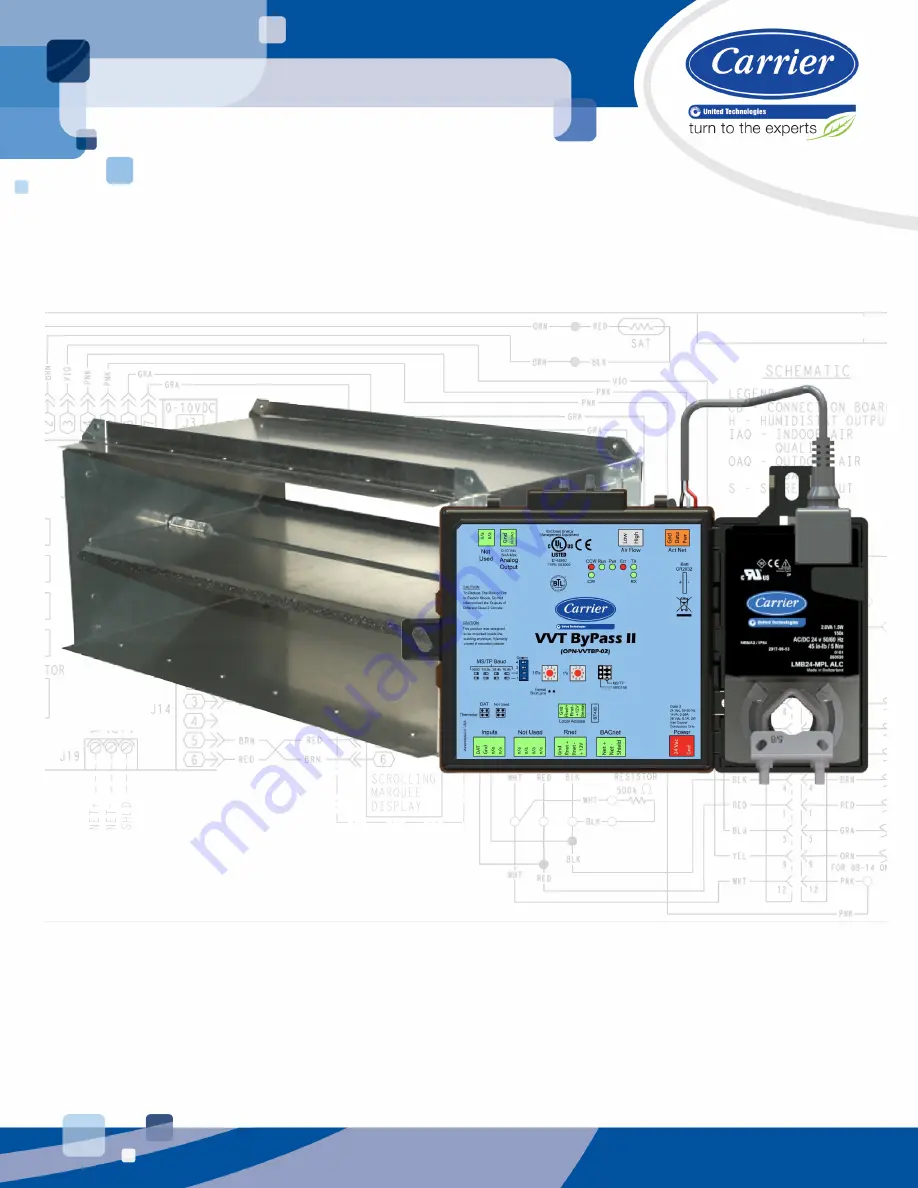
V
V
V
V
T
T
B
B
y
y
p
p
a
a
s
s
s
s
I
I
I
I
C
C
o
o
n
n
t
t
r
r
o
o
l
l
l
l
e
e
r
r
I
I
n
n
s
s
t
t
a
a
l
l
l
l
a
a
t
t
i
i
o
o
n
n
a
a
n
n
d
d
S
S
t
t
a
a
r
r
t
t
-
-
u
u
p
p
G
G
u
u
i
i
d
d
e
e
CARRIER CORPORATION ©2019
A member of the United Technologies Corporation family · Stock symbol UTX · Catalog No. 11-808-601-01 · 1/25/2019
Summary of Contents for VVT Bypass II
Page 51: ......