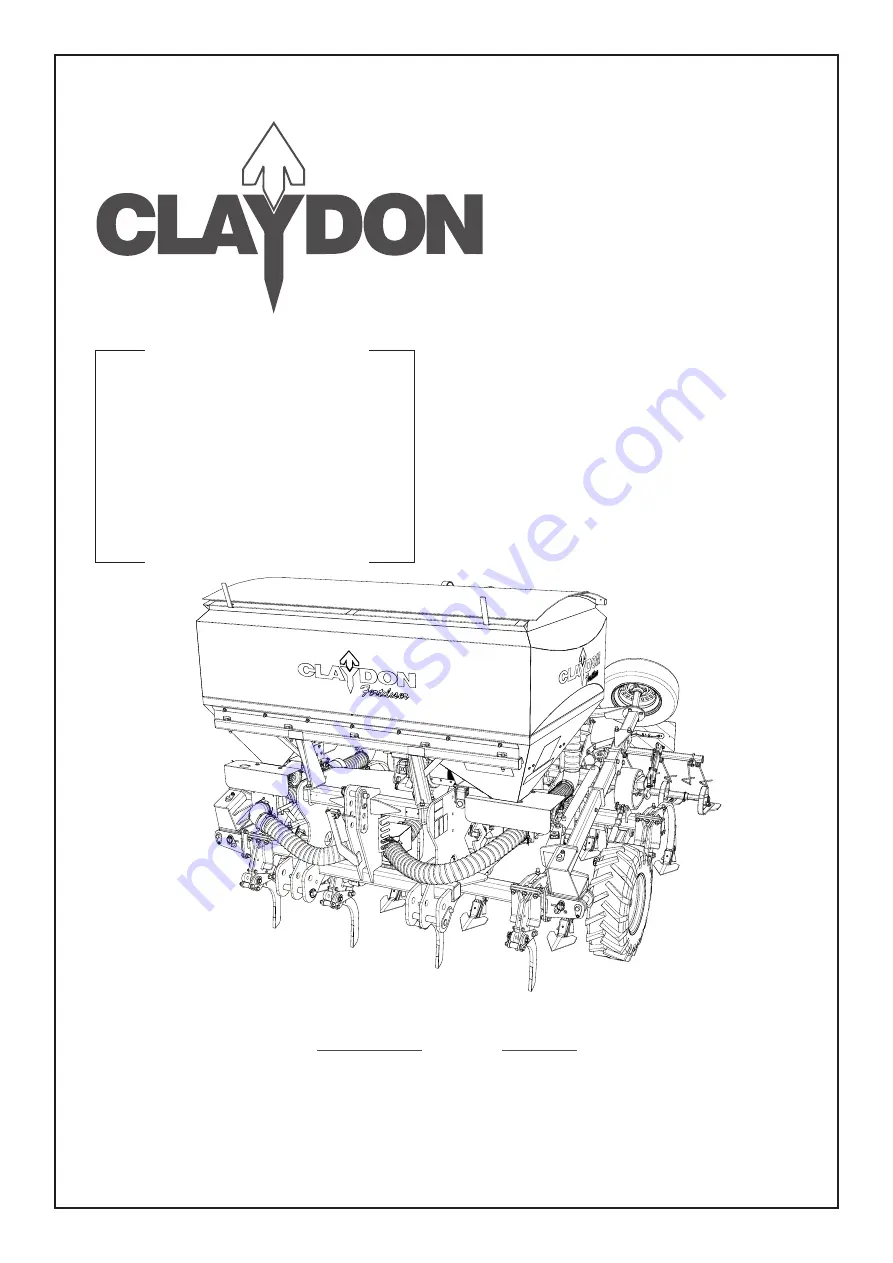
OPERATORS MANUAL
CLAYDON YIELD-O-METER LTD
BUNTERS ROAD, WICKHAMBROOK, NEWMARKET, SUFFOLK, CB8 8XY
TEL: +44 (0)1440 820 327
EMAIL: [email protected]
www.claydondrill.com
HYBRID
M3F &
M4RF
DOC0017
REV-01
Authorised Representative
Summary of Contents for HYBRID M3F
Page 4: ......
Page 6: ......
Page 8: ......
Page 14: ...E SAFETY 14 OPERATORS MANUAL HYBRID M3F M4RF Decal Location DC0091 ...
Page 41: ...41 H IN FIELD OPERATION OPERATORS MANUAL HYBRID M3F M4RF Seed Rate Calibration Chart M3F ...
Page 42: ...H IN FIELD OPERATION 42 OPERATORS MANUAL HYBRID M3F M4RF Seed Rate Calibration Chart M4RF ...
Page 59: ...59 I CARE AND MAINTENANCE OPERATORS MANUAL HYBRID M3F M4RF PAGE LEFT BLANK ...