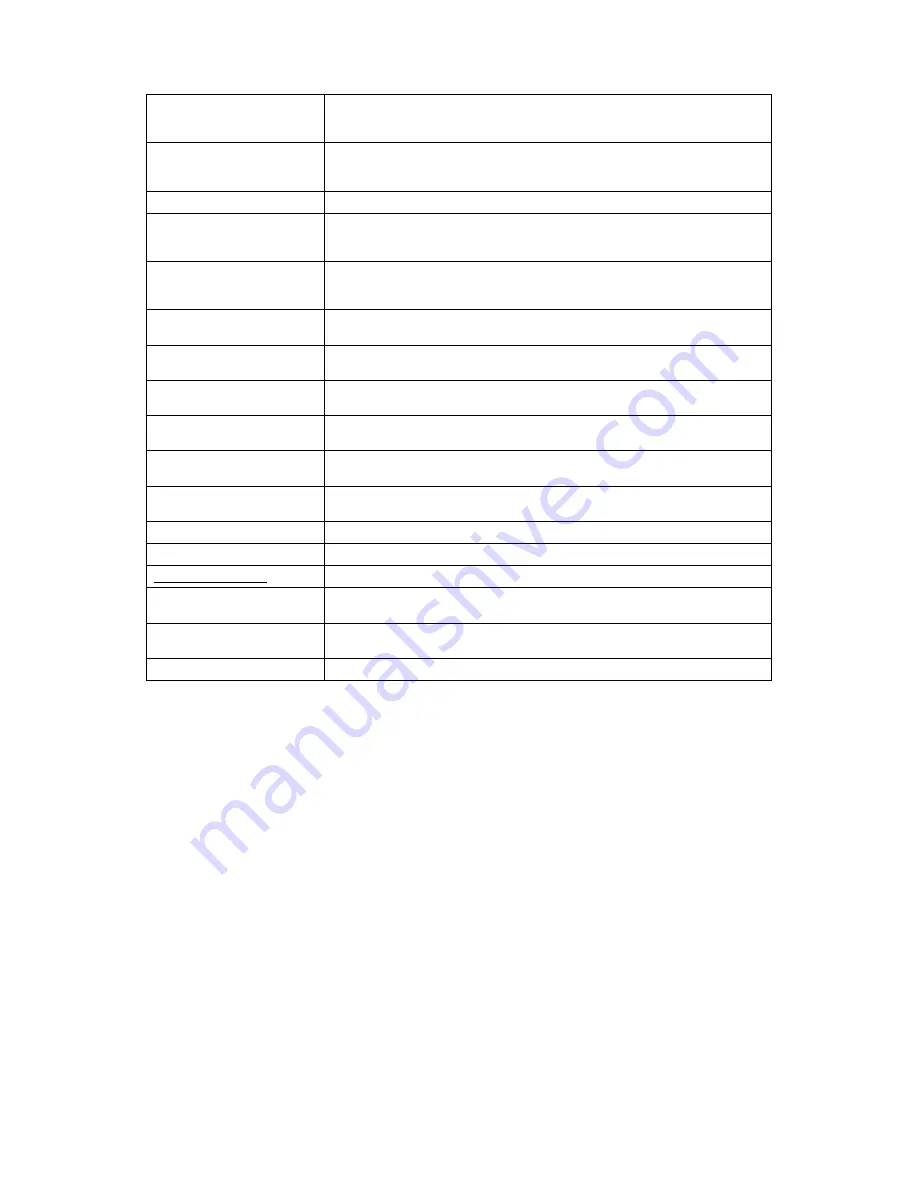
Page 18
'Channels' dropdown
The number of channels on the attached scanner should be chosen from the
'Channels' drop down. It is important that this number is correct when performing any
calibration or reading data from microDAQ.
'Full Scale' dropdown
This dropdown is the only means of selection of the scanner's full scale operating
pressure. The value affects the display of live engineering values and the generation
of calibration coefficients.
Scanner Type
Sets the type of scanner installed into the microDAQ (Conv, DTC, I-Daq, T-DAQ)
'Span High'
Sets the value of pressure for the 'high' point in the linear span and zero calibration.
Valid values range from 0.144PSI (3”WC) to 90PSI. Typically this value should be set
to 90% of the scanners full scale value, if possible.
‘Auto enable HW trigger on
startup’ dropdown
If set to anything other than Off, the microDAQ will immediately switch to hardware
trigger mode, waiting for the first trigger pulse, after initialisation. The dropdown
indicates the comms protocol used to send acquired data during triggering.
'Use DTC calibration if
available'
On powerup, uses the DTC scanners internal calibration coefficients to build the
microDAQ’s internal calibration data table.
If I-daq detected, use raw
calibration
If checked, this replaces the normal polynomial calibration function with a ‘raw’ linear
function whenever an I-daq is present in the microDAQ.
'Sensistor in circuit'
If checked, keeps the sensistor in circuit for a DTC scanner. In normal operation this
control should be left unchecked.
'All DTC Channels Active'
If checked, defaults microDAQ to setting the number of active channels to the number
read from the DTC scanner header
'Span Calibration to DTC Full
Scale'
If checked, defaults the span of the calibrated output to the full scale read from the
DTC scanner header.
'DTC gain = 1/3'
Selects the deranging function of the DTC scanner if the '3' option is selected,
otherwise defaults to the standard range of the scanner.
‘Scanner acquisition freq’
Selects the acquisition frequency of the scanner, either 20KHz or 50 KHz
‘Apply’
Applies the settings to the local settings memory
Calibration commands
Set span
Set the span of the linear calibration – confirms the value of pressure that has been
set up as the span value is being applied to the sensor.
Reset Linear cal
Resets the linear calibration to (+ 0) x1 ie no offset, unity gain. Applies ONLY to the
current linear calibration, ie the DTC calibration if using a DTC scanner.
Rebuld
Force a calibration table rebuild.
Table 5.10, Miscellaneous group settings