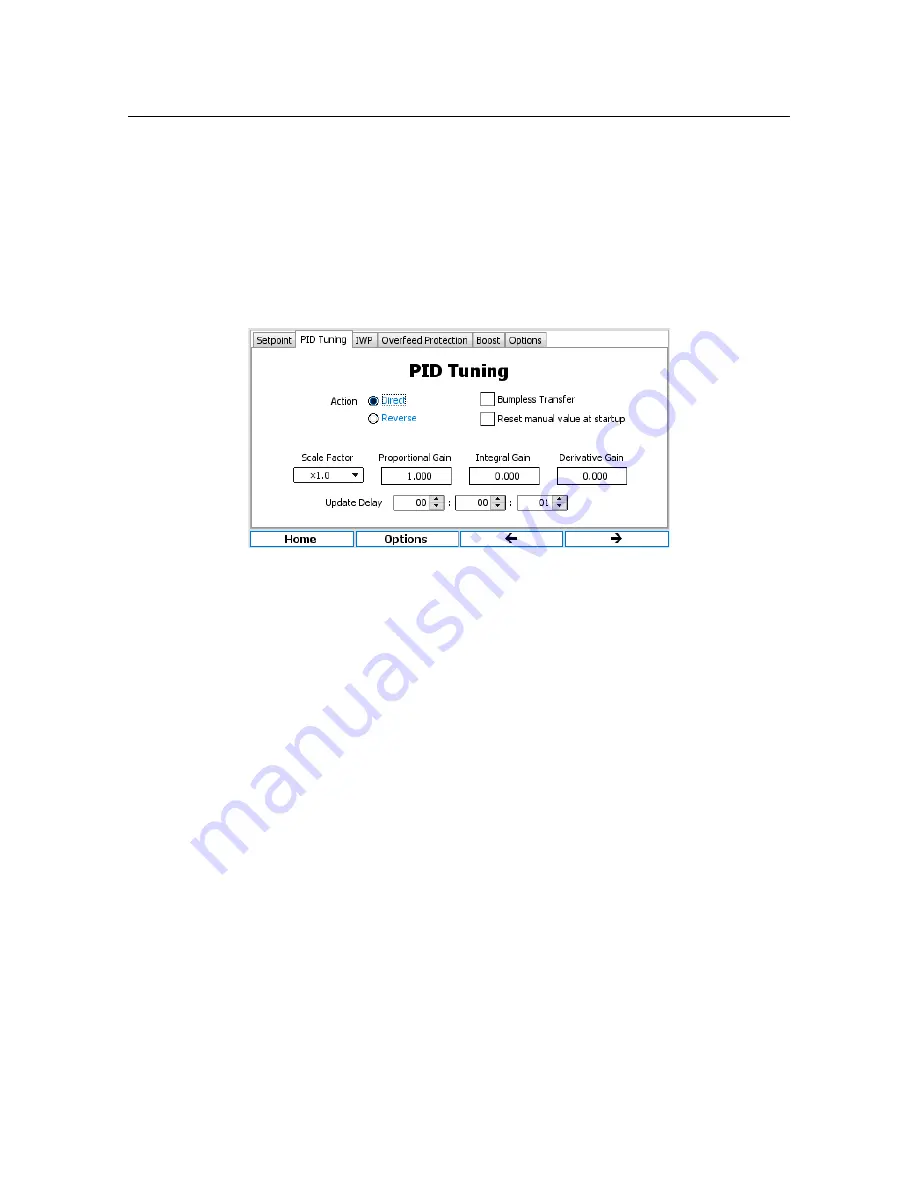
68
Chapter 4. Controls
Ramping
Enable or disable setpoint ramping. Large step changes in process variable errors can pro-
duce excessive PID output movements that could result in large over or undershoot, particularly
for controllers using the I or D terms. These step changes are likely when the controller is first
switched on or if the setpoint is changed. Setpoint ramping gradually moves the setpoint from its
current value, or current process variable reading when the controller is first turned on, to the
target value. This avoids the discontinuity present in a simple step change.
Ramping Factor
If ramping is enabled, set the ramping factor. Values from 0.00 to 1.00. A value of
0.00 will prevent the setpoint from ramping at all, while a value of 1.00 will effectively turn this
feature off.
4.1.2.4.2
PID Tuning Tab
Action
Select “Direct” if dosing increases process variable value (e.g., sodium hypochlorite addition
increases free chlorine reading), or “Reverse” if dosing decreases value (e.g., acid dosing
decreases pH).
Bumpless Transfer
Bumpless transfer is only applied when the controller is running. It will not
operate during the start delay. Bumpless transfer is designed to allow smooth transitions between
automatic and manual control modes. It avoids large changes in pump output when changing
the control mode. Bumpless transfer from automatic to manual control sets the manual output
value to the last calculated control output. For bumpless transfer from manual to automatic mode,
some integral control must be used. The initial integral error is set so that the pump output is
equal to the current manual value. The PID algorithm will then make appropriate changes to this
value to achieve the setpoint.
Scale Factor
Scaling factor applied to calculated error. For example, a scaling factor
×
1000.0 will
convert an ORP reading (
±
2000mV) into a -2.0..+2.0 error range to which the proportional,
integral and derivative functions are applied. Values from
×
0.1 to
×
1000.0.
Proportional
Sets the proportional gain. Values from 0.000 to 10,000.000. A value of 0.000 disables
proportional control.
Integral
Sets the integral gain. Values from 0.000 to 10,000.000. A value of 0.000 disables integral
control.
Derivative
Sets the derivative gain. Values from 0.000 to 10,000.000. A value of 0.000 disables
derivative control.
4.1.2.4.3
IWP Tab
Integral windup refers to the situation when the process variable spends a significant amount of time
away from the setpoint. During this time the integral term accumulates a significant error (referred to
as windup) and an overshoot occurs whilst the accumulated error is negated by errors in the opposite
direction (the error is unwound). To prevent this excessive overshoot integral windup protection (IWP)
limits the maximum windup, both positive and negative. Integral windup protection is only available if
the integral gain is greater than 0 (i.e., there is an integral part to the control).
Summary of Contents for HydroAct HA4
Page 1: ...HydroAct 4 User Manual Chemtrac Inc Firmware Version 1 19 November 15 2017...
Page 8: ......
Page 10: ......
Page 32: ......
Page 34: ......
Page 42: ...42 Chapter 3 Sensors For safety and correct operation the sensor must be properly earthed...
Page 74: ......
Page 92: ......
Page 93: ...III 6 Warranty 95 7 Returns 97 7 1 Contact Details Documentation...
Page 94: ......
Page 96: ......