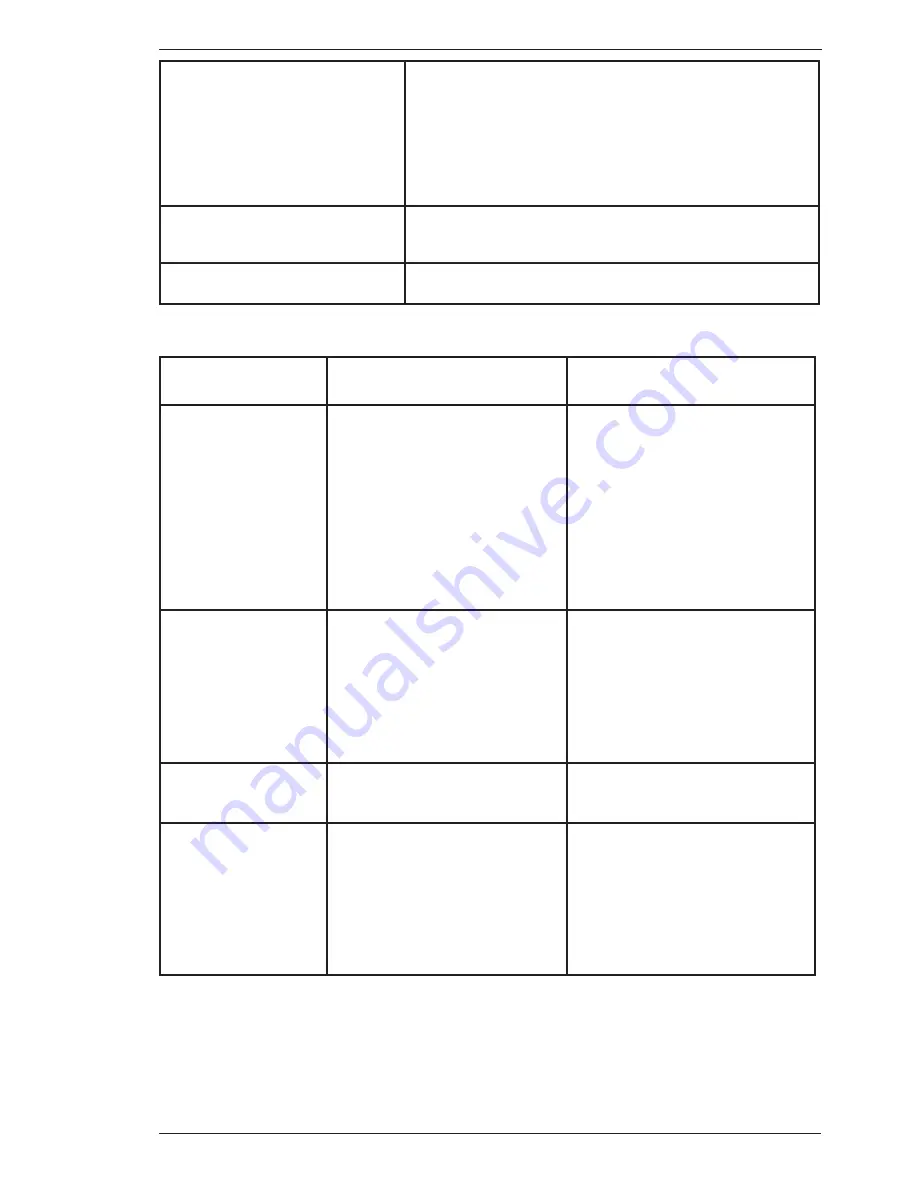
8-3
Manual No 0-5072
service weldskill 250, 350
December , 2008
6 Incorrect or worn contact tip
A
B
The contact tip transfers the weld current to the electrode wire.
If the hole in the contact tip is too large then arcing may occur
inside the contact tip resulting in the wire jamming in the contact
tip.
When using soft wire such as aluminium it may become jammed
in the contact tip due to expansion of the wire when heated. A
contact tip designed for soft wires should be used.
7 Poor work lead contact to work
piece
If the work lead has a poor electrical contact to the work piece
then the connection point will heat up and result in a reduction
of power at the arc.
8 Bent liner
This will cause friction between the wire and the liner thus
reducing wire feedability
8.07 Welding Problems
FAULT
CAUSE
REMEDY
Undercut
A
B
C
Welding arc voltage too high.
Incorrect torch angle
Excessive heat input
A
B
C
Reduce voltage by reducing the
Voltage Control switch positions
or turn the Wirespeed control knob
anticlockwise.
Adjust angle
Increase the torch travel speed
or reduce welding current by
reducing the Voltage Control
switch positions and turn the
Wirespeed control knob anti-
clockwise.
2 Lack of penetration
A
B
C
Welding current too low
Joint preparation too narrow or
gap too tight
Shielding gas incorrect
A
B
C
Increase welding current by
increasing the Wirespeed control
knob clockwise and increasing
Voltage Control switch positions.
Increase joint angle or gap
Change to a gas which gives
higher penetration
3 Lack of fusion
Arc voltage to low
Increase Arc voltage by increasing
the Voltage Control switch
positions.
4 Excessive spatter
A
B
Arc voltage too high
Arc voltage too low
A
B
Lower voltage by reducing the
Voltage Control switch positions
or turn the Wirespeed control knob
anti-clockwise.
Raise voltage by increasing the
Voltage Control switches or turn
the Wirespeed control knob
clockwise.
Summary of Contents for WeldSkill 250 MIG
Page 6: ......
Page 12: ...1 December 1 2008 weldskill 250 350 Manual No 0 5072 This page left intentionally blank...
Page 20: ...2 Manual No 0 5072 weldskill 250 350 December 1 2008 This page left intentionally blank...
Page 24: ...3 Manual No 0 5072 weldskill 250 350 December 1 2008 This page left intentionally blank...
Page 28: ...4 Manual No 0 5072 December 1 2008 weldskill 250 350 This page left intentionally blank...
Page 36: ...6 Manual No 0 5072 weldskill 250 350 December 1 2008 This page left intentionally blank...
Page 44: ...8 Manual No 0 5072 weldskill 250 350 December 1 2008 This page left intentionally blank...
Page 50: ......