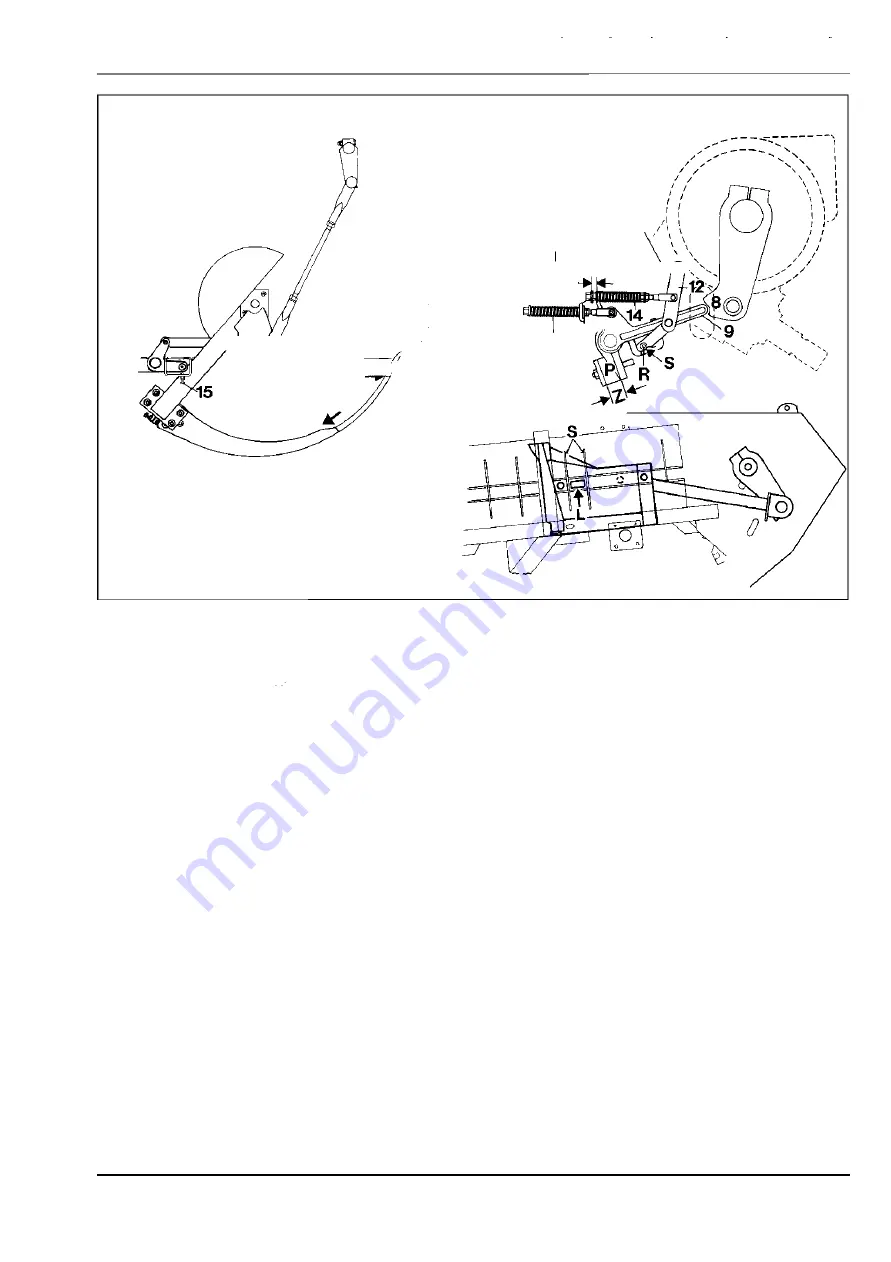
Basic settings for the twine wrap device
G
13
i
-t:::::===============ii:1§:�1
I
B
I
�=cc======::::i===-
J
M"LlP
-.....;_11
200741
Ram stop
The ram stop is built on next to the main gearbox.
It protects the needles against damage, should these
come to a stop in the bale chamber. If this event
occurs, the shear bolt on the main gearbox shears
off.
Setting the ram stop:
PLEASE NOTE!
The rubber pressure springs (P)
must be set to the dimension (Z) 5 6 ± 1 mm.
1 . Release the tying cycle and turn the flywheel
by hand
in the direction of the arrow until the
needles are in the bale chamber.
2. Turn the flywheel against the direction of the
machine until the crank arms (8) have just passed
the ram stops ( 9). The ram stops give way
against the pressure of the crank arms.
(Fig. 18)
QUADRANT 2 2 00 / 2 2 00 RC
10
1 8
1.7 / 9