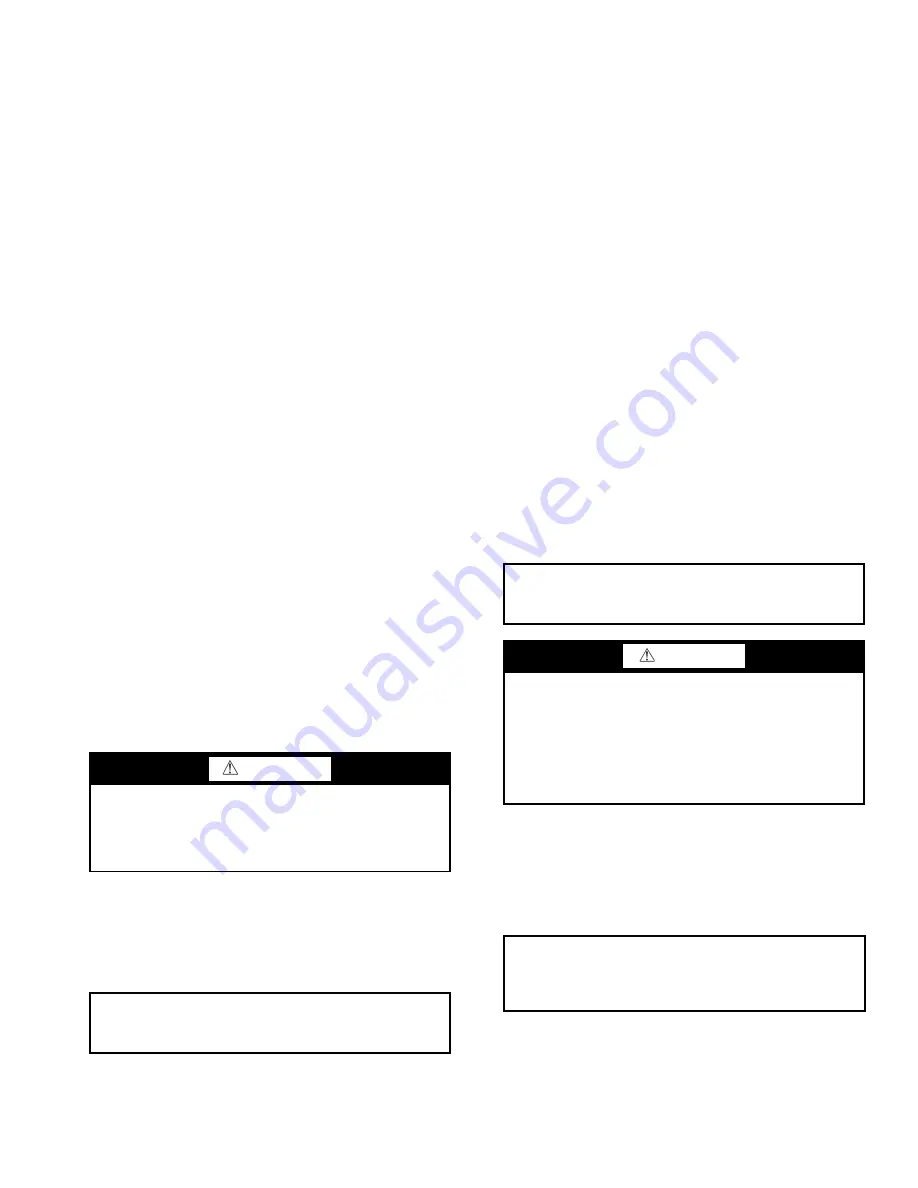
57
3. Replace the drain plug and add 2 gallons (7.6 liters) of a
suitable corrosion-inhibited anti-freeze solution such as
propylene glycol to the cooler to prevent freezing of any
remaining water in system. Antifreeze can be added
through the vent on top of cooler. If the unit has a hydron-
ic pump package, the pump must also be treated in the
same manner.
4. Open one of the thermistor connections to allow air to
escape the vessel and the anti-freeze to enter.
5. At the beginning of the next cooling season, be sure that
there is refrigerant pressure on each circuit before
refilling cooler, add recommended inhibitor, and reset the
CB-HT (circuit breaker heater) (if opened) or restore
power.
HEAT RECLAIM SYSTEM — At the end of each cooling
season the fluid should be drained from the system. However,
due to the heat reclaim condenser circuiting, some fluid will re-
main in the condenser after draining. To prevent freeze-up
damage to the condenser tubes perform the following
procedure.
1. If the heat reclaim condenser will not be drained do not
shut off power disconnect during off-season shutdown. If
the condenser will be drained, deenergize the heaters to
prevent damage and possible safety hazards when drain-
ing, or when there is no liquid in the system. Open the
condenser heater circuit breaker, CB-CDH7 to deenergize
the heaters. Drain the fluid from the system.
2. Isolate the condenser from the rest of the system with wa-
ter shut off valves.
3. Completely fill the condenser with an appropriate
amount of inhibited ethylene glycol solution (or other
suitable corrosion-inhibitive antifreeze) for 15 F
(8.3 C) below the expected low ambient conditions.
4. Leave the condenser filled with the antifreeze solution for
the winter, or drain if desired. Be sure to deenergize heat-
ers as explained in Step 1 to prevent damages. Use an ap-
proved method of disposal when removing the antifreeze
solution.
5. At the beginning of the next cooling season, be sure that
there is refrigerant pressure on each circuit before refill-
ing the condenser circuit, add recommended inhibitor and
reset the CB-CDHT (if opened) to restore power.
Step 6 — Make Electrical Connections
POWER SUPPLY — The electrical characteristics of the
available power supply must agree with the unit nameplate
rating. Supply voltage must be within the limits shown.
Some units have options for multiple power connections.
See Table 9 and Fig. 58 for elecrical connection information.
See Tables 10A-14 for electrical requirements.
POWER WIRING — All power wiring must comply with
applicable local and national codes. Install field-supplied
branch circuit fused disconnect per NEC of a type that can be
locked OFF or OPEN. Disconnect must be within sight and
readily accessible from the unit in compliance with NEC
Article 440-14. In the power box,
7
/
8
in. holes are provided for
power entry. The holes will need to be enlarged to accept the
appropriate conduit. NEC also requires all conduits from a
conditioned space to the power box(es) be sealed to prevent
airflow and moisture into the control box.
Duplex units require at least two separate power supplies, at
least one for each module, depending on the power supply
option ordered.
General Wiring Notes:
1. The control circuit does NOT require a separate power
source. A step-down transformer from the main three-
phase power supply obtains control circuit power. Be sure
that the appropriate connection tap is connected on all
transformers for the supply voltage. Up to three terminal
blocks are provided for field-wired control devices.
2. Cooler heat reclaim condenser and pump heaters (if fac-
tory installed) are wired in the control circuit so they are
operable as long as the main power supply to the unit is
ON. A factory-installed and set overload device protects
them.
NOTE: The field-supplied disconnect should never be off
except when unit is being serviced or is to be down for a pro-
longed period, in which case the cooler and heat reclaim con-
denser should be drained if not properly protected.
3. Power entry depends on the size and power entry option
ordered.
4. Maximum field wire sizes allowed by lugs on terminal
block/non-fused disconnect are listed in Tables 10 and 11.
5. Terminals for field power supply are suitable for copper
conductors. Insulation must be rated 75 C minimum.
CONTROL POWER — Control power is obtained from the
main power supply and does NOT require a separate source. A
toggle switch (marked SW2 on the unit label diagram and by
the switch) allows the control circuit to be manually
disconnected when necessary. Cooler heat reclaim condenser
and pump heaters (if installed) are in an inoperable state when
this switch is in the Off position.
FIELD CONTROL OPTION WIRING — Install field con-
trol wiring options. See Fig. 58 and 59. Some options, such as
4 to 20 mA demand limit that requires the energy management
module, may require that accessories be installed first if not
factory installed for terminal connections.
WARNING
Electrical shock can cause personal injury and death. Shut
off all power to this equipment during installation. There
may be more than one disconnect switch. Tag all discon-
nect locations to alert others not to restore power until work
is completed.
IMPORTANT: Operating unit on improper supply
voltage or with excessive phase imbalance constitutes
abuse and may adversely affect Carrier warranty.
IMPORTANT: To ensure power to the heaters, make
sure power to the unit is always on (except during ser-
vice or a prolonged shutdown).
CAUTION
Proper rotation of condenser fan(s) and pump(s) MUST be
verified before pumps or compressors are started. Consult
the Controls, Start-Up, Operation, Service and Trouble-
shooting guide provided with 30RB060-390 units for cor-
rect procedure. Improper pump rotation can cause
permanent damage to pump impeller and housing. If
pump(s) have been removed for trimming, verify wiring is
reconnected in the original manner.
IMPORTANT: For 208-v systems, the connection tap
for all transformers must be changed. The factory
default setting is for 230-v. Failure to connect to the
proper tap may result in unreliable operation.
Summary of Contents for MINIMUM LOAD CONTROL ACCESSORY 30RB060-390
Page 36: ...36 Fig 24 Unit Rigging Label Detail 30RB060 150...
Page 37: ...37 Fig 25 Unit Rigging Label Detail 30RB160 300...
Page 74: ......
Page 75: ......