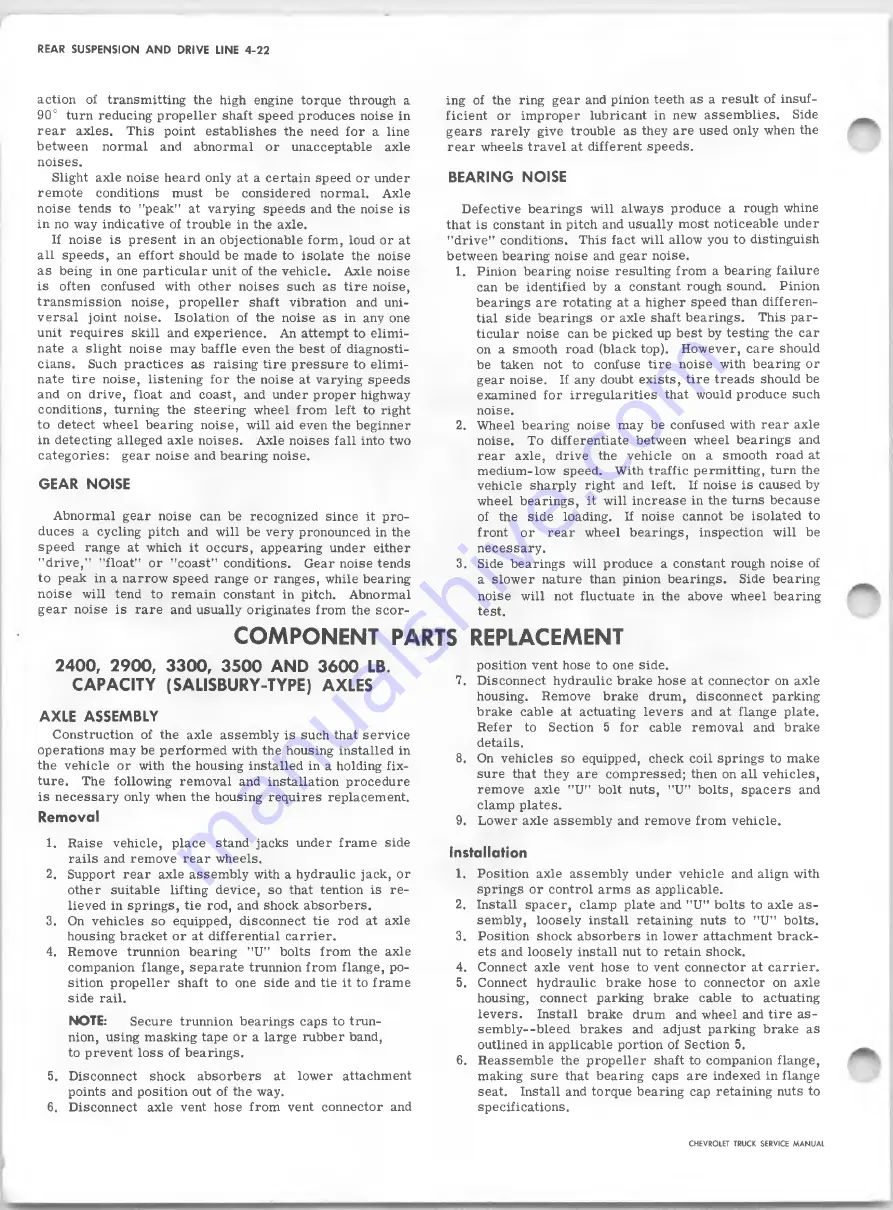
REAR SUSPENSION AND DRIVE LINE 4-22
action of transmitting the high engine torque through a
90° turn reducing propeller shaft speed produces noise in
rear axles. This point establishes the need for a line
between normal and abnormal or unacceptable axle
noises.
Slight axle noise heard only at a certain speed or under
remote conditions must be considered normal. Axle
noise tends to "peak" at varying speeds and the noise is
in no way indicative of trouble in the axle.
If noise is present in an objectionable form, loud or at
all speeds, an effort should be made to isolate the noise
as being in one particular unit of the vehicle. Axle noise
is often confused with other noises such as tire noise,
transmission noise, propeller shaft vibration and uni
versal joint noise. Isolation of the noise as in any one
unit requires skill and experience. An attempt to elimi
nate a slight noise may baffle even the best of diagnosti
cians. Such practices as raising tire pressure to elimi
nate tire noise, listening for the noise at varying speeds
and on drive, float and coast, and under proper highway
conditions, turning the steering wheel from left to right
to detect wheel bearing noise, will aid even the beginner
in detecting alleged axle noises. Axle noises fall into two
categories: gear noise and bearing noise.
GEAR NOISE
Abnormal gear noise can be recognized since it pro
duces a cycling pitch and will be very pronounced in the
speed range at which it occurs, appearing under either
"drive," "float" or "coast" conditions. Gear noise tends
to peak in a narrow speed range or ranges, while bearing
noise will tend to remain constant in pitch. Abnormal
gear noise is rare and usually originates from the scor-
COMPONENT
Pt
2400, 2900, 3300, 3500 AND 3600 LB.
CAPACITY (SALISBURY-TYPE) AXLES
AXLE ASSEMBLY
Construction of the axle assembly is such that service
operations may be performed with the housing installed in
the vehicle or with the housing installed in a holding fix
ture. The following removal and installation procedure
is necessary only when the housing requires replacement.
Removal
1. Raise vehicle, place stand jacks under frame side
rails and remove rear wheels.
2. Support rear axle assembly with a hydraulic jack, or
other suitable lifting device, so that tention is re
lieved in springs, tie rod, and shock absorbers.
3. On vehicles so equipped, disconnect tie rod at axle
housing bracket or at differential carrier.
4. Remove trunnion bearing "U" bolts from the axle
companion flange, separate trunnion from flange, po
sition propeller shaft to one side and tie it to frame
side rail.
NOTE:
Secure trunnion bearings caps to trun
nion, using masking tape or a large rubber band,
to prevent loss of bearings.
5. Disconnect shock absorbers at lower attachment
points and position out of the way.
6
. Disconnect axle vent hose from vent connector and
ing of the ring gear and pinion teeth as a result of insuf
ficient or improper lubricant in new assemblies. Side
gears rarely give trouble as they are used only when the
rear wheels travel at different speeds.
BEARING NOISE
Defective bearings will always produce a rough whine
that is constant in pitch and usually most noticeable under
"drive" conditions. This fact will allow you to distinguish
between bearing noise and gear noise.
1. Pinion bearing noise resulting from a bearing failure
can be identified by a constant rough sound. Pinion
bearings are rotating at a higher speed than differen
tial side bearings or axle shaft bearings. This par
ticular noise can be picked up best by testing the car
on a smooth road (black top). However, care should
be taken not to confuse tire noise with bearing or
gear noise. If any doubt exists, tire treads should be
examined for irregularities that would produce such
noise.
2. Wheel bearing noise may be confused with rear axle
noise. To differentiate between wheel bearings and
rear axle, drive the vehicle on a smooth road at
medium-low speed. With traffic permitting, turn the
vehicle sharply right and left. If noise is caused by
wheel bearings, it will increase in the turns because
of the side loading. If noise cannot be isolated to
front or rear wheel bearings, inspection will be
necessary.
3. Side bearings will produce a constant rough noise of
a slower nature than pinion bearings. Side bearing
noise will not fluctuate in the above wheel bearing
test.
S REPLACEMENT
position vent hose to one side.
7. Disconnect hydraulic brake hose at connector on axle
housing. Remove brake drum, disconnect parking
brake cable at actuating levers and at flange plate.
Refer to Section 5 for cable removal and brake
details.
8
. On vehicles so equipped, check coil springs to make
sure that they are compressed; then on all vehicles,
remove axle "U" bolt nuts, "U" bolts, spacers and
clamp plates.
9. Lower axle assembly and remove from vehicle.
Installation
1. Position axle assembly under vehicle and align with
springs or control arms as applicable.
2. Install spacer, clamp plate and "U" bolts to axle as
sembly, loosely install retaining nuts to "U" bolts.
3. Position shock absorbers in lower attachment brack
ets and loosely install nut to retain shock.
4. Connect axle vent hose to vent connector at carrier.
5. Connect hydraulic brake hose to connector on axle
housing, connect parking brake cable to actuating
levers. Install brake drum and wheel and tire as
sembly--bleed brakes and adjust parking brake as
outlined in applicable portion of Section 5.
6
. Reassemble the propeller shaft to companion flange,
making sure that bearing caps are indexed in flange
seat. Install and torque bearing cap retaining nuts to
specifications.
CHEVROLET TRUCK SERVICE M ANUAL
Summary of Contents for 10 Series 1967
Page 1: ...CHASSIS V3 a n s W U gw...
Page 2: ......
Page 28: ......
Page 80: ...BODY IB 18 Fig 41 Exploded View of Level Ride Seat CHEVROLET TRUCK SERVICE MANUAL...
Page 89: ...BODY IB 27 CHEVROLET TRUCK SERVICE MANUAL...
Page 105: ...BODY IB 43 Fig 94 Check Link Assembly Typical CHEVROLET TRUCK SERVICE MANUAL...
Page 117: ...BODY IB 55 Fig 116 A uxiliary Seat CHEVROLET TRUCK SERVICE MANUAL...
Page 121: ...Fig 4 1 0 3 0 Series Truck Frame...
Page 122: ...Fig 5 4 0 6 0 Single A xle Truck Frames Exc T ilt Cab FRAME 2 4...
Page 124: ...CHEVROLET TRUCK SERVICE MANUAL 1 Ficu 7 4 0 6 0 Series T ilt Cab Truck Frames FRAME 2 6...
Page 228: ...BRAKES 5 12 TD 50 60 Fig 23 Parking Brake Cables T Models CHEVROLET TRUCK SERVICE MANUAL...
Page 280: ......
Page 324: ...I I...
Page 336: ...ENGINE FUEL 6M 12 CHEVROLET TRUCK SERVICE MANUAL...
Page 342: ......
Page 348: ......
Page 386: ......
Page 393: ...CHEVROLET TRUCK SERVICE MANUAL CLUTCHES AND TRANSMISSIONS 7 7...
Page 472: ...STEERING 9 18 Fig 31 Typical Power Steering Hose Routing CHEVROLET TRUCK SERVICE MANUAL...
Page 474: ...w j...
Page 486: ......
Page 500: ...1...
Page 502: ...l c t r iC al 12 2...
Page 568: ......
Page 576: ......
Page 580: ...1...
Page 587: ...SPECIFICATIONS 7 ENGINE SECTION 6 8 25 1 on CE TE400 Series CHEVROLET TRUCK SERVICE MANUAL...
Page 590: ...SPECIFICATIONS 10 ENGINE TORQUES CHEVROLET TRUCK SERVICE MANUAL...