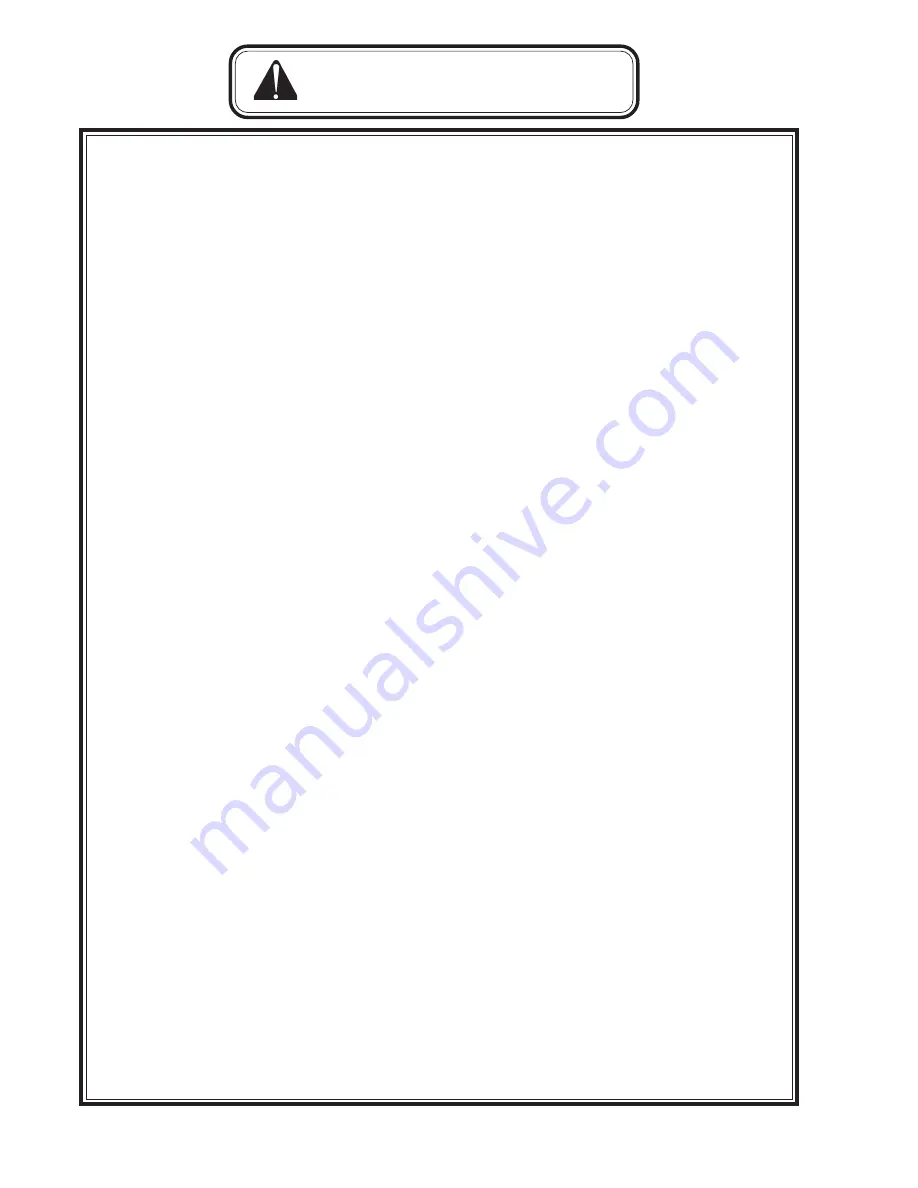
SAFETY PRECAUTIONS
SR2-1-6
15501 9-35990
use appropriate aligning tools.
Remove all sharp edges and burrs from re-worked
parts.
Use only approved and effectively grounded auxiliary
power sources for heaters, battery chargers, pumps
and similar equipment to reduce electrical shock
hazard.
Lift and handle heavy components using hoisting
devices of appropriate capacity. Ensure the parts are
supported by appropriate straps and hooks.
Use lifting eyes provided to this aim.
Pay attention to bystanders near the lifting area.
N e v e r p o u r g a s o l i n e o r d i e s e l f u e l i n t o o p e n
containers. Never use gasoline, solvents or other
flammable fluids to clean parts. Use proprietary
certified non-flammable, non-toxic solvents only.
When using compressed air to clean parts, wear
safety glasses with side shields. Limit pressure to
max. 2 bar, in accordance with local and national
safety regulations in force.
D o n o t r u n t h e e n g i n e o f t h i s m a c h i n e i n c l o s e d
buildings without proper forced ventilation capable to
remove toxic exhaust gases concentrating in the air.
D o n o t s m o k e , n o r a l l o w o p e n f l a m e s o r s p a r k s
nearby while refuelling the unit or handling highly
flammable materials.
Do not use open flames as light sources to look for
leaks or inspect anywhere on the machine.
Make sure that all mechanical tools provided are in
good condition at all times. Never use tools with
mushroomed or damaged heads. Always wear eye
protections with side shields.
Move with extreme care when working under, on or
near the machine or its attachments.
In case of attachment tests during which the engine
should be kept running, a qualified operator must sit
in the driver’s seat at all times while the mechanic is
at work.
Keep hands and clothes far OFF moving parts.
Stop the engine and move the safey lever to the lock
position before starting adjusting or repairing an
assembly.
Do not carry out any work on the attachment without
p r i o r a u t h o r i s a t i o n . O b s e r v e r e c o m m e n d e d
maintenance and repair procedures.
In case of field service, move the machine to level
ground and block it. If work on an incline cannot be
a v o i d e d , s e c u r e l y b l o c k t h e m a c h i n e a n d i t s
attachments. Move the machine to level ground as
soon as possible. Do not twist chains and cables.
N e v e r u s e a t w i s t e d c h a i n o r c a b l e f o r l i f t i n g o r
pulling. Always wear safety gloves to handle chains or
cables.
Be sure chains and cables are firmly fastened and
that the anchor point is strong enough to withstand
the expected load. Keep all bystanders clear of the
anchor point, cables or chains.
Do not pull or tow
u n l e s s t h e o p e r a t o r ’ s c o m p a r t m e n t s o f t h e
machines involved are fitted with proper guards
against cable or chain backlash.
Keep the maintenance area clean and dry at all times.
Clean immediately all water and oil spillage.
Do not pile up oily or greasy rags as they represent a
major fire hazard. Always store them in closed metal
containers.
Before starting the machine or its attachment, check,
adjust and lock the operator’s seat. Also ensure that
nobody is within the machine or attachment operating
range before starting or operating the machine and/or
its attachments. Sound the horn.
Rust inhibitors are volatile and flammable. Prepare
parts in well ventilated areas. Keep open flames
away.
Do not smoke.
Store containers in a cool well
ventilated place where they could not be reached by
unauthorised people.
Do not carry loose objects in your pockets that might
fall unnoticed into open compartments.
Wear appropriate safety clothing such as hard hat,
s a f e t y s h o e s a n d g l o v e s , s a f e t y g l a s s e s w h e n
splinters or other particles may be ejected.
Wear the appropriate welder’s equipment such as
dark safety glasses or mask, hard hat, protective
clothing, safety gloves and footwear always while
welding or arc-cutting. Wear dark safety glasses when
you are near a welding in progress.
Do not look the
welding arc without proper eye protection.
Become acquainted with all your jacking equipment
and their capacity. Ensure that the jacking point on
the machine is appropriate for the load applied. Also,
be sure the supports under the jack and between the
jack and the machine are appropriate and stable.
Any equipment supported by a jack represents a
p o s s i b l e h a z a r d . A l w a y s s u p p o r t t h e l o a d o n t o
appropriate blocking means as a safety measure
before proceeding with service or maintenance work,
in compliance with local or national safety regulations.
Metal cables produce steel splinters. Always wear
certified protection clothes such as safety gloves and
glasses while handling them.
Handle all parts carefully. Keep hands and fingers
away from gaps, gears, and similar. Always use and
wear certified safety clothes such as safety glasses,
gloves and footwear.
The attachment is kept constantly in position by an oil
column trapped into the high pressure circuit. Lower
the attachment to the ground and relieve pressure
from all circuits prior to carrying out any type of
maintenance or repair work.
Do not service or repair the machine if it is parked
downhill. Consult the Operator's Manual for correct
maintenance procedure.
A r e a s n e a r a r t i c u l a t e d c u t t i n g e d g e s w h e r e
mechanical parts are in motion are where personal
injuries are most likely to occur. Pay attention to
prevent possible part movements by means of blocks
or by keeping clear of such zones when motion may
Summary of Contents for WX90
Page 1: ...Excavator WX90 Service Manual Cre 9 35990...
Page 6: ...15501 9 35990 Find manuals at http best manuals com search s CASE 935990...
Page 14: ...HU1 3 4 FEATURES OF THE MANUAL WX90 15501 9 35990 NOTES...
Page 16: ...15501 9 35990...
Page 51: ...This as a preview PDF file from best manuals com Download full PDF manual at best manuals com...