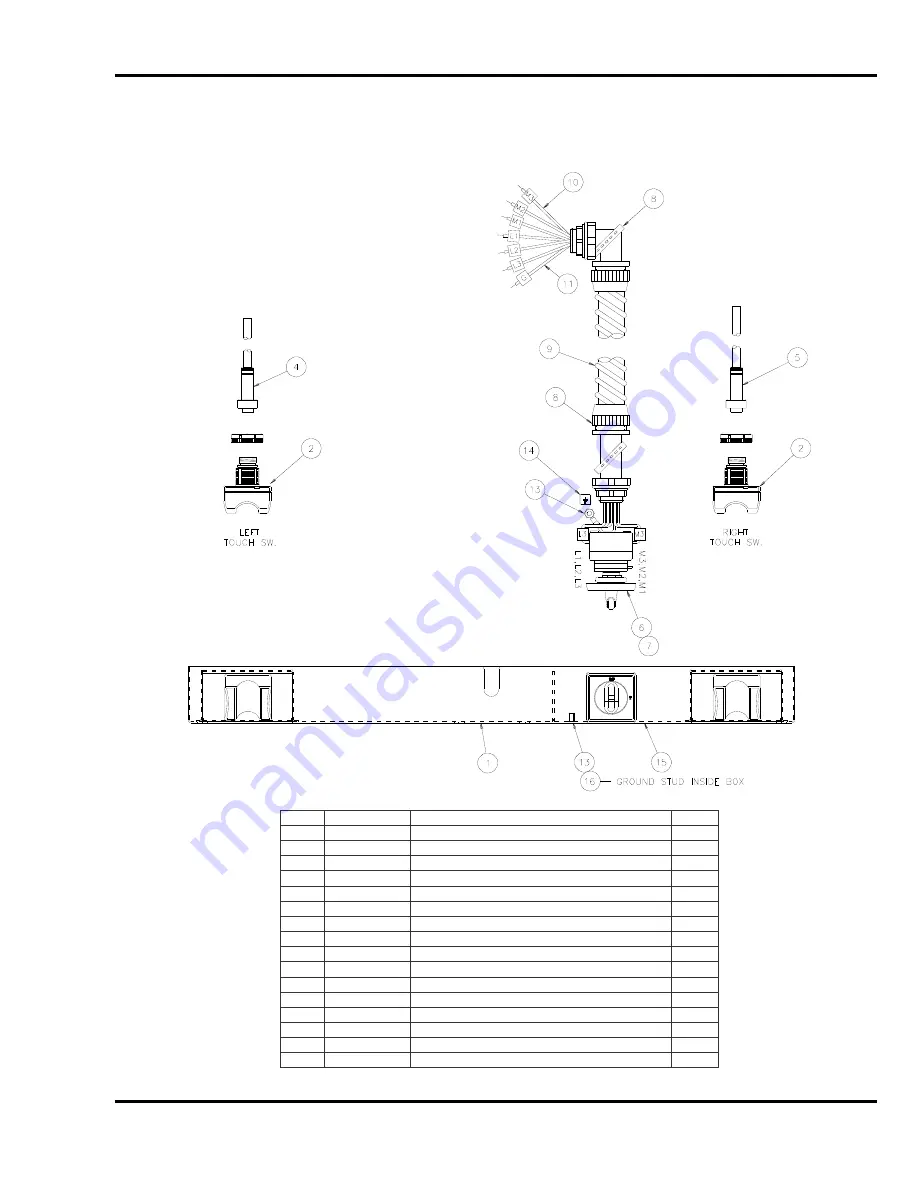
15.0 Schematics & Parts Lists
97
15.21 Cut Button Assembly – ErgoTouch
EE-3382-1 Sheet 1, Rev. A
NO. PART
NO. DESCRIPTION
OF
ACCESSORIES
QTY
1 47665
CONTROL
BOX
ASSEMBLY
1
2
E-3347
SWITCH - ERGO TOUCH
2
3
EE-3350-2
CONTROLLER - ASM. - TOUCH SWITCH
1
4
EE-3348-2
CABLE ASM. - TOUCH SWITCH, LH
1
5
EE-3349-2
CABLE ASM. - TOUCH SWITCH, RH
1
6
E-3083
SWITCH FACE - MAIN DISCONNECT
1
7
E-3082
SWITCH - MAIN DISCONNECT (BODY)
1
8
E-2190-2
3/4" CONDUIT CONNECTOR - 90%%d
2
9
E-2189-2
CONDUIT - PLASTIC, 16" LONG
1
10
E-1213-B
WIRE - #10 GA. BLACK MTW 38" LONG
6
11
E-2743-1
WIRE - #14 GA. GRN/YEL TEW 38" LONG
1
12
E-1214-64
CONNECTOR - 1/4" RING (16-14GA)
1
13
H-6423-4
NUT - 1/4-20 HEX
1
14
S-1781-42
LABEL - GROUND SYMBOL, SECONDARY
1
15
S-1781-11
LABEL - ELECTRIC SHOCK
1
16
H-6910-404
SCREW - 1/4-20 X 1/2" BUT HD CAP
1
Summary of Contents for CHAMPION 305 TC
Page 10: ...5 0 Footprint 10 5 0 Footprint...
Page 24: ...8 0 Knife Installation Changing 24 NOTES...
Page 57: ...14 0 Troubleshooting 57 NOTES...
Page 60: ...15 0 Schematics Parts Lists 60 15 2 Main Assembly Hydraulics 47900 Sheet 2...
Page 62: ...15 0 Schematics Parts Lists 62 15 3 Main Assembly Clamp 47900 Sheet 3...
Page 64: ...15 0 Schematics Parts Lists 64 15 4 Main Assembly Final Wiring 47900 Sheet 4...
Page 68: ...15 0 Schematics Parts Lists 68 15 6 Main Assembly Electrical Components Upper 47900 Sheet 6...
Page 70: ...15 0 Schematics Parts Lists 70 15 7 Main Assembly Air Table 47900 Sheet 7...
Page 72: ...15 0 Schematics Parts Lists 72 15 8 Main Assembly Table Mounting 47900 Sheet 8...
Page 76: ...15 0 Schematics Parts Lists 76 15 10 Main Assembly Knife 47900 Sheet 11...
Page 78: ...15 0 Schematics Parts Lists 78 15 11 Main Assembly Covers and Labels 47900 Sheet 12...
Page 80: ...15 0 Schematics Parts Lists 80 15 12 Main Assembly Table Extensions 47900 Sheet 13...
Page 82: ...15 0 Schematics Parts Lists 82 15 13 Power Panel Assembly EE 3461 Sheet 1 Rev D...
Page 85: ...15 0 Schematics Parts Lists 85 Power Panel Assembly EE 3461 Sheet 2 Rev D...
Page 86: ...15 0 Schematics Parts Lists 86 15 14 Basic Machine Schematic E 3462 Rev C...
Page 87: ...15 0 Schematics Parts Lists 87 15 15 Interconnection Diagram E 3463 Rev A...
Page 92: ...15 0 Schematics Parts Lists 92 15 17 Hydraulic Schematic H 468 3 Rev B...
Page 95: ...15 0 Schematics Parts Lists 95 EE 3339 Sheet 2 Rev F...
Page 98: ...15 0 Schematics Parts Lists 98 EE 3382 1 Sheet 2 Rev A...
Page 102: ...15 0 Schematics Parts Lists 102 15 25 Air Table Blower Assembly 47578 Rev C...
Page 104: ...15 0 Schematics Parts Lists 104 15 27 Power Panel Connection Procedure Label S 1781 211 Rev A...
Page 105: ...15 0 Schematics Parts Lists 105 15 28 Warning Label S 1781 16 Rev D...
Page 108: ...15 0 Schematics Parts Lists 108 NOTES...
Page 110: ...F 254 J May 2014...