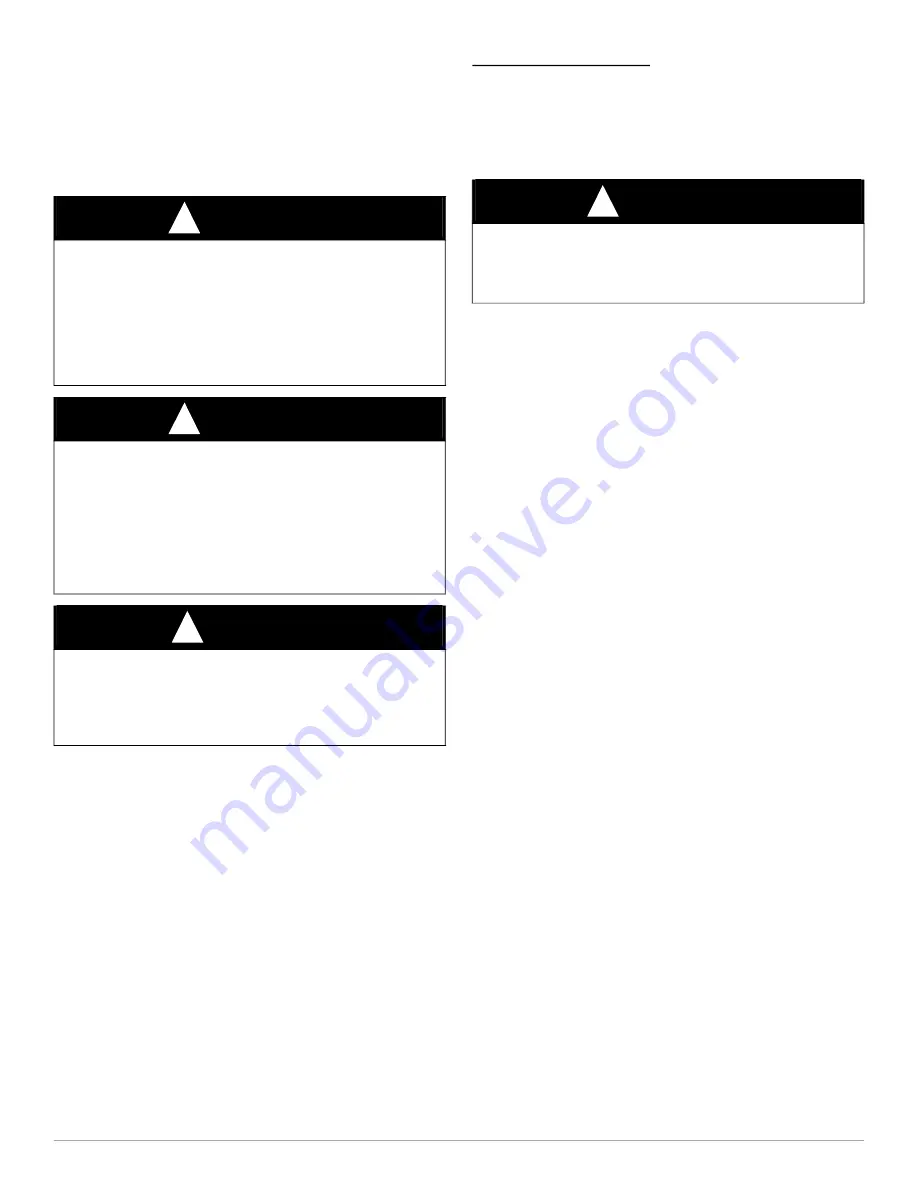
PHD4 Series K and WPH4 Series K: Installation Instruction
Manufacturer reserves the right to change, at any time, specifications and designs without notice and without obligations.
27
Maintenance
To ensure continuing high performance, and to minimize the possibility
of premature equipment failure, periodic maintenance must be
performed on this equipment. This heat pump unit should be inspected at
least once each year by a qualified service person. To troubleshoot unit,
.
NOTE:
TO EQUIPMENT OWNER: Consult your local dealer about the
availability of a maintenance contract.
The minimum maintenance requirements for this equipment are as
follows:
1. Inspect air filter(s) each month. Clean or replace when necessary.
2. Inspect indoor coil, drain pan, and condensate drain each cooling
season for cleanliness. Clean when necessary.
3. Inspect blower motor and wheel for cleanliness each cooling
season. Clean when necessary.
4. Check electrical connections for tightness and controls for proper
operation each cooling season. Service when necessary.
Step 1 – Air Filter
IMPORTANT:
Never operate the unit without a suitable air filter in the
return-air duct system. Always replace the filter with the same
dimensional size and type as originally installed. See
recommended filter sizes.
Inspect air filter(s) at least once each month and replace
(throwaway-type) or clean (cleanable-type) at least twice during each
cooling season and twice during the heating season, or whenever the
filter becomes clogged with dust and lint.
Indoor Blower and Motor
NOTE:
All motors are pre-lubricated. Do not attempt to lubricate these
motors.
NOTE:
460 volt units have a stepdown autotransformer that supplies
approximately 230 volts to a nominal 230 volt indoor blower motor.
For longer life, operating economy, and continuing efficiency, clean
accumulated dirt and grease from the blower wheel and motor annually.
To clean the blower motor and wheel:
1. Remove and disassemble blower assembly as follows:
a. Remove blower access panel (see
).
b. Disconnect 5 pin plug and 4 pin plug from indoor blower motor.
Remove capacitor if required.
c. On all units remove blower assembly from unit. Remove screws
securing blower to blower partition and slide assembly out. Be
careful not to tear insulation in blower compartment.
d. Ensure proper reassembly by marking blower wheel and motor in
relation to blower housing before disassembly.
e. Loosen setscrew(s) that secures wheel to motor shaft, remove
screws that secure motor mount brackets to housing, and slide
motor and motor mount out of housing.
2. Remove and clean blower wheel as follows:
a. Ensure proper reassembly by marking wheel orientation.
b. Lift wheel from housing. When handling and/or cleaning blower
wheel, be sure not to disturb balance weights (clips) on blower
wheel vanes.
c. Remove caked-on dirt from wheel and housing with a brush.
Remove lint and/or dirt accumulations from wheel and housing
with vacuum cleaner, using soft brush attachment. Remove
grease and oil with mild solvent.
d. Reassemble wheel into housing.
e. Reassemble motor into housing. Be sure setscrews are tightened
on motor shaft flats and not on round part of shaft. Reinstall
blower into unit. Reinstall capacitor.
f. Connect 5 pin plug and 4 pin plug to indoor blower motor.
g. Reinstall blower access panel (see
).
3. Restore electrical power to unit. Start unit and check for proper
blower rotation and motor speeds during cooling cycles.
WARNING
!
PERSONAL INJURY AND UNIT DAMAGE HAZARD
Failure to follow this warning could result in personal injury or death
and unit component damage.
The ability to properly perform maintenance on this equipment requires
certain expertise, mechanical skills, tools and equipment. If you do not
possess these, do not attempt to perform any maintenance on this
equipment, other than those procedures recommended in the Owner’s
Manual.
WARNING
!
ELECTRICAL SHOCK HAZARD
Failure to follow these warnings could result in personal injury or
death:
1. Turn off electrical power to the unit and install a lockout tag
before performing any maintenance or service on this unit.
2. Use extreme caution when removing panels and parts.
3. Never place anything combustible either on or in contact with the
unit.
CAUTION
!
UNIT OPERATION HAZARD
Failure to follow this caution may result in improper operation.
Errors made when reconnecting wires may cause improper and
dangerous operation. Label all wires prior to disconnecting when
servicing.
WARNING
!
ELECTRICAL SHOCK HAZARD
Failure to follow this warning could result in personal injury or death.
Disconnect and tag electrical power to the unit before cleaning the
blower motor and wheel.