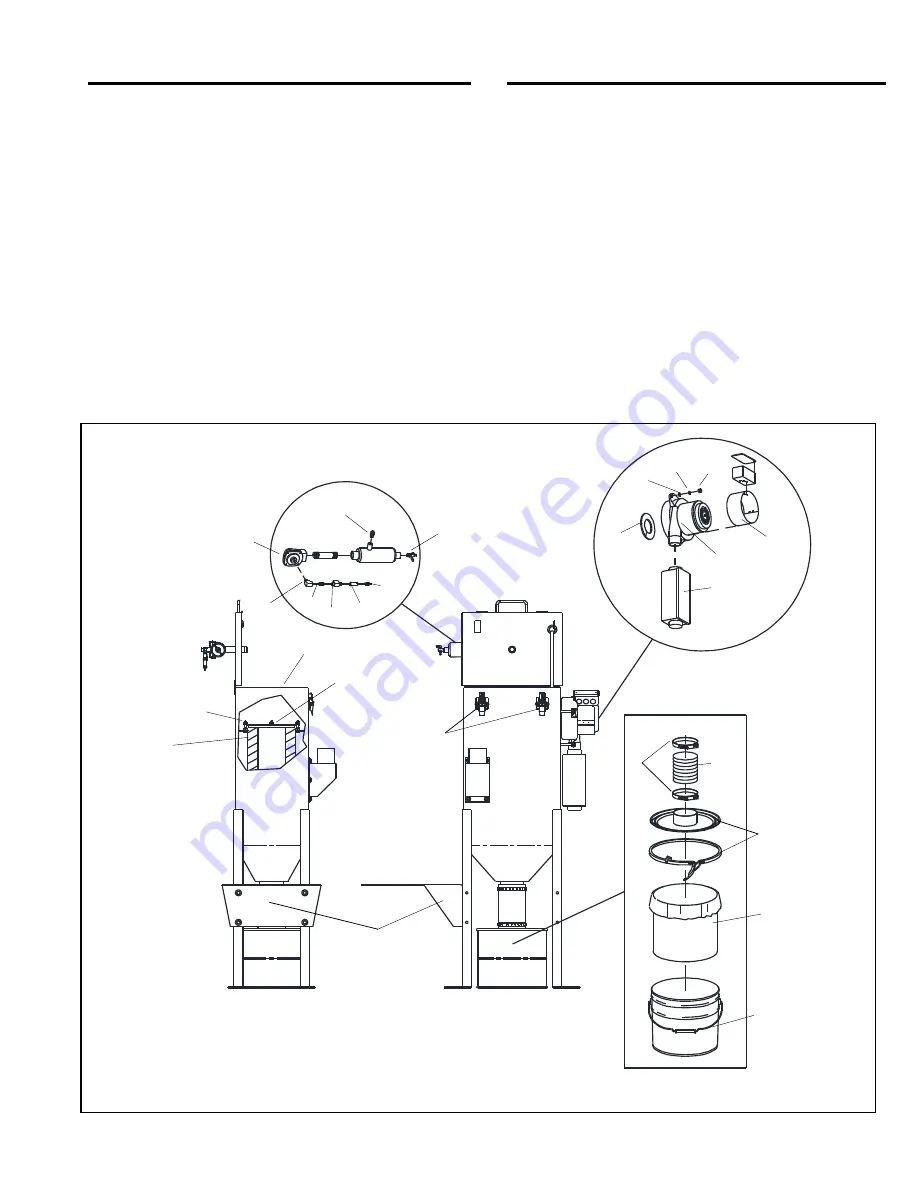
PULSAR
®
3D SUCTION BLAST CABINET
Page 27
© 2020 CLEMCO INDUSTRIES CORP.
www.clemcoindustries.com
Manual No. 29374
8.9
Dust Collector Assembly ‒ Figure 30
Item Description
Stock No.
1. Filter cartridge 8" x 16" flanged .................... 29903
2.
Hex nut, 3/8” – 16 ......................................... 03318
3. Filter cartridge hold down plate .................... 29901
4. Band, blower motor ...................................... 16409
5. Gasket, 3/
16” x 1”, 2 ft. required ................... 00186
6. Blower/motor assembly ................................ 24975
7. Brushes, blower motor, not shown .............. 28157
8. Muffler, blower .............................................. 24976
9. Latch, door .................................................... 10290
10. Valve, 3/4" NPT diaphragm pulse ................ 25867
11. Elbow, 1/8" NPT brass st ............................. 03993
12. Nipple, 1/8" brass hex .................................. 01945
13. Valve, 3 way ................................................. 12202
14. Actuator, air pilot .......................................... 19123
15. Fitting, straight 1/8" NPT x 1/8" barb ........... 11732
16. Petcock, drain .............................................. 01993
17. Fitting, straight 1/4" NPT x 3/8" tube ............ 11736
18. Clamp, 4" ..................................................... 11577
19. Hose, 4" unlined flex, 1-ft minimum ............. 12447
20. Lid and locking ring, dust drum .................... 23419
21. Liners, drum, pack of 5 ................................ 28621
22. Dust drum, 3.5 gallon ................................... 23417
23. Washer, 5/16" flat ........................................ 03216
24. Washer, 5/16" lock ....................................... 03217
25. Nut, 5/16" NC hex ........................................ 03211
26.
Gasket, 5/16” x 1”, 5 ft. required ................... 00187
27. Reclaim mount .............................................. 29902
Some items removed or rotated for clarity.
Figure 30
2
21
19
20
15
8
22
11
23
25
26
16
5
6, 7
17
10
9
12
13
3
4
24
1
14
18
27