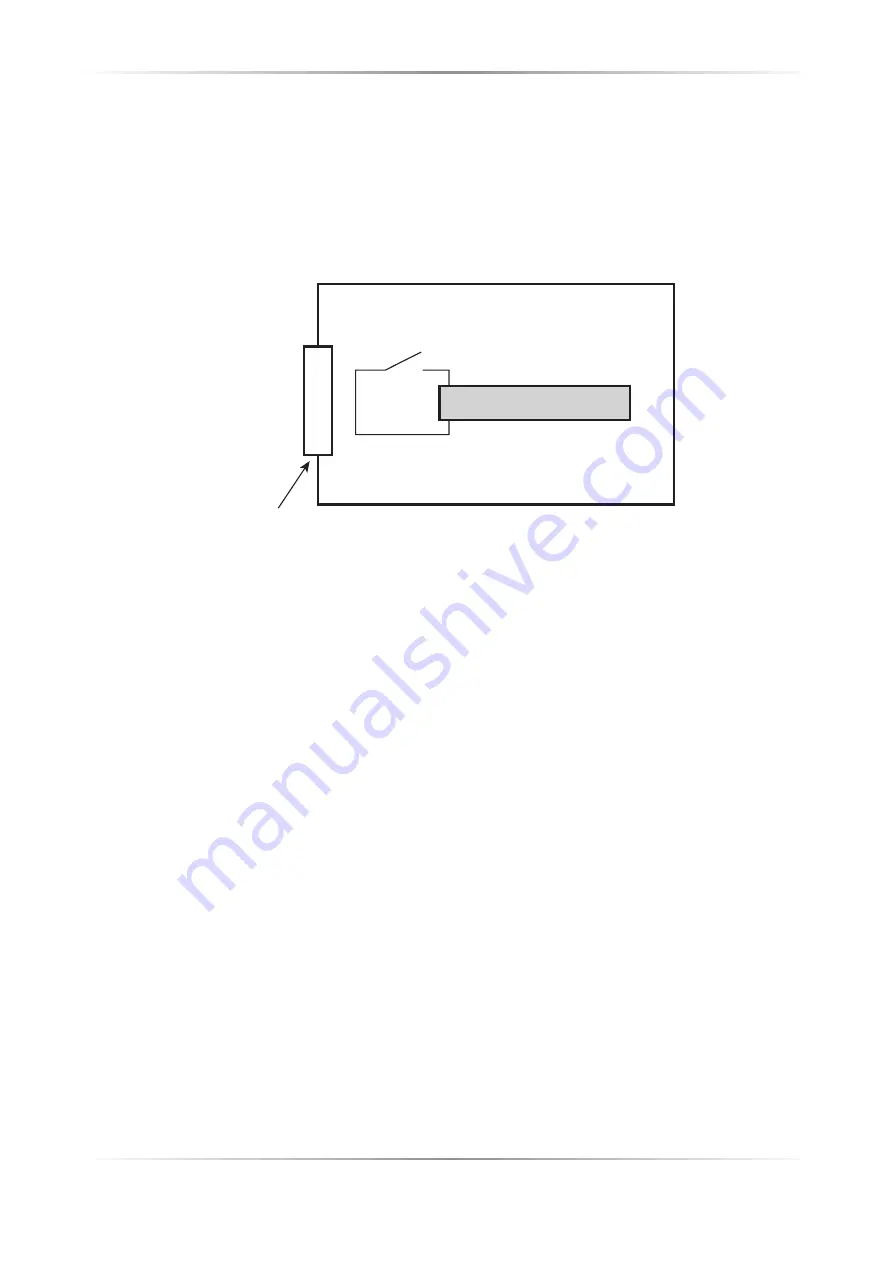
74
REVO C
3PH from 1100A to 2100A
User’s manual
13.4 Using FieldBus only
The static unit as an option can be ordered with a FieldBus (Ex: profinet).
This option continuously writes the values on the unit keeping them up to date.
Using the field bus it is possible to change the status of the Sw
S
contact with bit 2 of the “Command table” (See
the communication manual of the respective FieldBus).
NOTE:
The parameters written are:
• command table
• reference
• rescaling
if the FieldBus is active but disconnected these values will be forced to 0.
Sw
S
= Switch software
Sw
s
DI
Software switch
from communication
DI Function Configurated like “Not Used” or different from “Enable”
Instrument Enable
Summary of Contents for REVO C 3PH 1100A
Page 2: ......