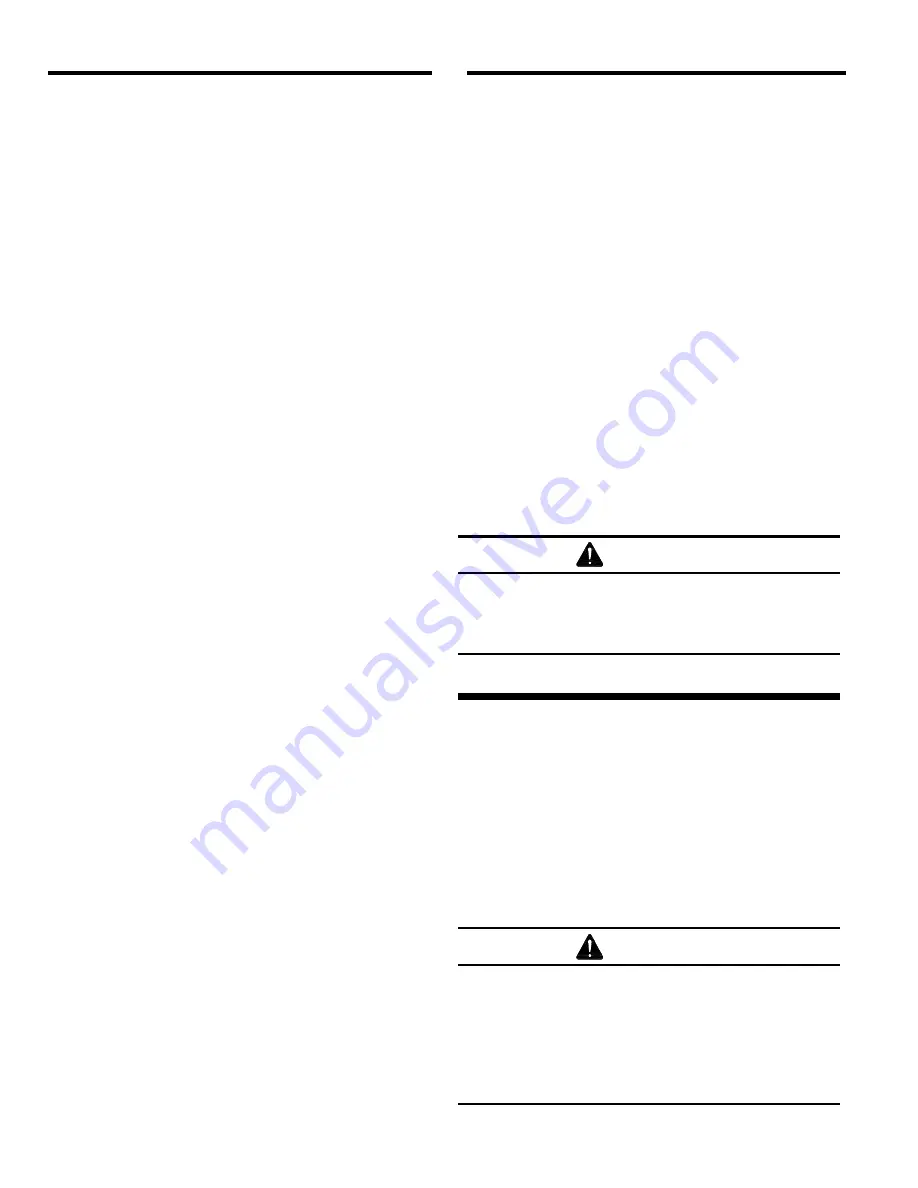
PULSAR
®
3D SUCTION BLAST CABINET
Page 4
© 2020 CLEMCO INDUSTRIES CORP.
www.clemcoindustries.com
Manual No. 29374
1.7
Nozzle Options
1.7.1
Ventilation requirements limit standard cabinets
to No. 5 (5/16" orifice) nozzle and No. 5 (5/32" orifice) air
jet. Unless otherwise specified at the time of order,
cabinets are supplied with a tungsten carbide lined
nozzle. Ceramic nozzles are available but should be
limited to occasional blasting and with mild media. More
durable boron carbide nozzles should be used when
blasting with aggressive media such as those listed in
Section 1.8.4. Nozzle options are shown under BNP
®
Gun
and Hose Assembly in Section 8.2.
1.8
Media
1.8.1
The Pulsar
®
3D utilizes most common reusable
media 60 mesh to 180 mesh that is specifically
manufactured for dry blasting. Media finer than those
recommended may carry over to the dust collector. Media
coarser than those recommended may not convey
through the media hose or recovery hose.
1.8.2
Steel:
Steel grit 50 mesh to 120 grit or S70 to
S170 shot may be used.
1.8.3
Sand and slag media:
These are not suitable for
cabinet use. Sand should NEVER be used for abrasive
blasting because of the respiratory hazards associated with
media containing free silica. Slags are not recommended
because they rapidly break down and are not recyclable.
1.8.4
Aluminum Oxide, Silicon Carbide, and
Garnet:
These are the most aggressive of the commonly
used media. Aggressive media such as these between 60
mesh and 180 mesh may be used, but the service life of
any components exposed to the media will be reduced.
To avoid unscheduled downtime and maximize cabinet
life, periodically inspect all parts of the cabinet, nozzle,
and hoses, that come in contact with the media.
When using aggressive media use a boron carbide lined
nozzle. Nozzles lined with boron carbide extend nozzle
wear life. Refer to Section 8.2 Item 9.
1.8.5
Glass Bead Recommended range is #6 thru
#13:
Most beads are treated to ensure free-flow operation
even under moderately high humidity conditions. Glass
beads subjected to excessive moisture may be reused
after thorough drying and breaking up of any clumps.
1.8.6
Fine-Mesh Media:
In most cases media finer
than 180 will carry over to the dust collector.
1.8.7
Lightweight
Media:
Plastic
and
similar
lightweight and/or nonaggressive media are generally not
recommended for suction-style cabinets because the
lower blast velocity of suction blasting combined with the
softer and lighter weight media do not provide the media
impact for productive blasting.
1.9
Compressed-Air Requirements
1.9.1
The cabinet requires approximately 33 cfm of
compressed air at a maximum of 80 psi.
1.9.2
The filter at the air inlet connection reduces
condensed water from the compressed air. Its use is
especially important in areas of high humidity, or when
fine-mesh media are used. Moisture causes media to
clot and inhibits free flow through the feed assembly. If
the filter does not remove enough moisture to keep
media dry and flowing, it may be necessary to install an
air dryer or aftercooler in the air-supply line.
1.10
Electrical Requirements
1.10.1
The system requires 115 VAC, 1 PH, 60 Hz, with
15 amps service. A 7-foot power cord is supplied. No
additional wiring is required.
Do not use electrical adaptors that eliminate the
ground prong on 115-volt plugs. Doing so can
cause injury from electric shock and damage
equipment.
2.0
INSTALLATION
2.1
General Installation Notes
2.1.1
Place the cabinet in a convenient location where
compressed air and electrical service are available. Allow
full access to the doors and service areas.
2.2
Connect Compressed Air-Supply Line
Failure to observe the following before
connecting the equipment to the compressed-
air source can cause serious injury from the
sudden release of trapped compressed air:
Lockout and tagout the compressed-air
supply.
Bleed the compressed-air supply line.