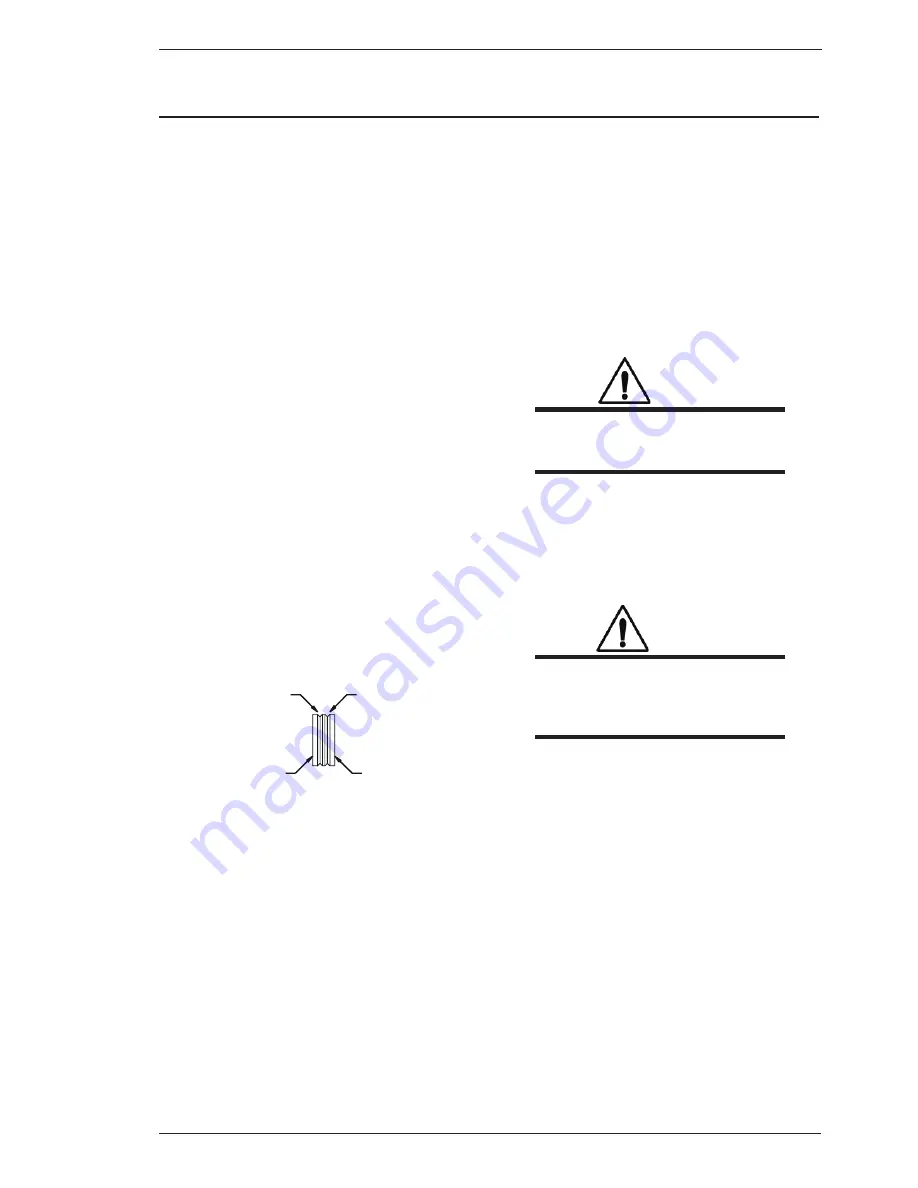
5-
Manual No 0-5072
set up weldskill 250, 350
December , 2008
SECTION 5:
SET UP FOR THE WELDSKILL 250, 350 POWER SOURCE
5.01 Power Source Connections
A. Remove all packaging materials.
B. Connect the work lead to the negative welding
terminal (-) [positive welding terminal (+) for
flux cored electrode wire]. If in doubt, consult
the electrode wire manufacturer.
C. Position a gas cylinder on the rear tray of the
Power Source and lock securely to the Power
Source cylinder bracket with the chain provided.
If this arrangement is not used or the Power
Source is not fitted with a gas cylinder tray
then ensure that the gas cylinder is secured to a
building pillar, wall bracket or otherwise securely
fixed in an upright position.
5.02 Wirefeeder Connections
A. Connect the TORCH power cable to the positive
welding terminal (+) [negative welding terminal
(-) for flux cored electrode wire]. If in doubt,
consult the electrode wire manufacturer.
B. Fit the gas regulator and flowmeter to the gas
cylinder then connect the gas hose from the rear
of the Power Source to the Flowmeter outlet.
C. Dual groove feed rollers are supplied as stan-
dard. They can accommodate 0.9 / .2 diameter
hard wires. Select the roller required with the
chosen wire size marking facing outwards.
GROOVE “B”
GROOVE “A”
GROOVE “A” SIZE
GROOVE “B” SIZE
Art # A-08739
D. Fit the electrode wire spool to the wire reel
hub. Ensure that the drive dog-pin engages the
mating hole in the wire spool. Push the 'R' clip
into place to retain the wire spool securely. The
electrode wire should feed from the bottom of
the spool.
E. MIG Torch, EURO MIG Torch Connection
Fit the MIG Torch to the Power Source by pushing
the torch connector into the brass torch adaptor
and screwing the plastic torch nut clockwise to
secure the torch to the torch adaptor. Remove
the contact tip from the torch handset.
5.03 Common Connections
A. Lift up the wire feeder pressure levers and
pass the electrode wire through the inlet guide,
between the rollers, through the centre guide,
between the rollers, through the outlet guide
and into the MIG torch.
B. Lift up the wire feeder pressure levers and
pass the electrode wire through the inlet guide,
between the rollers, through the centre guide,
between the rollers, through the outlet guide
and into the MIG torch.
WARNING
D O N O T W E A R G L O V E S W H I L E
THREADING THE WIRE OR CHANGING
THE WIRE SPOOL.
C. Lower the pressure levers and with the torch
lead reasonably straight, feed the electrode
wire through the torch. Fit the appropriate
contact tip, eg a 0.9mm tip for 0.9mm wire.
D. Press the Torch switch to feed the wire
through the torch.
WARNING
The electrode wire will be at welding volt-
age potential whilst it is being fed through
the wirefeeder system if the wire is fed by
using the TORCH SWITCH.
5.04 Drive Roller Pressure Adjustment
The moveable rollers apply pressure to the grooved
feed rollers via a scaled adjustable tension screw.
These devices should be adjusted to a minimum
pressure that will provide satisfactory WIREFEED
without slippage. If slipping occurs, and inspection
of the wire contact tip reveals no wear, distortion or
burn back jam, the conduit liner should be checked
for kinks and clogging by metal flakes and swarf. If
it is not the cause of slipping, the feedroll pressures
can be increased by rotating the scaled tension screws
clockwise. The use of excessive pressure may cause
rapid wear of the feed rollers, shafts and bearing.
Summary of Contents for WeldSkill 250 MIG
Page 6: ......
Page 12: ...1 December 1 2008 weldskill 250 350 Manual No 0 5072 This page left intentionally blank...
Page 20: ...2 Manual No 0 5072 weldskill 250 350 December 1 2008 This page left intentionally blank...
Page 24: ...3 Manual No 0 5072 weldskill 250 350 December 1 2008 This page left intentionally blank...
Page 28: ...4 Manual No 0 5072 December 1 2008 weldskill 250 350 This page left intentionally blank...
Page 36: ...6 Manual No 0 5072 weldskill 250 350 December 1 2008 This page left intentionally blank...
Page 44: ...8 Manual No 0 5072 weldskill 250 350 December 1 2008 This page left intentionally blank...
Page 50: ......