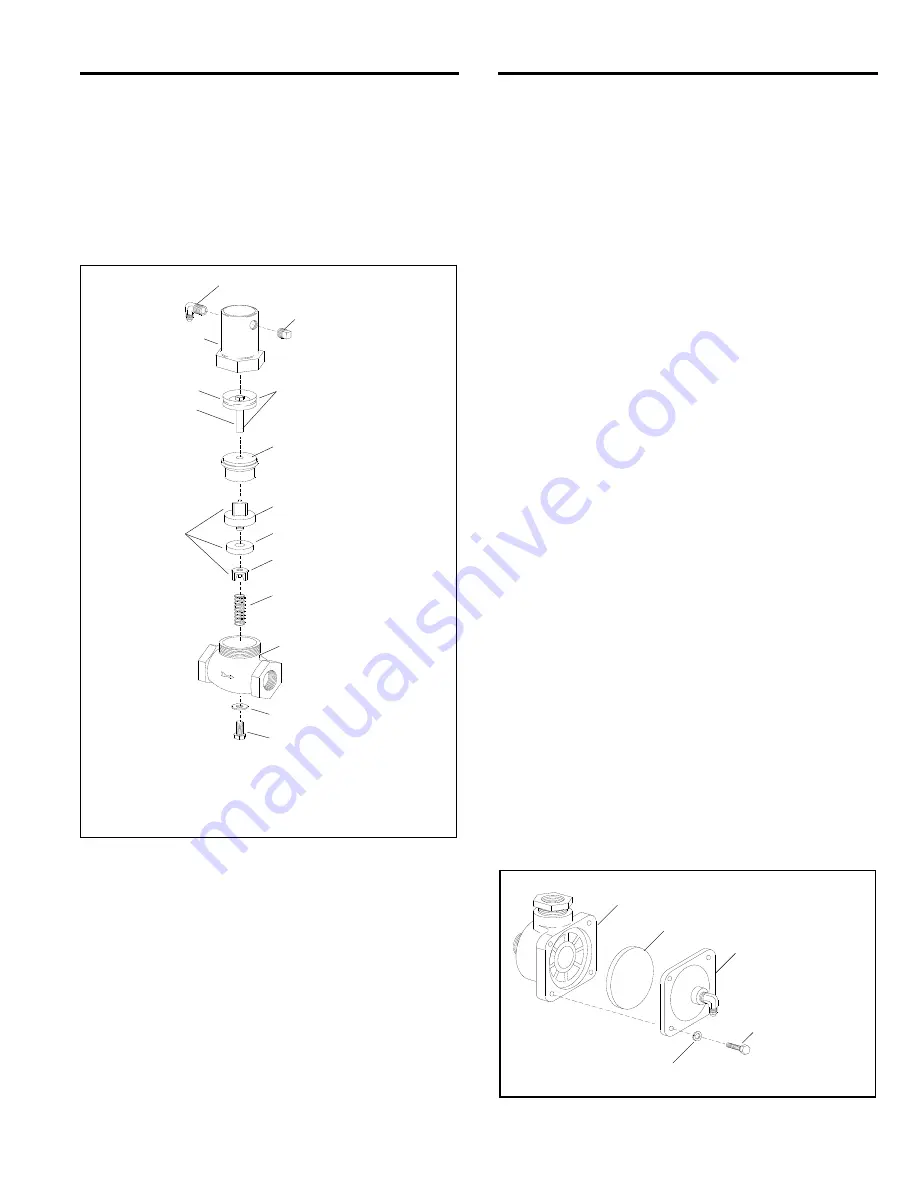
CLASSIC BLAST MACHINE with TLR-100/300 REMOTE CONTROLS
Page 21
© 2018 CLEMCO INDUSTRIES CORP.
www.clemcoindustries.com
Manual No. 22501, Rev. I 02/18
6.4.4
To remove the bonnet, lift it straight up until the
piston rod clears the spindle guide.
6.4.5
Remove the spindle, plug assembly, and spring
from the valve body.
6.4.6
Remove the piston from the bonnet by pulling
the piston rod.
Figure
19
6.4.7
Inspect all parts for wear and damage as
follows:
Inspect the valve-plug washer, valve plug, and plug
retainer for damage. Replace all damaged parts.
When reassembling the valve-plug assembly tighten
the retainer enough to compress the washer, but not
so tight that it causes it to bulge.
Examine the body casting for wear. If the body or the
machined seat is worn, replace the body.
Examine the spring guide bolt and nylon washer. If
either is worn, replace both.
The spring is approximately 1-5/8
long; if it is
abrasive worn, rusty, or compressed, replace it.
The piston cup should fit snugly against the bonnet’s
cylinder wall. If it does not, replace the piston
assembly.
The piston rod should be free of deep abrasion and
move freely in the spindle guide’s bore. If it is badly
abraded, drags in the bore, or is loose in the bore,
replace the piston assembly.
6.4.8
Lubricate the cylinder wall and piston cup with
lightweight machine oil or tool oil.
6.4.9
Install the piston into the bonnet’s cylinder.
Cocking the piston so it enters the bonnet at a slight
angle and rotating it while applying pressure makes
assembly easier. Do not push the piston fully into the
bonnet; the rod should be flush with the opening.
6.4.10
Place the spring over the guide bolt and place
the plug assembly (retainer down) on the spring.
6.4.11
Place the spindle in the body. The large opening
faces down and fits over the plug fins. The spindle
shoulder will not rest on the valve body due to the force
of the spring.
6.4.12
To assemble the bonnet to the valve body, first
insert the piston rod into the spindle guide hole. While
keeping the bonnet, spindle, and body aligned, screw the
bonnet onto the body. If all parts are correctly aligned, the
body will screw on hand-tight until it is seated.
NOTE: If
the bonnet does not screw on hand-tight, do not
force it. Recheck alignment and repeat assembly.
6.4.13
After the bonnet is fully seated on the body,
tighten the assembly with a wrench.
6.4.14
Attach the control hose to the fitting on the
bonnet.
6.5
Diaphragm Outlet Valve - Figure 20
Refer to Section 6.4 to service the piston outlet valve.
Figure
20
*Items included in service kit.
For replacement parts, refer to Section 8.11.
Valve Body
Diaphragm
Cap
Cap Screw
Lock Washer
1/4-NPT Plug
Elbow Adaptor
Valve Bonnet
Plug and Spindle Guide
Piston Assembly
Piston Cup
*Valve Plug
Piston Rod
*Valve Plug
*Valve-Plug Retainer
*Spring
Valve Body
*Nylon Washer
*Cap Screw (Guide Bolt)
Plug
Assembly