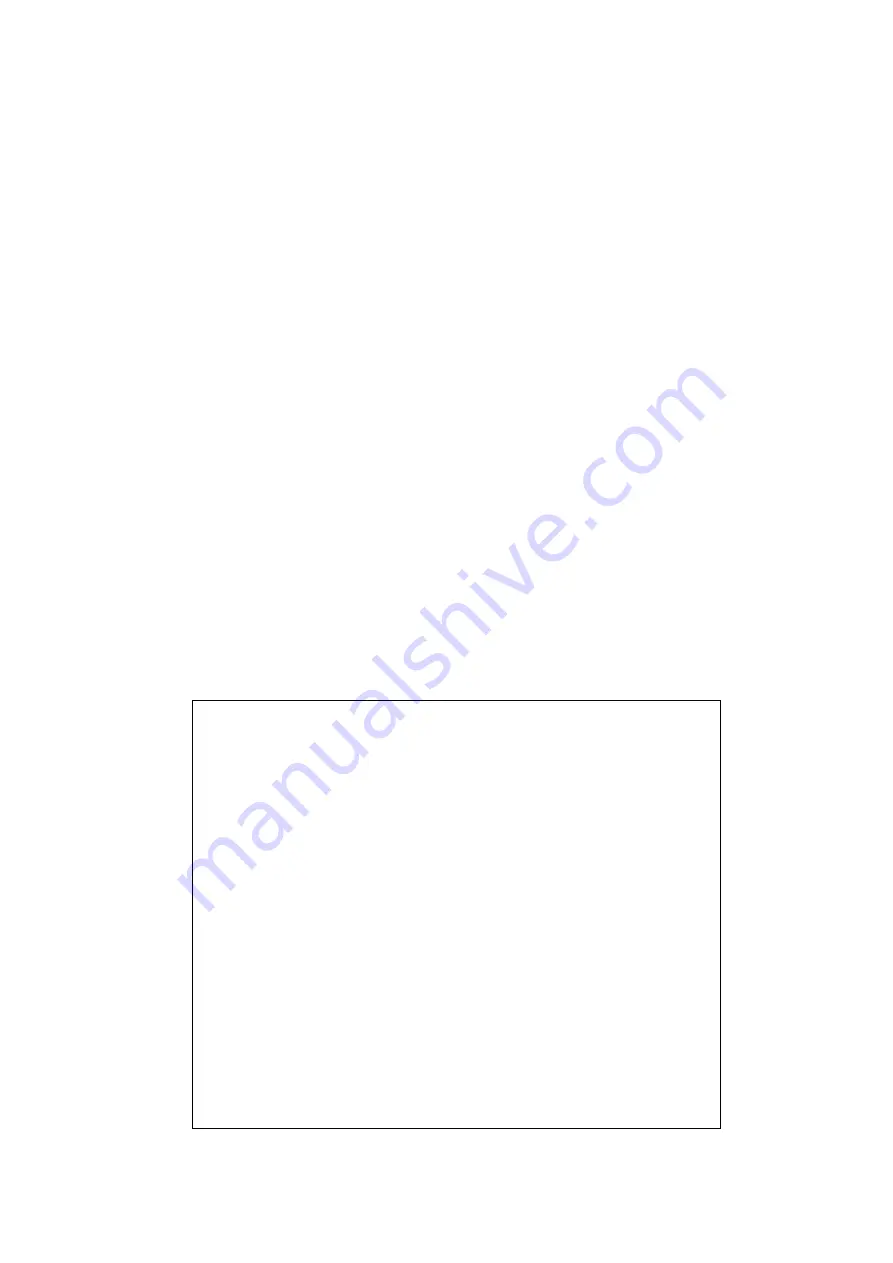
50
Maintenance
Complete an operating statement and perform the checks
listed in the table above at least twice a year and, without fail,
whenever units which are used on a seasonal basis are
restarted. Keep the unit clean.
- Keep the space around the unit clean and unobstructed in
order to avoid accidents and ensure that the condensor is
correctly ventilated.
- Check for clogging-up of the coil if necessary, remove dust,
fibres, leaves etc. using a soft brush or a vacuum cleaner. It can
also be cleaned with a water jet:
■
at low pressure
■
in the direction of the fins
■
in the opposite direction to the air
IMPORTANT
: to ensure correct operation of the unit and be
able to make use of the guarantee: sign a maintenance
contract with your installer or an approved maintenance
company.
Safety instructions
Verifications of the operating unit must be performed in
compliance with national regulations.
Do not climb on the machine. Use a platform to work at
machine height.
Do not mount on copper refrigerant piping.
Operations to the electrical or refrigerant elements may only be
peformed by qualified, authorised engineers.
Any operations (opening or closing) to an isolating valve must
be performed with the unit stopped.
The liquid valve (located after the dryer) must always be fully
open when there is refrigerant liquid in the circuit.
Never perform any operation on any electrical component
without first having cut the general power supply to the
unit with the isolator located at the electrical panel. This is
because even if the compressors are stopped, voltage is
still applied to the power circuit until the unit’s isolator has
been opened.
Furthermore, there might still be live elements; this is due
to external slavings connected on the orange colour
sectionnable contacts located on the main terminal
Remove the sectionnable part of these contacts before
intervention
The surfaces of the compressor and the piping may reach
temperatures greater than 100°C and result in skin burns.
Similarly, under certain conditions, the surfaces of the
compressors may sink to very low temperatures and
present a risk of freezing.
Particular care is therefore necessary during maintenance
operations.
Engineers working on the unit must wear the necessary
safety equipment (gloves, goggles, isolating clothing,
safety boots etc.).
Noise
Similarly, it is advisable for personnel working close to sources
of high noise emission to wear ear-muffs. These ear-muffs
should in no way impede the wearing of the other protective
equipment.
Oil
The oils used for refrigerating machines present very little
danger to health provided that the proper precautions are
taken during their use:
- Avoid handling components lubricated with oil unless
necessary. Use protective creams.
- Oils are inflammable and must be stored and handled with
care. Any rags or “Disposable” cloths used for cleaning must be
kept away from unprotected flames and must be disposed of in
accordance with the proper procedures.
- Cans must be stored closed. Do not use oil from an open can
which has been stored in poor conditions.
In accordance with Regulation (EC) No. 842/2006 on certain greenhouse gases.
R410A, R134a and R407C are refrigerant fluids with the following environmental
impacts:
1/Non-ozone depleting: Ozone Depletion Potential (ODP) of 0.
2/Impact on the greenhouse effect: Global Warming Potential (GWP) of each gas.
- R410A----------GWP=1975
- R407C----------GWP=1652
- R134a-----------GWP=1300
- Users must have systems containing refrigerant periodically checked for leaks by
qualified personnel. The frequency of checks depends on the refrigerant charge:
- Every 12 months for units containing 3 to 30 kg of refrigerant (2 kg in France, decree
and order dated 7 May 2007) .
- Every 6 months for units containing 30 to 300 kg of refrigerant.
- Every 3 months for units containing over 300 kg of refrigerant (a leak detection
system must be installed).
- Users of any system containing over 3 kg of refrigerant (2 kg in France) are required
to keep a log of the quantities and types of refrigerants used, added or recovered, and
to include the dates and results of leak tests, as well as the name of the technician and
the technician's company.
- A leak test must be carried out one month following any leak repairs.
- System users are responsible for collecting used refrigerant and having it recycled,
regenerated or destroyed.