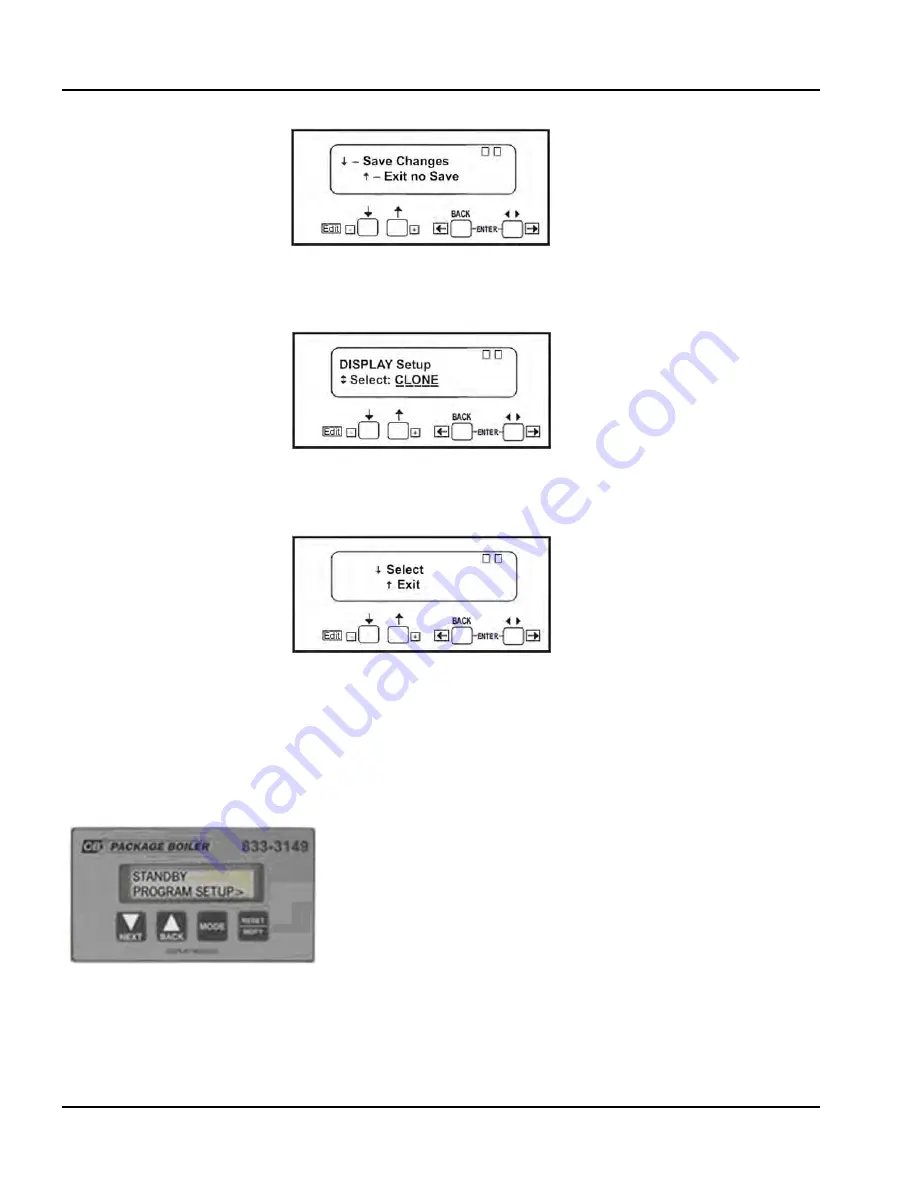
Section 3 — Hardware Checkout
Hawk 1000
3-6
Part No. 750-366
Press down arrow key to save changes.
Press ENTER buttons at the same time.
Press upper arrow key to exit.
3.1.5 Burner Control Modbus Address and Baud Rate - CB120E
The CB120E has built-in Modbus capability; for proper communications the ModBus baud rate and node
address need to be correctly set. To check the settings, the CB120E must be powered.
Press the <BACK> or <NEXT> key on the CB120E display until the screen displays PROGRAM SETUP>.
Summary of Contents for Hawk 1000
Page 1: ...750 366 07 2013 Hawk 1000 Boiler Control Operation Manual...
Page 4: ......
Page 6: ......
Page 30: ...Section 3 Hardware Checkout Hawk 1000 3 12 Part No 750 366...
Page 54: ...Section 4 System Configuration Hawk 1000 4 24 Part No 750 366...
Page 78: ...Section 6 Diagnostics and Troubleshooting Hawk 1000 6 6 Part No 750 366...
Page 82: ...Section 7 Parts Hawk 1000 7 4 Part No 750 366...