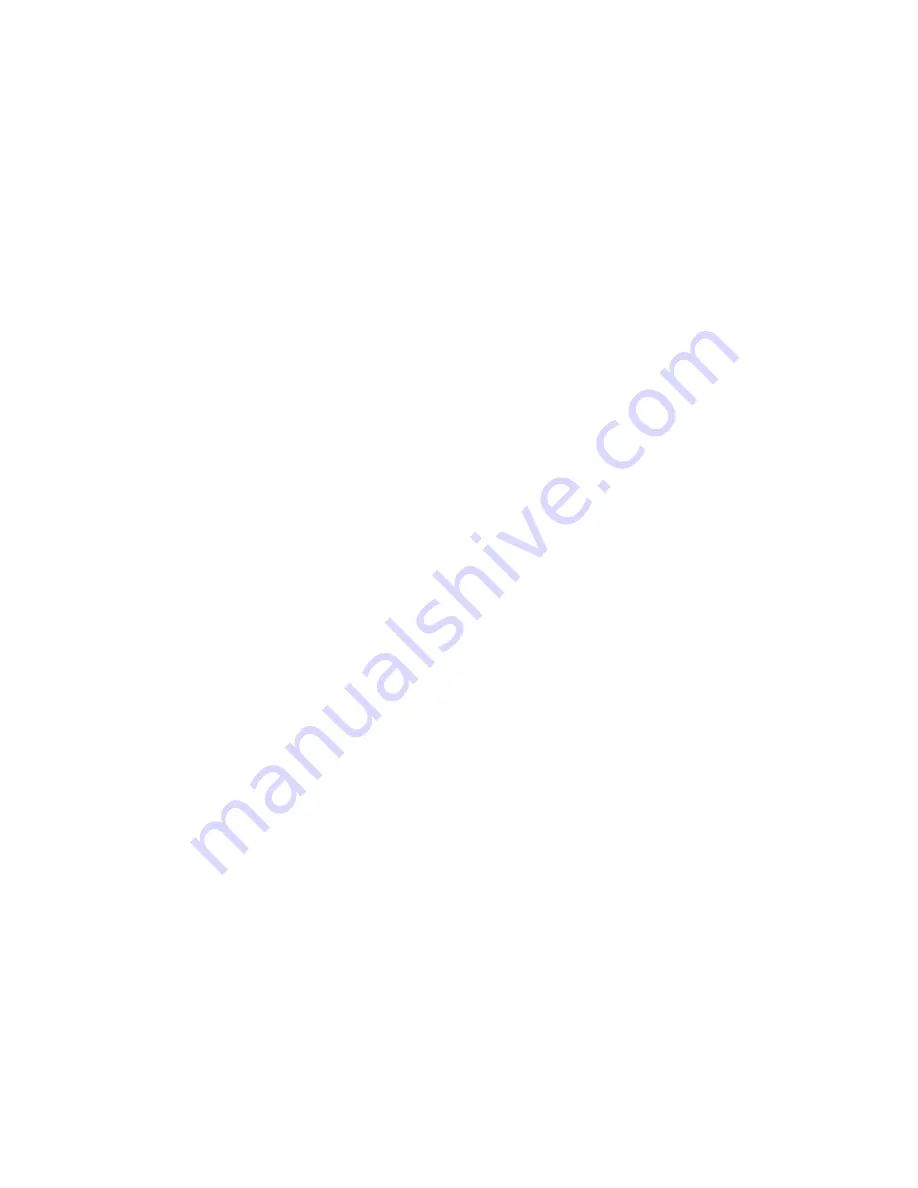
Page 22
Page 22
Page 22
Page 22
Page 22
INST
INST
INST
INST
INSTALLA
ALLA
ALLA
ALLA
ALLATION OF MO
TION OF MO
TION OF MO
TION OF MO
TION OF MOT
T
T
T
TOR
OR
OR
OR
OR AND BLOWER
AND BLOWER
AND BLOWER
AND BLOWER
AND BLOWER ASSEMBL
ASSEMBL
ASSEMBL
ASSEMBL
ASSEMBLY
Y
Y
Y
Y
FOR CISSELL FORM FINISHERS
FOR CISSELL FORM FINISHERS
FOR CISSELL FORM FINISHERS
FOR CISSELL FORM FINISHERS
FOR CISSELL FORM FINISHERS
INST
INST
INST
INST
INSTALLA
ALLA
ALLA
ALLA
ALLATION OF BLOWER
TION OF BLOWER
TION OF BLOWER
TION OF BLOWER
TION OF BLOWER
A.
Place Blower Wheel in housing with blades
at bottom cupped towards opening.
(See illustration on other side)
B.
Install cut-off sheet.
C.
Slip Shaft through center holes of Housing
and Blower Wheel.
D.
Align Blower Wheel equidistant from each
side of Housing with equal lengths of shaft
extending beyond each side of Housing.
Tighten Blower Wheel Set Screw against
flat of Shaft with fingers.
NO
NO
NO
NO
NOTE
TE
TE
TE
TE
USE ONE DROP OF LIGHTWEIGHT OIL IN
HOLE OF EACH BEARING BEFORE INSERT-
ING ON SHAFT.
E.
Install Bearing Insulator, Bearing Assembly,
and Plastic Thrust Washer on each end of
Shaft, as illustrated. Also install Thrust
Collar as illustrated. Tighten Set Screw of
Thrust Collar and Center Blower Wheel Set
Screw with a wrench.
F.
Slip Large Pulley on Blower Wheel Shaft
against Plastic Thrust Washer with Set
Screw outside. Tighten securely.
NO
NO
NO
NO
NOTE
TE
TE
TE
TE
SEE INSTRUCTIONS FOR ALIGNMENT
AND PROPER BELT TENSION.
INST
INST
INST
INST
INSTALLA
ALLA
ALLA
ALLA
ALLATION OF MO
TION OF MO
TION OF MO
TION OF MO
TION OF MOT
T
T
T
TOR
OR
OR
OR
OR
NO
NO
NO
NO
NOTE
TE
TE
TE
TE
CONDENSER MUST BE REMOVED BEFORE
REMOVING OF INSTALLING MOTOR.
A.
Install Motor Support Bar and Adjusting
Bolt on Motor before installing Motor in
Housing
B.
Place Motor in position and secure with
bolts in each end of Support Bar.
C.
Slip Small Pulley on Motor Shaft with Set
Screw out away from Motor. Have end of
Pulley flush with end of Shaft.
ALIGNMENT OF PULLEYS
ALIGNMENT OF PULLEYS
ALIGNMENT OF PULLEYS
ALIGNMENT OF PULLEYS
ALIGNMENT OF PULLEYS
NO
NO
NO
NO
NOTE
TE
TE
TE
TE
IF INSTALLATION HAS BEEN MADE
ACCORDING TO INSTRUCTIONS THE BELT
ALIGNMENT SHOULD BE CORRECT. IF
THERE SHOULD BE ANY DOUBT, CHECK
THE FOLLOWING INSTRUCTIONS.
A.
Place a straight edge against face of Large
Pully and align face of Small Pulley with
straight edge. Move Small Pulley for
adjustment. (Fig. 2)
B.
To put tension on belt turn Adjustment Bolt
Clockwise. (Use wrench) Hold bolt with
wrench, tighten Square Lock Nut clockwise
with a wrench.
BLOWER BEL
BLOWER BEL
BLOWER BEL
BLOWER BEL
BLOWER BELT SETTING EXTREMEL
T SETTING EXTREMEL
T SETTING EXTREMEL
T SETTING EXTREMEL
T SETTING EXTREMELY IMPORT
Y IMPORT
Y IMPORT
Y IMPORT
Y IMPORTANT
ANT
ANT
ANT
ANT
Improper belt tension and misalignment develop
bearing and belt failures.
FIGURES 1 and 2 deal with proper tension and
correct alignment of belts and pulleys when used
on blower applications.
FIGURE 1 indicates the recommended tension,
determined by grasping the belt as shown and
when a normal pressure is applied, a deflection of
approximately 1” in the belt will occur.
If the deflection is much in excess of that indi-
cated, belt slippage may occur and excessive belt
wear can result.
If the deflection is somewhat less than indicated,
the belt is too tight and will shorten the life of the
bearing. Excessive tension will actually pull the
shaft through the oil film in the bearing and
allow metal to metal contact. In addition to
decreasing the bearing life, it will contribute to
noisy blower operation. Any defects in the belt or
pulleys will be exaggerated.
FIGURE 2 deals with a recommended method for
checking correct alignment of pulleys. Excessive
misalignment produces increased belt wear and
can produce lateral motion of the wheel and shaft
to the point that considerable noise can develop.