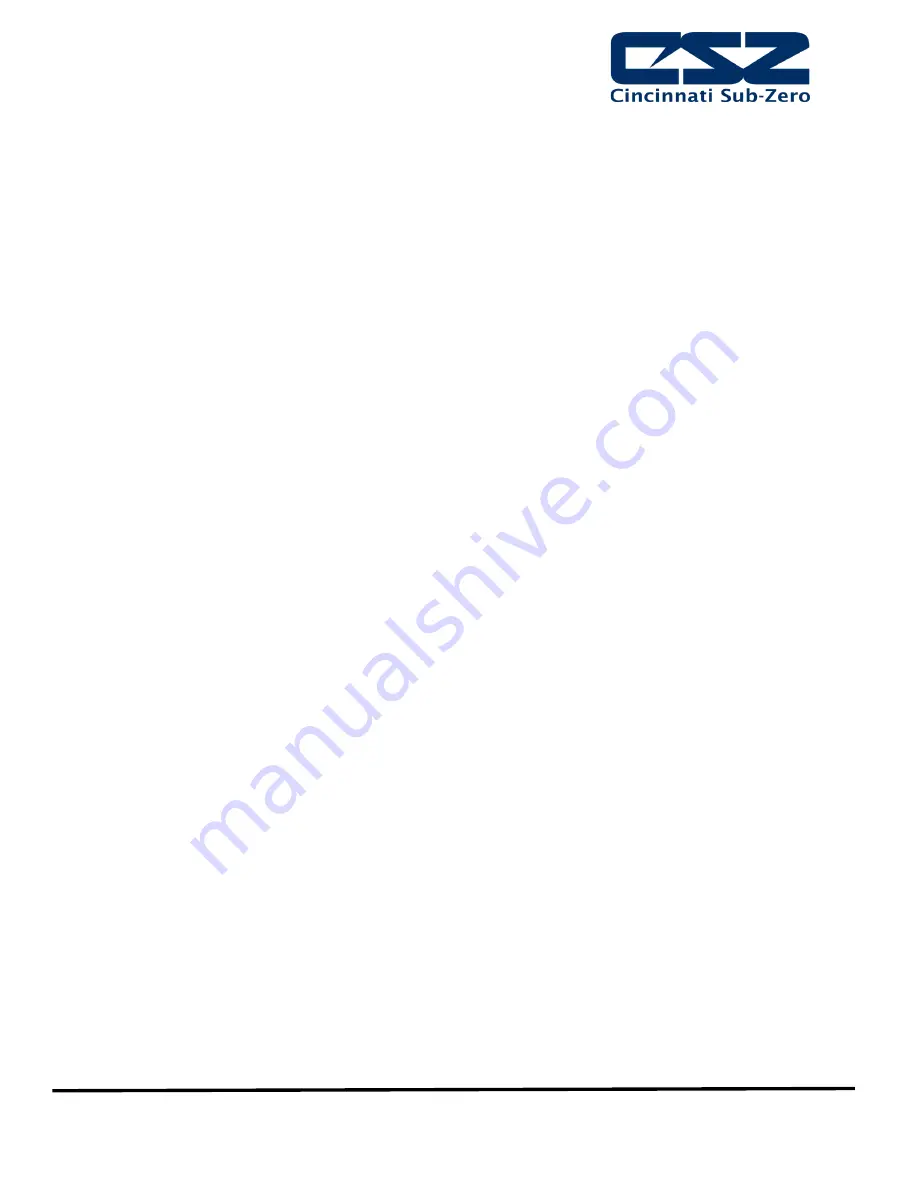
GENERAL DESCRIPTION
26
SEQUENCE OF OPERATION
CASCADE UNIT - SYSTEM 1 (R-404A) DESCRIPTION
(Refer to Refrigeration Diagram in Drawing Section)
NOTE:
Pressure settings are approximate.
The compressor (item 101) will pump compressed R-404A vapor through the discharge line where the
high-pressure gauge (item 183) displays the high-pressure of the refrigerant.
System 1 – Description (2 HP – 6 HP Systems)
The high-pressure switch (item 195) senses the discharge refrigerant pressure and will open a contact in
the event that discharge pressure exceeds 400 PSIG (27.6 bar(g)). This contact opening will serve to shut
down the unit and will automatically reset when the pressure drops to 300 PSIG (20.7 bar(g)).
System 1 – Description (10 HP – 20 HP Systems)
The high-pressure switch (item 195) senses the discharge refrigerant pressure and will open a contact in
the event that discharge pressure exceeds 350 PSIG (24.1 bar(g)). This contact opening will serve to shut
down the unit and must be manually reset.
The discharge refrigerant vapor passes a tee which diverts some of the refrigerant to the bypass loop
(see bypass description) and enters the condenser.
Air Cooled Condensing Option (2 HP – 6 HP systems)
The condenser (item 105) cools the high pressure R-404A vapor and condenses it into a high pressure
liquid. The condenser fan motor (item 196) will be energized anytime the compressor (item 101) is
running.
The high pressure liquid leaves the condenser and flows through a filter drier (item 108) and sight glass
(item 109) then passes a tee which diverts some of the liquid refrigerant to the bypass loop (see bypass
description)
Water Cooled Condensing Option (3.5 HP – 20 HP systems)
The condenser (item 105) cools the high pressure R-404A vapor and condenses it into a high pressure
liquid. The pressure actuated water valve (item 107) will maintain the discharge pressure at
approximately 210 PSIG (14.5 bar(g)).
The high pressure liquid leaves the condenser and flows through a receiver (item 122), filter drier (item
108) and sight glass (item 109) then passes a tell which diverts some of the liquid refrigerant to the
bypass loop (see bypass description).
Summary of Contents for ZP Series
Page 1: ...58911 rev B 1 2021 Installation Operation Maintenance Manual ZP Series ...
Page 4: ...THIS PAGE INTENTIONALLY LEFT BLANK ...
Page 6: ...CHAMBER LABELS AND MEANINGS ii THIS PAGE INTENTIONALLY LEFT BLANK ...
Page 12: ...TABLE OF CONTENTS viii THIS PAGE INTENTIONALLY LEFT BLANK ...
Page 24: ...GENERAL DESCRIPTION 12 Figure 2 4 Achievable Humidity Points ...
Page 52: ...GENERAL DESCRIPTION 40 THIS PAGE INTENTIONALLY LEFT BLANK ...
Page 66: ...OPERATING INSTRUCTIONS 54 THIS PAGE INTENTIONALLY LEFT BLANK ...
Page 96: ...MAINTENANCE WITH Q A 84 THIS PAGE INTENTIONALLY LEFT BLANK ...
Page 98: ...SERVICE PARTS WARRANTY 86 THIS PAGE INTENTIONALLY LEFT BLANK ...
Page 99: ...SYSTEM DIAGRAMS ELECTRICAL SCHEMATIC SYMBOLS Figure 9 1 Symbols Used on Electrical Scematics ...