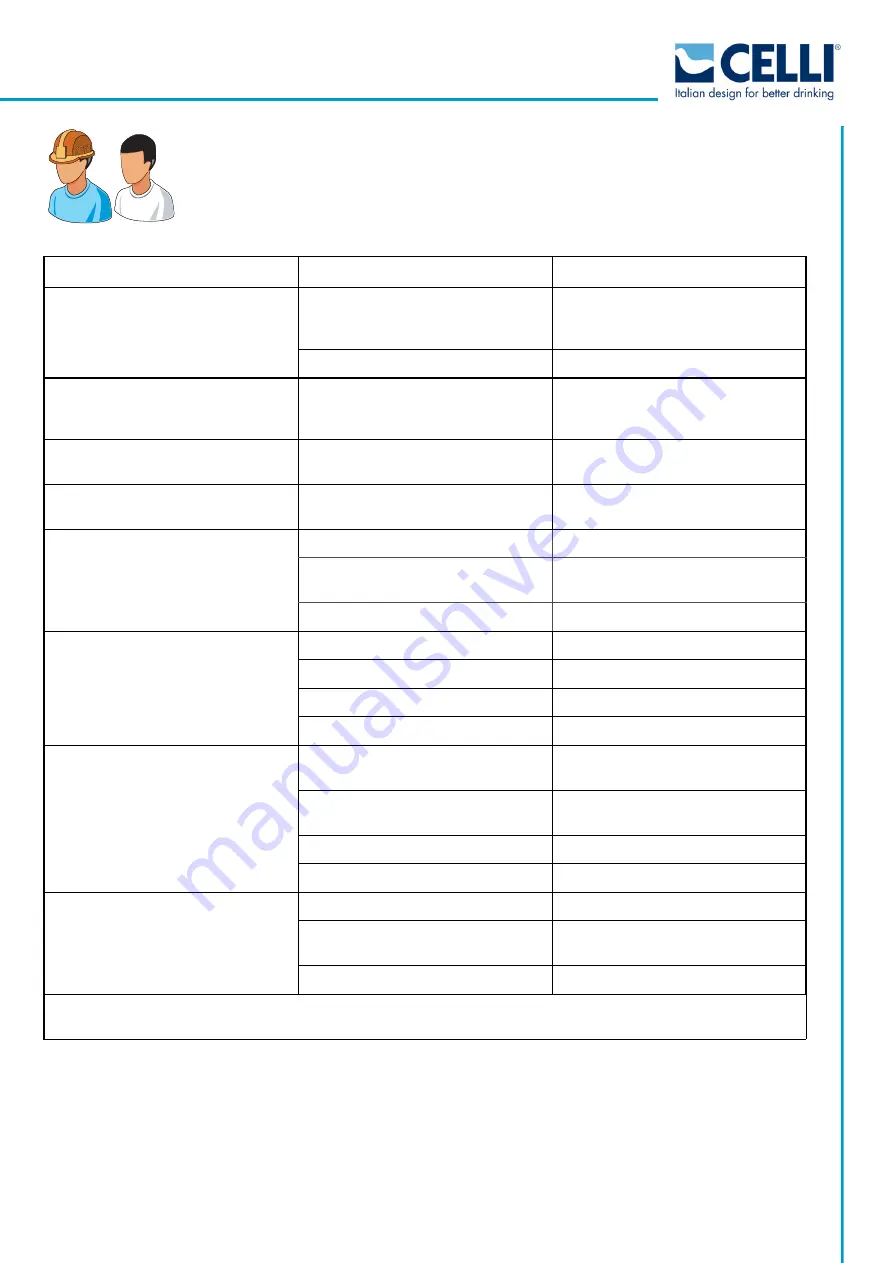
Troubleshooting
53
Brave 30 ES- Brave 60 ES - Brave 90 ES
7 - Troubleshooting
PROBLEM
PROBABLE CAUSE
REMEDIES
The dispenser does not start up
Power supply failure
Check that power is present.
If the power is OK, call an authorised
technician.
Thermostat failure
Call an authorised technician
The cooling unit operates
continually, and the water
delivered is warm
Refrigerant gas leak
Call an authorised technician
The cooling unit operates
continually, and the water freezes
Thermostat failure
Call an authorised technician
Noisy water pump
Water supply failure
Check that water is reaching the
appliance
The dispenser does not deliver
water
Main water tap turned off
Turn on the water tap
Water supply connection tube crushed
or obstructed
Inspect the path of the tube
No electricity supply
Check the plug is well inserted
The dispenser does not deliver
sparkling water
CO
2
cylinder has run out
Replace the CO
2
cylinder
Electronic control unit malfunction
Call an authorised technician
Pump failure
Call an authorised technician
CO
2
cylinder shut off
Open the CO
2
cylinder valve
The dispensed product is not cold
enough
The ice bank has run out
Wait until the ice bank has fully
reformed
The water entering the machine is too
hot
Check the incoming water temperature
is lower than 32°C
Soda recirculation pump malfunction
Call an authorised technician
Inadequate insulation on the python
Call an authorised technician
Only water is dispensed
The syrups have run out
Replace the syrup tanks with new ones
The syrup lines are obstructed
Sanitise the syrup lines, as indicated in
the relevant paragraph
No CO
2
Replace the CO
2
cylinder
FOR ANY OTHER PROBLEMS NOT COVERED HERE,
CONTACT THE SERVICE CENTRE