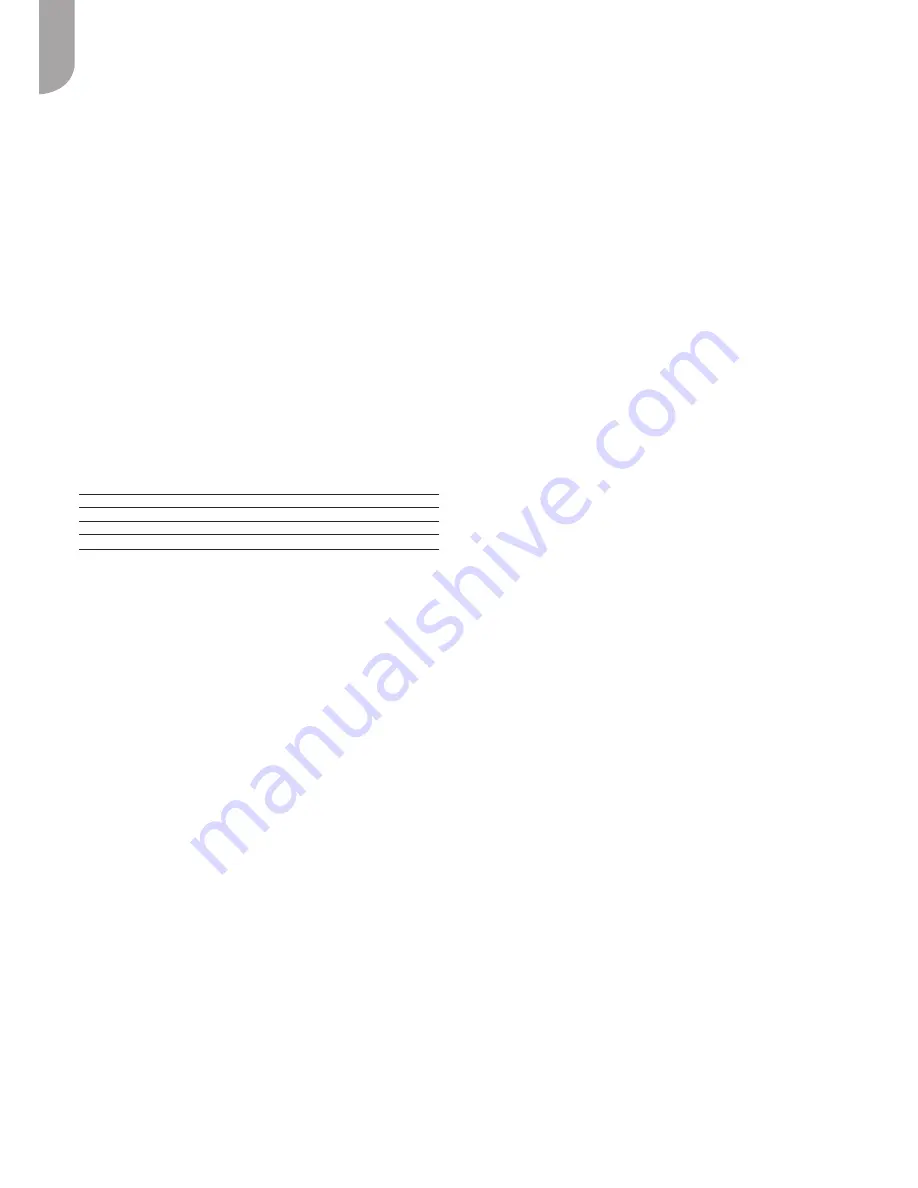
10
English
IMPORTANT: The components, which make up the
different control loops described in this manual include
electronic items. As such, they may generate or be harmed
by electromagnetic interference unless they are installed
and used in accordance with these instructions. The
components making up these control systems conform to
the requirements of electromagnetic compatibility in
residential, commercial and light industrial areas. They
also comply with the low-voltage directive.
If the product is supplied without a Carrier control device,
verification of EMC conformity is the responsibility of the
installer.
2.3 - General installation conditions
IMPORTANT: The Carrier numeric controller, power
module, or in general units fitted with controls loops must
have an isolating device upstream (for example a double-
pole circuit breaker). If necessary, an easily operated
emergency stop device (such as a punch-button switch)
must cut off the power to all equipment. These safety
devices shall be sized and installed in accordance with
IEC Recommendation 364, corresponding to Europe HD
384, France NFC 15 100 and UK IEE Wiring
Regulations. These devices are not supplied by Carrier.
In general terms the following rules must be applied:
Upstream over-voltage protection
Unit without electric heater
T2A
Standard unit sizes 05/09/10/19/21/31 with electric heater
T10A
Standard unit sizes 22/23/29/32/33/39 with electric heater
T16A
•
Units must be provided with over-voltage protection
upstream (not supplied by Carrier). Caution: In LEC
motors the leakage current can reach 3 mA.
•
The power disconnection device must be clearly labelled
to identify which items of equipment are connected to it.
•
The wiring of the components which make up the
different control systems and the communication buses
must be carried out in accordance with the latest rules
and regulations by professional installers.
•
The power supply cable must be doubly insulated and
fixed using a cable clamp. A hole is provided for this
purpose in the plastic Carrier controller housing. The
cable must be clamped on the outer insulation.
•
The control loop components must be installed in an
environment, which conforms to their index of protec-
tion (IP).
•
The maximum level of pollution is normally pollutant
(level 2) and installation category II.
•
The low-voltage wiring (communication bus) must be
kept physically separate from the power wiring.
•
In order to avoid interference with the communication
links:
-
Keep low-voltage wiring away from power cables
and avoid using the same cable run (a maximum of
300 mm in common with the 230 V a.c., 30 A cable).
-
Do not pass low-voltage wires through loops in
the power cables.
-
Do not connect heavy inductive loads to the same
electrical supply (circuit breaker) used by the
controllers, power modules or speed controllers.
-
Use the screened cable type recommended by
Carrier and make sure all cables are connected to
the controllers and power modules.
2.4 - Caution for the control of the unit
IMPORTANT: It is not permitted to connect several unit
units to the same control device (electronic NTC
controller, HDB controller, or any other third party
controller). Carrier electronic Thermostat type A&B for
AC motors require additional accessory board to allow
master/slave function. Carrier electronic Thermostat type
C&D for EC motors can be connected upto 10 units, refer
to thermostat installation manual instructions.
2.5 - Conformity
This equipment is in compliance with the essential
requirements of the following European directives:
•
Electromagnetic compatibility: 2004/108/EEC,
•
Low-voltage directive: 2006/95/EEC.
3 - INSTALLATION OF THE UNIT
3.1 - Installing the unit in the false ceiling
The positioning of the unit must not create an obstacle that
may lead to an unequal distribution and/or return flow of the
air. The ceiling must be sufficiently even to allow a simple
installation without danger from the unit. The supporting
structure must be able to carry the unit weight and prevent
deformation, breaks or vibrations during operation.
INSTALLATION PRECAUTIONS: During the installation
process, remove all debris and construction material from
the ducts to prevent any damage to the unit.
3.2 - Installation procedure
•
Position the 42EM close to where it is to be installed
in the ceiling void. For installation in a false ceiling use
a hydraulic lift and a folding ladder to make the task
easier (Fig. 6).
•
Check that the clearances around the unit are sufficient
to allow easy maintenance. Please refer to the diagram
that shows the service clearances.
•
Mark the position of the threaded hangers on the
ceiling (if several units need to be installed, it may be
advisable to produce a drilling template). The method
of fixing the threaded hangers (not supplied by Carrier)
depends on the ceiling type (maximum diameter of
the threaded hangers is 10 mm). Once the threaded
hangers are fixed to the ceiling, tighten the first nuts.
WARNING: When moving the units, do not use water
pipes, condensate drain pan, valves or flexible pipes to lift
them.
Lift the unit and align it on the threaded hangers, insert
the second nuts and tighten them slightly.
NOTE: At this point do not tighten the nuts fully and do
not clamp the unit up to the ceiling (leave a space between
the ceiling and the unit). The nuts will be adjusted finally,
when the unit has been connected to the pipework and
ducts and levelled.
Level the unit (Fig. 7).
Adjust the hanger nuts so that the unit is inclined 0.5%
towards the condensate drain pan. In the other direction
(air flow direction) the unit must be perfectly level (Fig. 8).