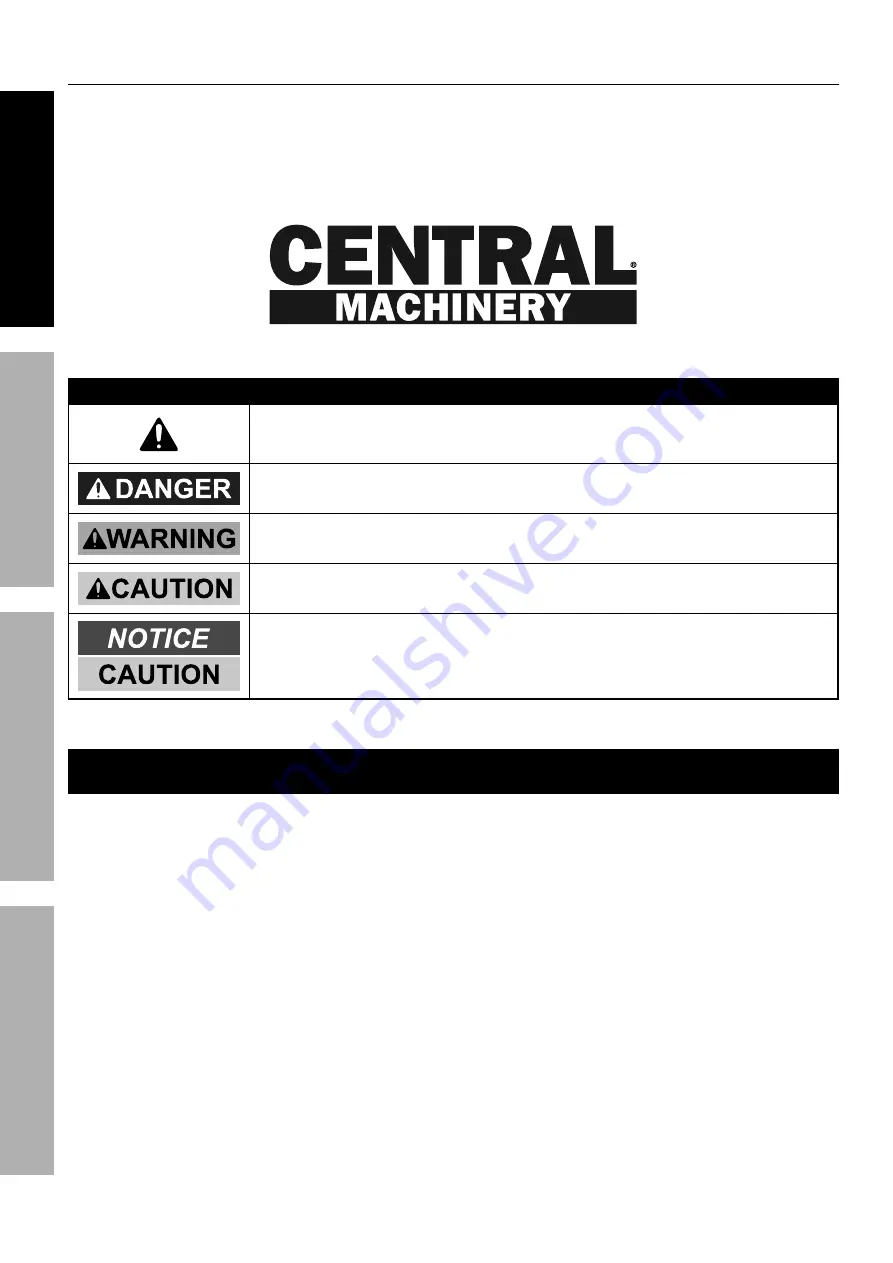
Page 2
For technical questions, please call 1-888-866-5797.
Item 33497
SA
FETY
OPERA
TI
O
N
MAINTENANCE
SETUP
Table of Contents
Safety ........................................................................2
Specifications ............................................................4
Setup .........................................................................4
Operation ...................................................................8
Maintenance ..............................................................9
Parts List and Diagram .............................................10
Warranty ...................................................................12
WARNING SYMBOLS AND DEFINITIONS
This is the safety alert symbol. It is used to alert you to potential
personal injury hazards. Obey all safety messages that
follow this symbol to avoid possible injury or death.
Indicates a hazardous situation which, if not avoided,
will result in death or serious injury.
Indicates a hazardous situation which, if not avoided,
could result in death or serious injury.
Indicates a hazardous situation which, if not avoided,
could result in minor or moderate injury.
Addresses practices not related to personal injury.
IMPORTANT SAFETY INFORMATION
WARNING Read all safety warnings and instructions.
Failure to heed these markings may result in
personal injury and/or property damage.
Save all warnings and instructions for future reference.
The warnings, precautions, and instructions discussed in this manual cannot cover all possible
conditions and situations that may occur. The operator must understand that common sense and
caution are factors, which cannot be built into this product, but must be supplied by the operator.
1. Keep hands away from arbor plates
and press pin during use.
2. Do not move workpiece while compressed.
3. Release load before service or maintenance.
4. Bolt to floor before use.
5. Keep area under arbor plates clear. If arbor
plates rest on obstruction (i.e. bolt, debris,
etc.), it creates an uneven press, causing
excess stress and possible breakage.
6. Avoid off-center loads. Do not operate if
workpiece tilts or binds during compression.
7. STOP and release compression if you suspect
imminent structural failure. If safe, inspect
thoroughly and reposition before proceeding.
8. Do not compress springs or other elastic
objects. They could disengage hazardously.
9. Wear ANSI-approved safety goggles,
heavy-duty work gloves, and steel-toe
work boots during set up and/or use.
10. Keep bystanders out of work area.