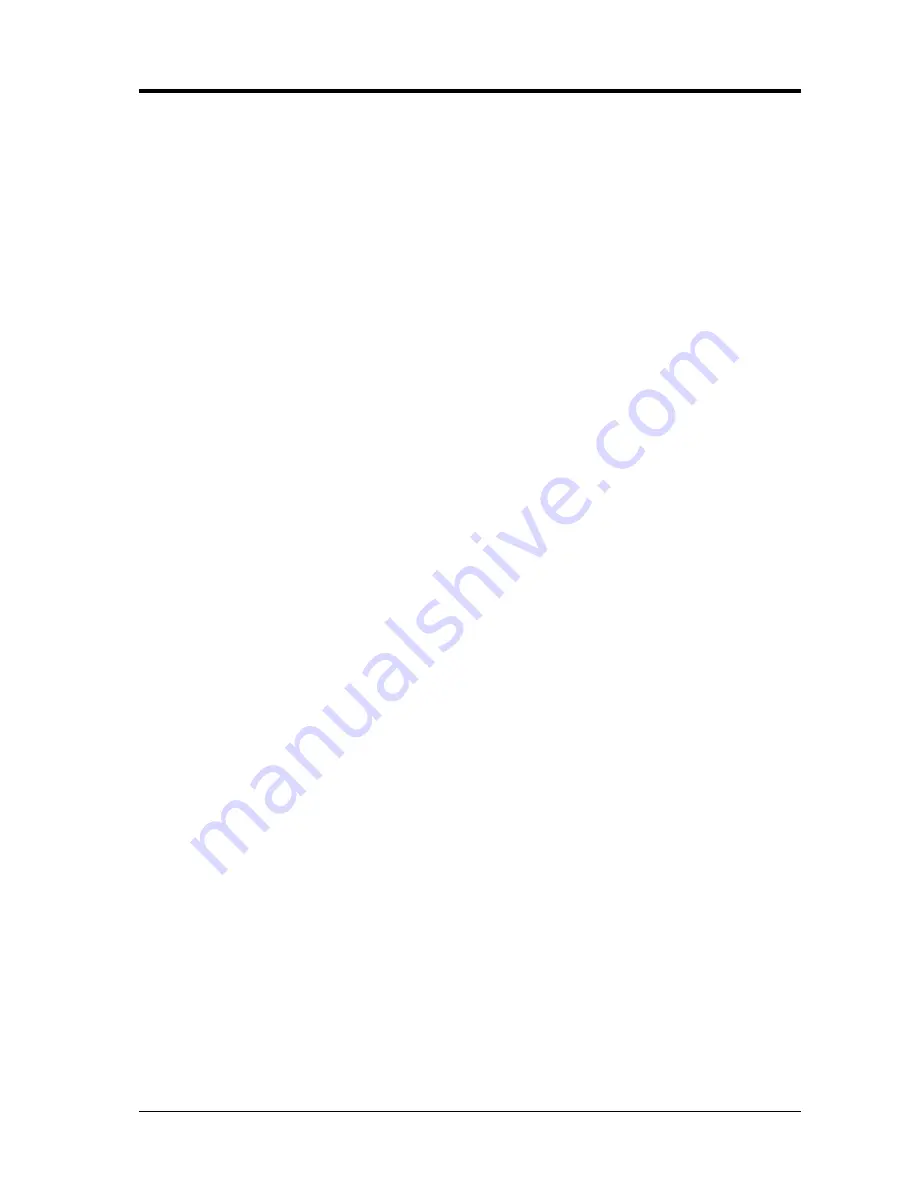
CEBORA S.p.A.
7
The terminal J5 of the pilot arc board (58) also corresponds to the positive output (3) of the
igbt module. This is connected to the nozzle resistor (17), which facilitates switching from pilot
arc to transfer arc, and the nozzle potential output ready for connection to the Unit HV18. This
connection, inside the pilot arc board (58), also leads to the Hall-effect current transducer, which
sends the pilot arc current signal to the settings board (54).
The settings board (54) constitutes the actual current regulator for the system.
It generates the igbt drive signal, calculating the waveform (duty cycle) by comparing the
current reference signal from the control board (38) to the current feed-back signal from the
current transducers on the pilot arc board (58).
The signals of the two current transducers are also used for switching between pilot arc and
transfer arc. Specifically:
-
when the Power Source output current (signal of the transducer on TP3) is equal to the pilot
arc current (signal of the transducer on J5), the control activates operation in pilot arc mode.
-
when the Power Source output current (signal of the transducer on TP3) is greater than the
pilot arc current (signal of the transducer on J5), the control activates operation in transfer arc
(cutting) mode.
This check is carried out by the control board (38), which analyzes the signals of the two
current transducers appropriately handled by the settings board (54).
The connector (3) on the rear panel is ready to connect the Power Source to the Gas Console.
It contains the supply voltages (24 Vac and 27 Vac) for the Gas Console and the CAN bus
communication line for the exchange of information between the MASTER processor on the
Power Source and the SLAVE processor on the Gas Console. The two supply voltages, 24 Vac
and 27 Vac, of the Gas Console are generated by the service transformer (56), powered by the
same voltage that powers the service transformer (50).
The connector (4) on the rear panel is ready to connect the Power Source to the system
(pantograph or robot). It contains all of the signals necessary for the cutting system to dialogue
with the plant.
These signals include:
-
emergency stop (signal from the system to the Power Source);
-
start Power Source (signal from the system to the Power Source);
-
operating permission (pantograph or robot connected);
-
arc voltage (signal from the Power Source to the system);
-
arc lit (signal from the Power Source to the system).
The remote board (59) acts as an interface between the control board (38) of the Power
Source and the system, and connects and affects all of the signals present on the connector (4).
The fuse board (50) contains the fuses for the following circuits:
-
power supplies to the electronic boards;
-
power supply to the DC-capacitors pre-charge circuit on pilot arc board (58);
-
power supply of the line contactor (44).
The pre-charge board (45), controlled by the control board (38) acts:
-
the pre-charge of DC-capacitors on pilot arc board (58); during this phase the voltage reached
by the capacitors is checked, and the corresponding signal is sent to the control board (38);
-
pre-magnetization of the power transformer (27), through the resistors R16, R17, R18 and
relay RL3, present on the pre-charge board (45);
-
power supply of the cooling unit pump (13) through the relay RL1.
The control board (38) contains the main microprocessor of the Power Source (MASTER).
It supervises management of the other boards, more specialized in their respective functions,
controls the line contactor (44), processes the reference signal of the cutting current to be sent to
the settings board (54), communicates with the microprocessor of the panel board on the Gas
Console (SLAVE) to manage the solenoid valves of the gas circuits, and makes sure that proper
operating conditions are always present.
3.302.218
9/8/2006