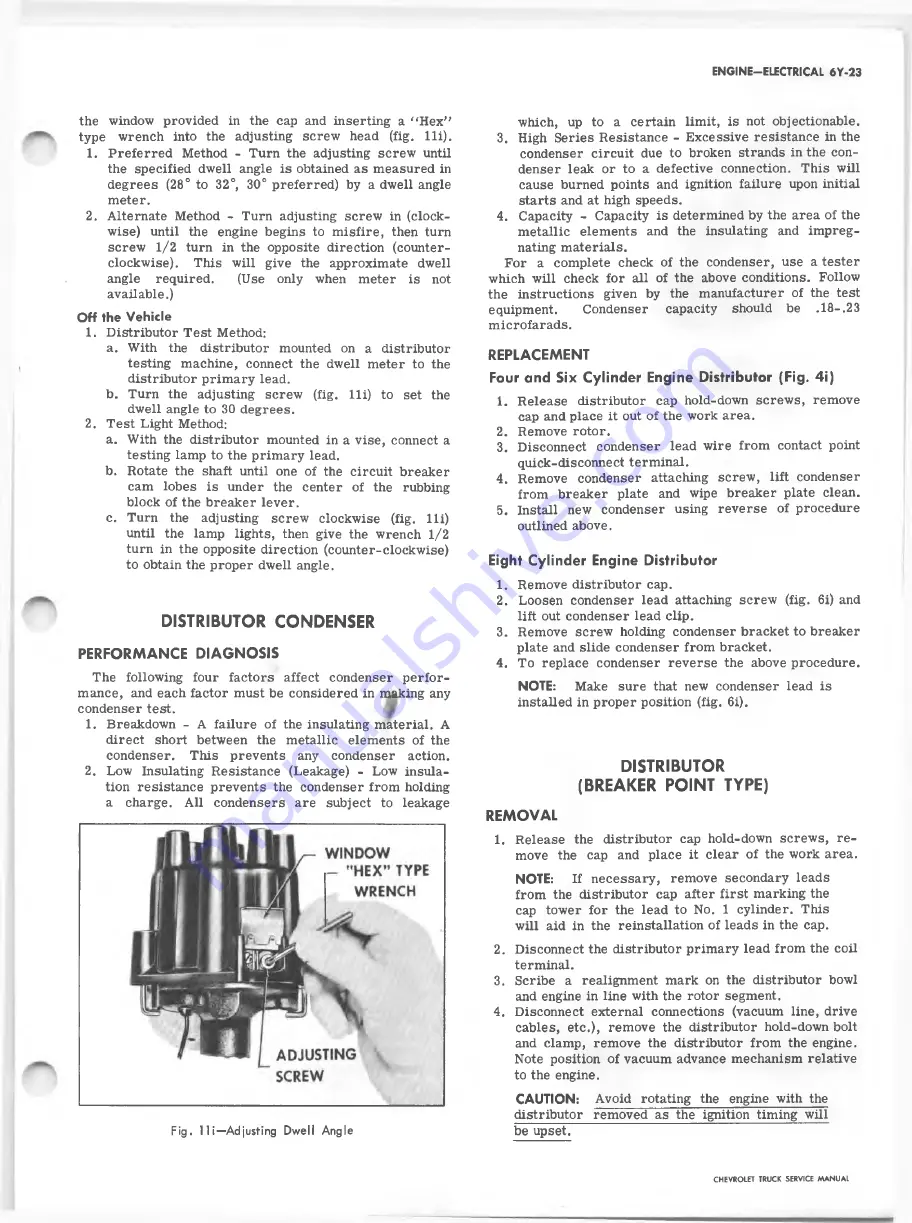
ENGINE-ELECTRICAL 6Y-23
the window provided in the cap and inserting a "Hex”
type wrench into the adjusting screw head (fig. H i).
1. Preferred Method - Turn the adjusting screw until
the specified dwell angle is obtained as measured in
degrees (28° to 32°, 30° preferred) by a dwell angle
meter.
2. Alternate Method - Turn adjusting screw in (clock
wise) until the engine begins to m isfire, then turn
screw
1 / 2
turn in the opposite direction (counter
clockwise). This will give the approximate dwell
angle required.
(Use only when meter is not
available.)
Off the Vehicle
1. Distributor Test Method:
a. With the distributor mounted on a distributor
testing machine, connect the dwell meter to the
distributor primary lead.
b. Turn the adjusting screw (fig. lli) to set the
dwell angle to 30 degrees.
2. Test Light Method:
a. With the distributor mounted in a vise, connect a
testing lamp to the primary lead.
b. Rotate the shaft until one of the circuit breaker
cam lobes is under the center of the rubbing
block of the breaker lever.
c. Turn the adjusting screw clockwise (fig. lli)
until the lamp lights, then give the wrench
1 / 2
turn in the opposite direction (counter-clockwise)
to obtain the proper dwell angle.
DISTRIBUTOR CONDENSER
PERFORMANCE DIAGNOSIS
The following four factors affect condenser perfor
mance, and each factor must be considered in making any
condenser test.
1. Breakdown - A failure of the insulating material. A
direct short between the metallic elements of the
condenser. This prevents any condenser action.
2. Low Insulating Resistance (Leakage) - Low insula
tion resistance prevents the condenser from holding
a charge. All condensers are subject to leakage
F ig . 11 i —Adjusting Dw ell Angle
which, up to a certain limit, is not objectionable.
3. High Series Resistance - Excessive resistance in the
condenser circuit due to broken strands in the con
denser leak or to a defective connection. This will
cause burned points and ignition failure upon initial
starts and at high speeds.
4. Capacity - Capacity is determined by the area of the
metallic elements and the insulating and impreg
nating m aterials.
For a complete check of the condenser, use a tester
which will check for all of the above conditions. Follow
the instructions given by the manufacturer of the test
equipment.
Condenser
capacity should be .18-. 2 3
microfarads.
REPLACEMENT
Four and Six Cylinder Engine Distributor (Fig. 4i)
1. Release distributor cap hold-down screws, remove
cap and place it out of the work area.
2. Remove rotor.
3. Disconnect condenser lead wire from contact point
quick-disconnect terminal.
4. Remove condenser attaching screw, lift condenser
from breaker plate and wipe breaker plate clean.
5. Install new condenser using reverse of procedure
outlined above.
Eight Cylinder Engine Distributor
1. Remove distributor cap.
2. Loosen condenser lead attaching screw (fig.
6
i) and
lift out condenser lead clip.
3. Remove screw holding condenser bracket to breaker
plate and slide condenser from bracket.
4. To replace condenser reverse the above procedure.
NOTE:
Make sure that new condenser lead is
installed in proper position (fig.
6
i).
DISTRIBUTOR
(BREAKER POINT TYPE)
REMOVAL
1. Release the distributor cap hold-down screws, re
move the cap and place it clear of the work area.
NOTE:
If necessary, remove secondary leads
from the distributor cap after first marking the
cap tower for the lead to No. 1 cylinder. This
will aid in the reinstallation of leads in the cap.
2. Disconnect the distributor primary lead from the coil
terminal.
3. Scribe a realignment mark on the distributor bowl
and engine in line with the rotor segment.
4. Disconnect external connections (vacuum line, drive
cables, etc.), remove the distributor hold-down bolt
and clamp, remove the distributor from the engine.
Note position of vacuum advance mechanism relative
to the engine.
CAUTION:
Avoid rotating the engine with the
distributor removed as the ignition timing will
be upset.
CHEVROLET TRUCK SERVICE MANUAL
Summary of Contents for 10 Series 1967
Page 1: ...CHASSIS V3 a n s W U gw...
Page 2: ......
Page 28: ......
Page 80: ...BODY IB 18 Fig 41 Exploded View of Level Ride Seat CHEVROLET TRUCK SERVICE MANUAL...
Page 89: ...BODY IB 27 CHEVROLET TRUCK SERVICE MANUAL...
Page 105: ...BODY IB 43 Fig 94 Check Link Assembly Typical CHEVROLET TRUCK SERVICE MANUAL...
Page 117: ...BODY IB 55 Fig 116 A uxiliary Seat CHEVROLET TRUCK SERVICE MANUAL...
Page 121: ...Fig 4 1 0 3 0 Series Truck Frame...
Page 122: ...Fig 5 4 0 6 0 Single A xle Truck Frames Exc T ilt Cab FRAME 2 4...
Page 124: ...CHEVROLET TRUCK SERVICE MANUAL 1 Ficu 7 4 0 6 0 Series T ilt Cab Truck Frames FRAME 2 6...
Page 228: ...BRAKES 5 12 TD 50 60 Fig 23 Parking Brake Cables T Models CHEVROLET TRUCK SERVICE MANUAL...
Page 280: ......
Page 324: ...I I...
Page 336: ...ENGINE FUEL 6M 12 CHEVROLET TRUCK SERVICE MANUAL...
Page 342: ......
Page 348: ......
Page 386: ......
Page 393: ...CHEVROLET TRUCK SERVICE MANUAL CLUTCHES AND TRANSMISSIONS 7 7...
Page 472: ...STEERING 9 18 Fig 31 Typical Power Steering Hose Routing CHEVROLET TRUCK SERVICE MANUAL...
Page 474: ...w j...
Page 486: ......
Page 500: ...1...
Page 502: ...l c t r iC al 12 2...
Page 568: ......
Page 576: ......
Page 580: ...1...
Page 587: ...SPECIFICATIONS 7 ENGINE SECTION 6 8 25 1 on CE TE400 Series CHEVROLET TRUCK SERVICE MANUAL...
Page 590: ...SPECIFICATIONS 10 ENGINE TORQUES CHEVROLET TRUCK SERVICE MANUAL...