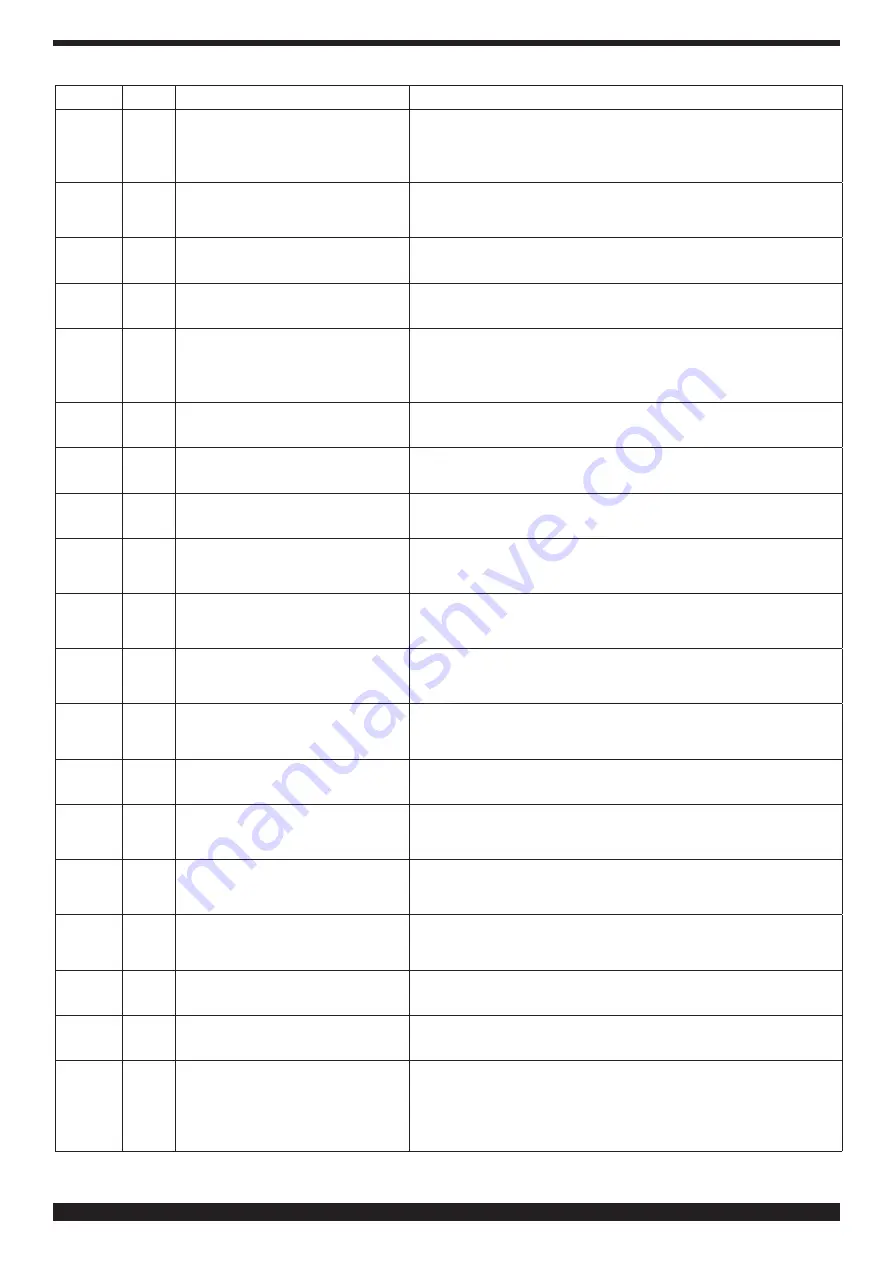
108/109
3301065/A
Code
Type
Error Description
Action
42
[E]
Motor speed out of control.
Check there are no mechanical blockages in the wire feeder
rollers. If the motor turns at an uncontrollable speed, check the
wiring in the wire feeder and ensure the motor feed polarity is
correct. If the error persists, contact technical assistance.
47
[E]
Low motor supply voltage error.
Check connection between power source and wire feeder.
Switch the power source on and off. If the error persists, con-
tact technical assistance.
54
[E]
Current not zero when power
source tested
Switch the power source on and off. If the error persists, con-
tact technical assistance.
56
[E]
Excessive duration of short-cir-
cuit at output
Switch the power source on and off. If the error persists, con-
tact technical assistance.
57
[E]
Excessive current on wire feeder
motor
Check there are no mechanical blockages in the wire feeder
rollers.
Switch the power source on and off. If the error persists, con-
tact technical assistance.
58
[E]
Firmware upgrade error
Contact technical assistance Or impose firmware update by
turning DIP3 on the master panel board ON.
60
[E]
Average current above maximum
limit for too long
Switch the power source on and off. If the error persists, con-
tact technical assistance.
63
[E]
Incorrect mains voltage (no pha-
se)
Check that the mains plug phases are properly connected.
If the error persists, contact technical assistance.
72
[W]
Thermal protection triggered due
to excessive temperature in SRS
kit, Item No 443.
Wait until the machine cools down. Check that the air intake
and outlet grilles are not blocked. If the problem persists, con-
tact technical assistance.
73
[W]
Thermal protection triggered due
to excessive temperature in ou-
tput diode unit.
Wait until the machine cools down. Check that the air intake
and outlet grilles are not blocked. If the problem persists, con-
tact technical assistance.
74
[W]
Thermal protection triggered due
to excessive temperature in IGBT
assembly.
Wait until the machine cools down. Check that the air intake
and outlet grilles are not blocked. If the problem persists, con-
tact technical assistance.
75
[W]
Coolant pressure too low.
Check the coolant level. Check the centrifugal pump turns
correctly. If it does not turn correctly, release using a release
screw. If the problem persists, contact technical assistance.
76
[W]
Cooling unit not connected
Check the pressure switch connection is intact. If the problem
persists, contact technical assistance.
78
[W]
Combined with Item No 102 indi-
cates that shielding gas pressure
is low.
Check the pressure entering the solenoid valve. It must be gre-
ater than the threshold set in the relevant gas console parame-
ter. If the problem persists, contact technical assistance.
79
[W]
Combined with Item No 102 indi-
cates that shielding gas pressure
is high.
Check the pressure entering the solenoid valve. If the problem
persists, contact technical assistance.
81
[E]
Gas kit not present in combina-
tion with Kit Item No 436.
Make sure that gas Kit Item 436 is correctly connected. Switch
the power source on and off. If the problem persists, contact
technical assistance.
84
[W]
Quality control option error
Check the parameters set are correct.
85
[W]
Error during USB firmware upda
-
ting
Switch the power source on and off. If the error persists, con-
tact technical assistance.
87
[E]
Gas flow sensor error
Check there are no obstructions in the shielding gas pipes. Test
the channel using the appropriate test command. Check the
cylinder inlet pressure, because the desired flow cannot be re
-
gulated if it is too low. If the problem persists, contact technical
assistance.