool should never be
used for cleaning the stainless
steel.
➩
Unit should never be cleaned
with a high pressure spray
hose.
➩
Do not leave water sitting in unit
when not in use.
Stagnant
Water
High Pressure
Spray Hose
Chloride Cleaners
Steel Pads
Wire Brush &
CLEANING INSTRUCTIONS
CAUTION
SURFACES MAY
BE EXTREMELY HOT!
CLEANING INSTRUCTIONS
1.
Turn unit off.
2.
Remove drain screen (if applicable). Thoroughly
wash and rinse the screen either in a sink or a
dishwasher.
3.
Prepare a warm water and mild detergent solution in
the unit.
4.
Remove food soil using a nylon brush.
5.
Loosen food which is stuck by allowing it to soak at
a low temperature setting.
6.
Drain unit.
7.
Rinse interior thoroughly.
8.
If the unit is equipped with a Tangent Draw-Off
Valve, clean as follows:
a)
Disassemble the draw-off valve first by turning
the valve knob counter-clockwise, then turning
the large hex nut counter-clockwise until the
valve stem is free of the valve body.
b)
In a sink, wash and rinse the inside of the valve
body using a nylon brush.
c)
Use a nylon brush to clean tangent draw-off tube.
d)
Rinse with fresh water.
e)
Reassemble the draw-off valve by reversing the
procedure for disassembly. The valve's hex nut
should be hand tight only.
9.
If the unit is equipped with a Butterfly Valve, clean
as follows:
a)
Place valve in open position.
b)
Wash using a warm water and mild detergent
solution.
c)
Remove food deposits using a nylon brush.
d)
Rinse with fresh water.
e)
Leave valve open when unit is not in use.
10.
Using mild soapy water and a damp sponge, wash
the exterior, rinse, and dry.
NOTES
➩
For more difficult cleaning applications one of the
following can be used: alcohol, baking soda, vinegar,
or a solution of ammonia in water.
➩
Leave the cover off when the kettle is not in use.
➩
For more detailed instructions refer to the Nafem
Stainless Steel Equipment Care and Cleaning manual
(supplied with unit).
Summary of Contents for MKEL-100-T
Page 24: ...POWER TILT 10 CONSOLE 44 45 43...