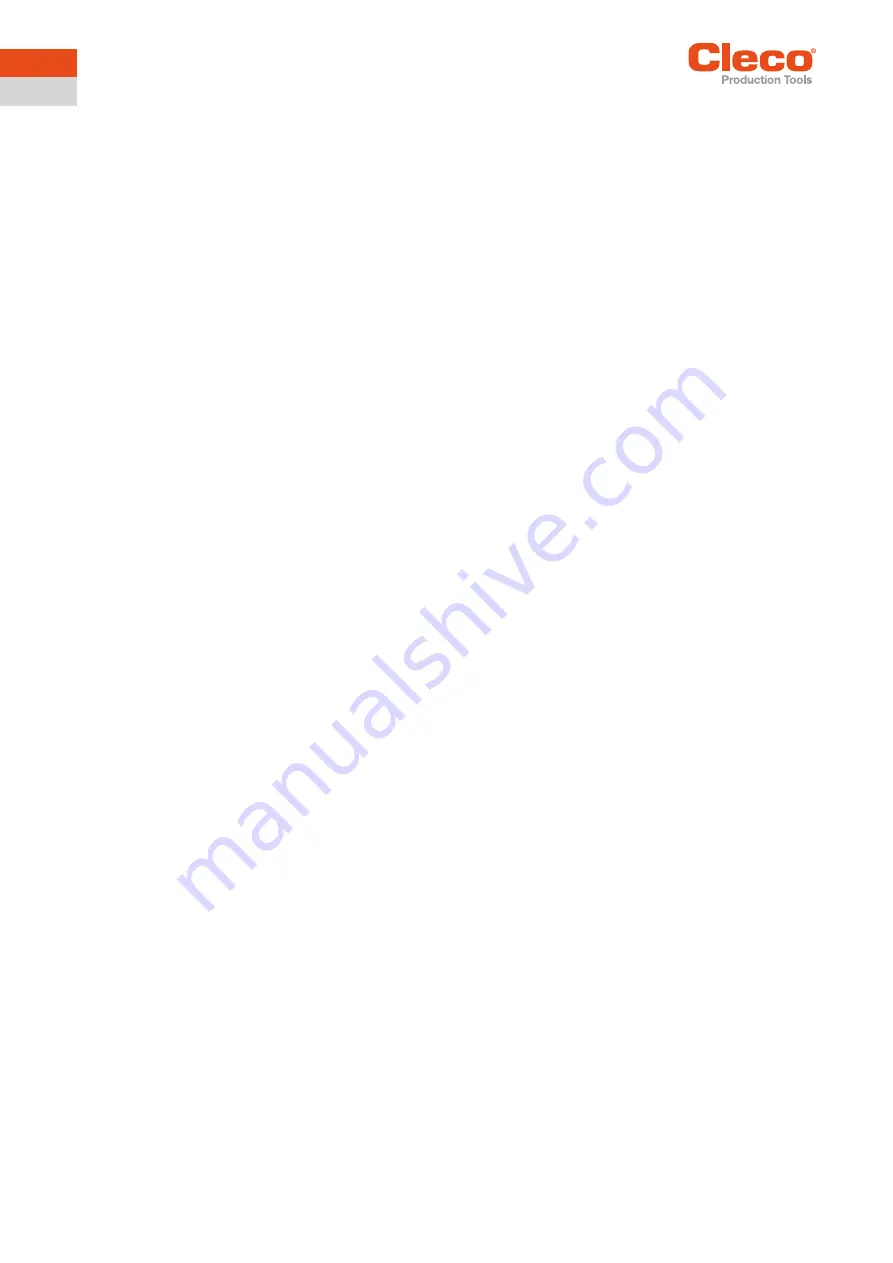
8
TM12-1109 | 2019-02
Apex Tool Group
1
EN
Use a suitable hoist.
Ensure the controller is rigidly mounted and secured
(see Quick Installation Guide).
Organize cables and lines to avoid damage and trip-
ping hazards.
Observe the permitted cable bending radius.
Do not exceed total length of Tool Cable
In the event of a fault, high leakage currents can occur and
cause injuries by electric shock.
Use the included power cable. When replacing, use an
appropriate power cable.
For 115 VAC cables with a larger cross-section, use
Order No. 541683-01.
Prior To Initial Operation
Only operate on a grounded power supply (TN sys-
tem). Operation on the IT system is not permitted.
Ensure a standard-compliant PE connection.
Prior to initial operation, carry out the protective con-
ductor measurement in accordance with the local reg-
ulations (in Germany, DGUV Regulation 3).
Do not switch on the controller until all the connections
have been made correctly (see hardware description).
Danger Due To Dangerous Movements
Insufficient emergency stop facilities can have life-threat-
ening consequences.
The necessity of an emergency stop and its execution
is the responsibility of the user and his risk analysis!
Provide accessible and effective emergency stop facil-
ities. Unlocking the emergency stop device must not
cause an uncontrolled restart of the system!
Before switching on the system, check the emergency
stop devices for function.
Danger Due To Incorrect Torque Measurement
An undetected NOK tightening could have life-threatening
consequences.
Recalibration (or capability analysis) is essential fol-
lowing incorrect use (crash, mechanical overload…).
For Category A Tightenings (VDI 2862) which are criti-
cal for safety, activate a redundancy measurement
(e.g., current redundancy).
Introduce regular monitoring of measuring equipment
for associated manufacturing equipment.
Only work with a properly functioning tightening sys-
tem. If in doubt, contact
Sales & Service Center
.
During Operation
Immediately power off the controller in the case of
unusual noise, heating, or vibration from the tool.
Pull power plug and have the tightening system
checked, and repaired if necessary, by qualified per-
sonnel.
Never remove the power plug from the outlet by pulling
the cord.
Protect cables from heat, oil, sharp edges or moving
parts.
Replace damaged cables immediately.
Ensure tool and plug connections between the
controller and tool are clean.
Ensure the workstation remains uncluttered to avoid
injury or damage to the tightening components.
Ensure the workstation provides adequate space for
the operation being completed.
Use of Secondary controllers in Line Topology:
When shutting off or in case of Secondary controller failure,
the TSNet bus communication is interrupted. This commu-
nication loss to the Primary / Master controller has conse-
quences for the Secondary controllers:
→ No results are returned to the Primary / Master
controller.
→ No more rundowns are started.
→ An in-process rundown is reported with the error
message SA (abort by removing the start signal) if
the TSNet connection was interrupted during tight-
ening.
→ A shut-off signal is no longer received and so a
shut-off is only possible
-
via the start button of the tool
-
after reaching the shut-off criterion
-
via a safety shut-off after two seconds
WARNING!
During remote-start operation (multiple tool setup) an inter-
ruption of TSNet bus leads to a delayed stop of the spindle/
tool. This delay is 2 seconds.
Danger Due To Unexpected Start Of The Motor Or An
Expected But Missing Stop
Despite redundant controller parts and monitoring func-
tions, an unexpected start of the machine can occur in very
rare cases. Possible reasons may include, but are not lim-
ited to: Remote control of diagnostic functions, bit dump in
the memory of the controller.
Mechanical hazards such as jars/jolts due to counter
torques; risk of injury due to winding up and seizing can
result from the tool.
•
Primary controller
mPro400GCD-P(…) max. 45 m
•
Secondary controller
mPro-400GCD-S(…) max. 30 m
•
When using tool Series 70:
-
Up to 3 m Tool Cable can be used with a
maximum of 25 m Extenstion Cable.
-
Up to 6 m Tool Cable can be used with a
maximum of 20 m Extenstion Cable.
-
Tool cables over 6 m must not be extended.
Summary of Contents for NeoTek 30 Series
Page 26: ...Leistungsdaten 26 TM12 1109 LG1 2019 02 Apex Tool Group 2 DE...
Page 38: ...Datos de rendimiento 38 TM12 1109 LG1 2019 02 Apex Tool Group 3 ES...
Page 50: ...Caract ristiques techniques 50 TM12 1109 LG1 2019 02 Apex Tool Group 4 FR...
Page 62: ...Prestazioni 62 TM12 1109 2019 02 Apex Tool Group 5 IT...
Page 75: ......