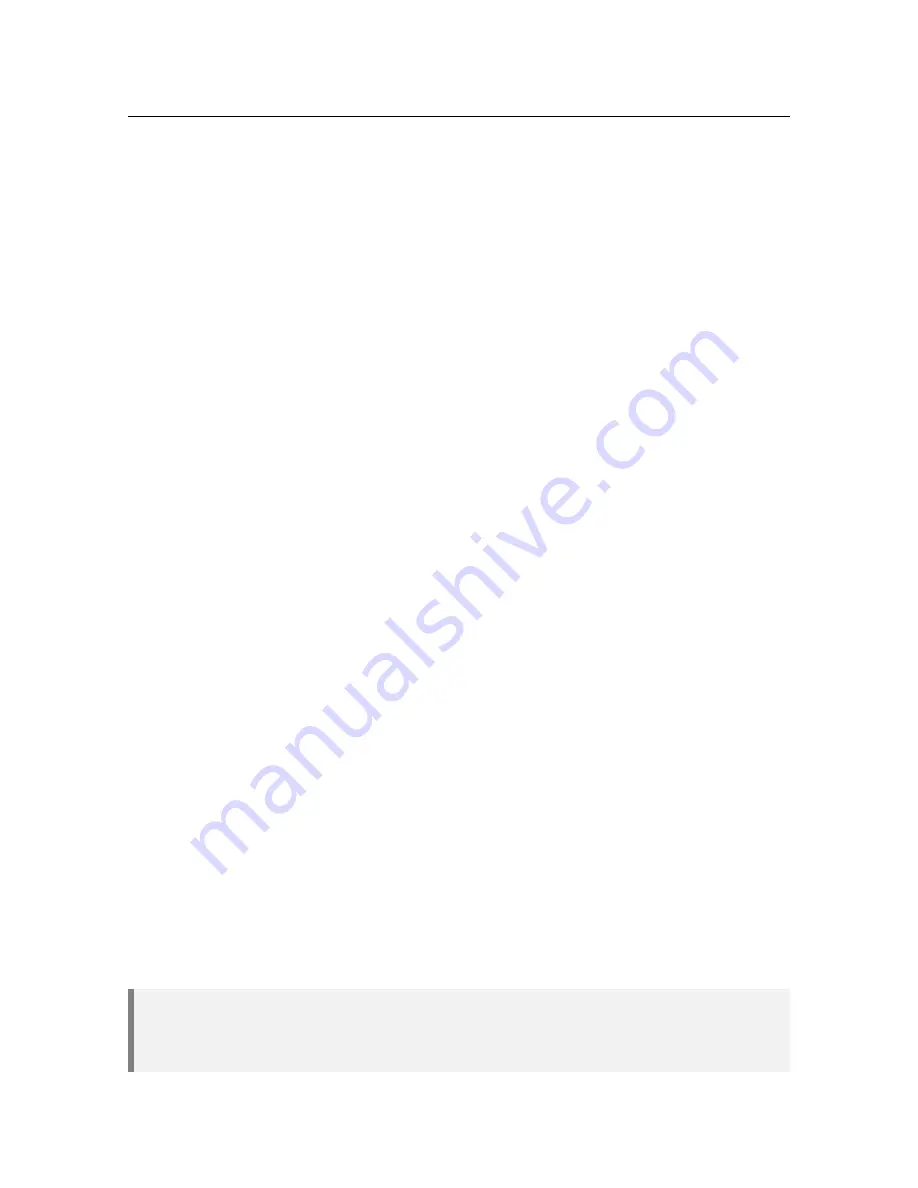
3.1 PC6 Particle Counter
43
3.1.4
Commissioning
3.1.4.1
Sample Considerations
The high sensitivity of the particle counter makes sample handling and delivery critical for proper
operation. Poor sample point selection and/or improper sample line installation can result in a
substantial loss of accuracy. It is important to ensure that the sample is properly representative of the
process stream. There are three common ways in which the sample can be distorted:
1. Adding particles to the sample stream. Choosing an improper location for the sample tap, such
as the bottom of a pipe where sediment can accumulate, or an open sample point where particles
can be introduced from outside the process usually causes this. Disturbances in sample flow to
the weir, or disturbing the sample tubing, will also cause particles to shed from the sample tubing
and result in large spikes in the reading which are not representative of the process. To minimize
this affect, keep sample tubing as short as possible, use smaller diameter tubing so flow velocity
is high (keeping tubing clean), and mount sample tubing away from locations where it is likely to
be disturbed.
2. Losing particles from the sample stream. Long sample lines can cause particle dropout, especially
at low flow rates. If the sample line must be long (more than 3m) then it will be important to keep
the sample flowing swiftly (i.e. 1.22m per second) to prevent particulate from settling out in the
tubing. The higher flow rate will also help keep the tubing cleaner and thereby help minimize
particle shedding which can be caused by fluctuations in flow.
3. Altering the particle distribution. Sample pumps can chop up larger particles creating more small
particles. “T” fittings can cause larger particles to miss the sample line because they can’t make
the sharp right angle “turn”. Having a sample tap that points into the sample stream is the most
ideal way to sample.
3.1.4.2
Initial Start Up
It is very important to flush out all taps and valves before connecting the PC6 Particle Counter.
Sometimes newly installed taps or valves, or those that haven’t been used for years, can contain debris
that may clog the sensor. Prior to connecting the sample line to the sensor, allow the sample to flow to
drain for at least 5 minutes.
Once installation is complete and the sample is hooked up to the sensor, the sample line may still
be somewhat dirty and not truly representative of the actual particle concentration at the sample point.
Typically the sample lines will sufficiently flush and stabilize within 15 to 30 minutes. If the particle
counter output is being recorded, it is easy to tell when the lines have been sufficiently flushed, as the
data will level out.
Once the counts have appeared to stabilize, a quick test can be done to verify the PC6 Particle
Counter sensor is not experiencing any sort of noise issue that can arise due to issues with poor
electrical grounding. Simply pinch the tubing coming off the top of the sensor (which is the tubing going
to the drain cup). Pinching this tubing will stop flow through the sensor. If the flow is stopped and the
tubing held stationary, the counts should drop to zero within 1 to 2 minutes providing the sample is
filter effluent (use DI water if filter effluent is not available or has a turbidity higher than 0.3 NTU).
With water flowing through the sensor, a check should be performed to make sure the PC6 Particle
Counter sensor does not have a cell condition alarm reporting on the HydroAct 4. If there is an alarm,
try cleaning the sensor as detailed in section 3.1.6.1. Contact your supplier for assistance if the cell
condition alarm does not clear after cleaning.
Both Laser and Cell condition are temperature dependent, so water and/or air temps near
freezing or above 35°C can cause these readings to change. The PC6 Particle Counter
sensor is working properly as long as the laser and cell condition reading are not in alarm
when water and air temps are in the 4 to 32°C range.
Summary of Contents for HydroAct 4
Page 1: ...HydroAct 4 User Manual Chemtrac Inc Firmware Version 1 19 November 15 2017...
Page 8: ......
Page 10: ......
Page 32: ......
Page 34: ......
Page 54: ......
Page 72: ......
Page 73: ...III 5 Warranty 75 6 Returns 77 6 1 Contact Details Documentation...
Page 74: ......
Page 76: ......