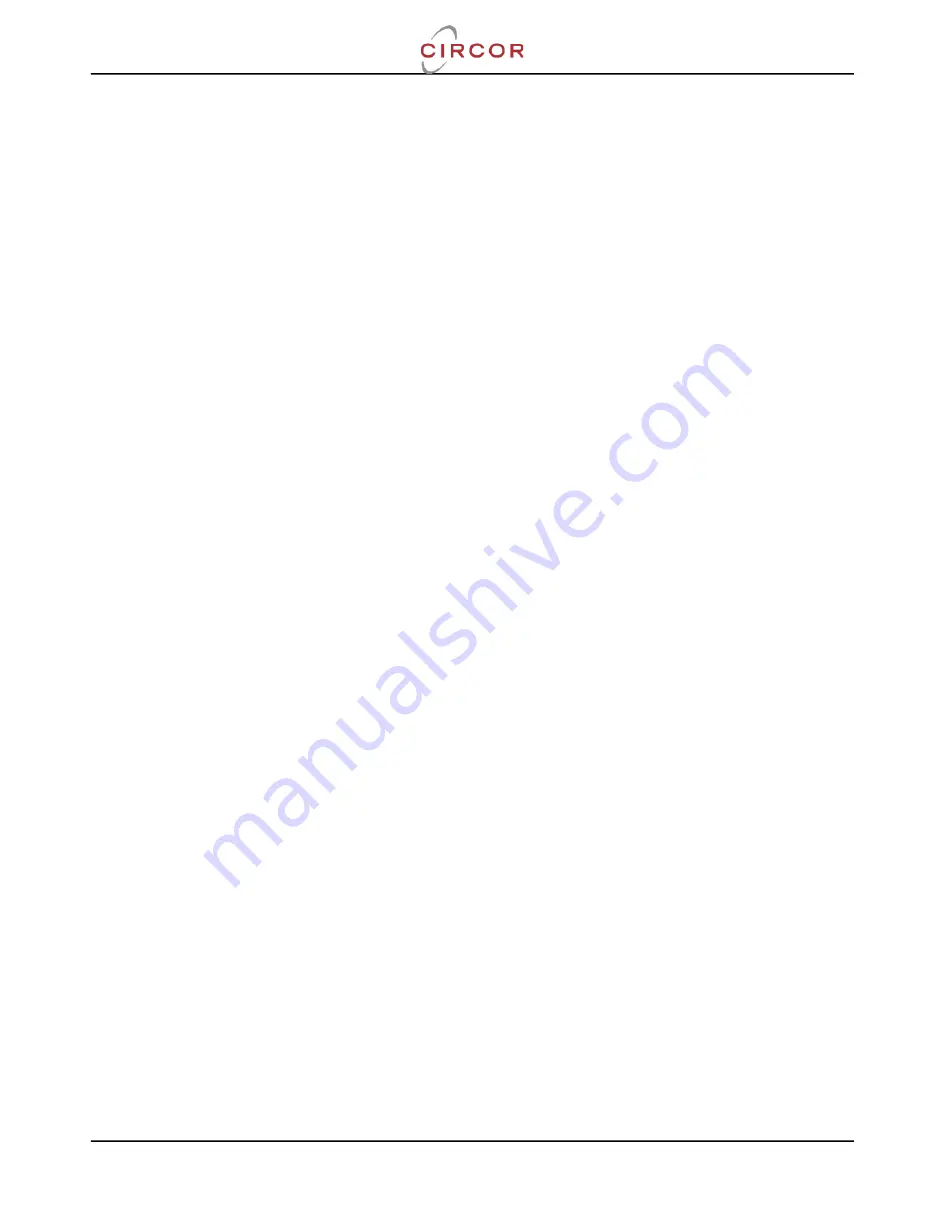
Introduction and Safety
216 Series Twin-Screw Pump -
Installation, Operation & Maintenance Manual
9
-
The pump is grounded.
-
There is no contact between the coupling and coupling guard
-
Pump interior, seal chamber, auxiliary systems, inlet and outlet piping, are always completely
filled with the liquid being pumped.
-
The maximum permissible surface temperature of the pump is not exceeded.
-
The maximum permissible fluid medium temperature is not exceeded (see 2.3)
-
Valves on the inlet and outlet of the pump are set correctly.
-
The pump has regular maintenance and monitoring.
-
It is impossible for the pump to run dry i.e, by monitoring tank levels, flow measurements, etc.
•
Ensure that the motors, couplings, gears and monitoring equipment supplied on site correspond to
the category and temperature class of the associated zone.
•
Note the information on order data sheet
•
Inform personnel regarding special dangers
- Danger of explosions through removal of dust buildup
•
All users must know about the risks of electric current and the chemical and physical characteristics
of the gas, the vapor, or both present in hazardous areas.
•
Any maintenance for Ex-approved products must conform to international and national standards (for
example, IEC/EN 60079-17).
•
CIRCOR disclaims all responsibility for work done by untrained and unauthorized personnel.
•
The yield stress of fasteners must be in accordance with the approval drawing and the product
specification.
•
Do not modify the equipment without approval from an authorized CIRCOR representative.
•
Only use parts that are provided by an authorized CIRCOR representative.
1.2 Materials
:
All pump parts and accessories must consist of electrically conductive materials.
With combustible pumped liquids, all pressure bearing parts must be of ductile material from internal
pump pressures of 10 bar (145 psi) or greater.