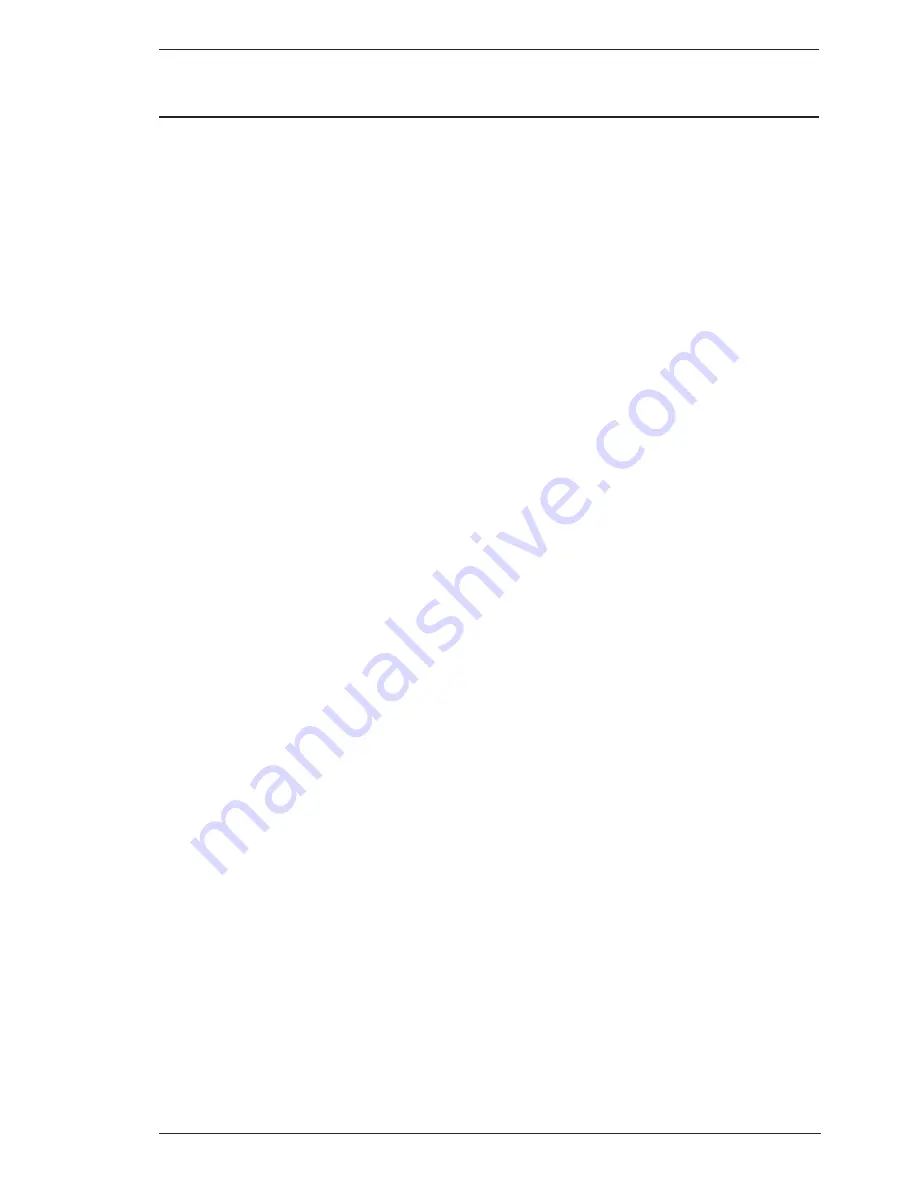
4-
Manual No 0-5072
safe practices weldskill 250, 350
December , 2008
SECTION 4:
SAFE PRACTICES FOR THE USE OF WELDING EQUIPMENT
In many situations the “striking” voltage can be hazardous. Any person touching simultaneously the electrode
lead/terminal and the work lead/terminal may receive a serious electrical shock. Additional precautions must
be exercised where two Welding Power Sources are being used close to each other because, under certain
conditions, the voltages between the welding terminals of the two Welding Power Sources could be two times
the specified open circuit voltage.
It is essential that the Welding Power Source is correctly installed, if necessary, by a qualified electrician and
maintained in sound mechanical and electrical condition. It is also important that the Welding Power Source
be switched off when not in use.
4.01 Precautions to be Taken by
Operators
• Whenever practicable, all parts of the welding
circuit should be isolated from earth and other
conducting material and under no circumstances
should any earthing conductor of the electrical
installation be used in place of the work lead.
• The Mains supply voltage should be switched
off before connecting or disconnecting welding
leads. Welding lead connections must have
clean contact surfaces and must be securely
tightened. Poor connections will result in over-
heating and loss of welding current. All parts of
the welding circuit, including the return paths,
are to be considered electrically alive, so the
operator must ensure that no part of the body
is placed in such a position that it will provide
a path for an electric current.
• Welding operators should avoid direct contact
with the work to be welded or against any metal
in contact with the work. When this cannot be
avoided the operator must not touch any ex-
posed portion of the electrode holder with any
part of the body. Should this occur, the operator
will risk completing the electrical circuit through
the body.
• When welding in confined spaces, where rea-
sonable movement is restricted, particular care
must be taken to ensure that the area is well
ventilated and the operator is under constant
observation by a person who can immediately
switch off the power and give assistance in an
emergency.
• The flux covering of an electrode cannot be
assumed to provide effective insulation, conse-
quently an insulating glove must be worn when
placing an electrode into its holder, or should it
be necessary to handle an electrode once it is
in contact with its holder.
• During pauses between welding runs, electrode
holders, TIG torches and MIG torches should
be so placed that they cannot make electrical
contact with persons or conductive objects.
• The welding leads, both the electrode lead, TIG
torch lead or MIG torch lead and the work lead,
must be protected from damage. Damaged
leads must not be used.
• Keep combustible materials away from the
welding area. Have a suitable fire extinguisher
handy.
• Do not stand on damp ground when welding.
4.02 Personal Protection
The radiation from an electric arc during the welding
process can seriously harm eyes and skin. It is es-
sential that the following precautions be taken:
• Gloves should be flameproof gauntlet type to
protect hands and wrists from heat burns and
harmful radiations. They should be kept dry and
in good repair.
• Protective clothing must protect the operator
from burns, spatter and harmful radiation.
Woollen clothing is preferable to cotton because
of its greater flame resistance. Clothing should
be free from oil or grease. Wear leggings and
spats to protect the lower portion of the legs and
to prevent slag and molten metal from falling
into boots or shoes.
• Welding Faceshield
It is a requirement to use a welding Faceshield,
complying to a relevant standard, when electric
arc welding. Use a welding Faceshield in ser-
viceable condition and fitted with an eye filter
lens to safely reduce harmful radiation from the
arc as per Table 4-.
Summary of Contents for WeldSkill 250 MIG
Page 6: ......
Page 12: ...1 December 1 2008 weldskill 250 350 Manual No 0 5072 This page left intentionally blank...
Page 20: ...2 Manual No 0 5072 weldskill 250 350 December 1 2008 This page left intentionally blank...
Page 24: ...3 Manual No 0 5072 weldskill 250 350 December 1 2008 This page left intentionally blank...
Page 28: ...4 Manual No 0 5072 December 1 2008 weldskill 250 350 This page left intentionally blank...
Page 36: ...6 Manual No 0 5072 weldskill 250 350 December 1 2008 This page left intentionally blank...
Page 44: ...8 Manual No 0 5072 weldskill 250 350 December 1 2008 This page left intentionally blank...
Page 50: ......