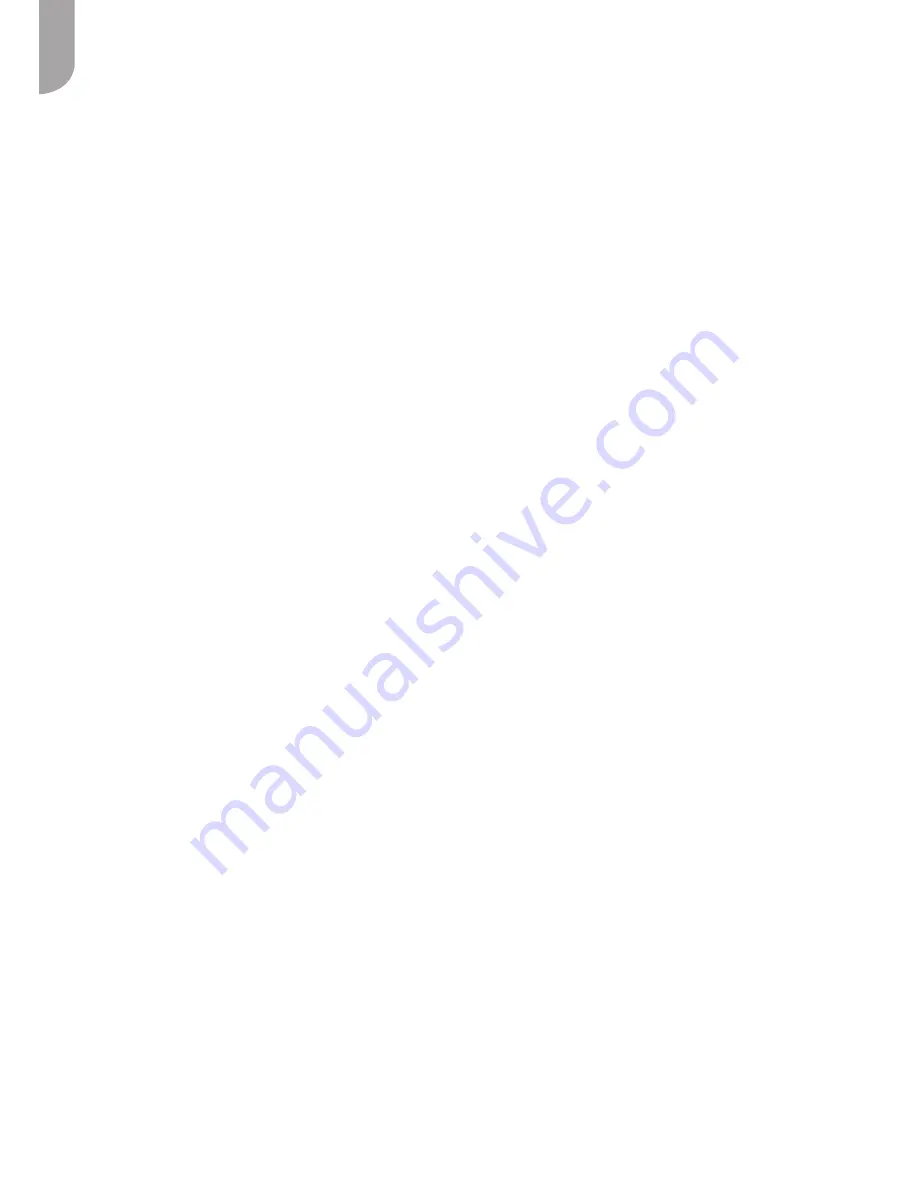
14
English
•
Disconnect the power supply to the unit before carrying
out any work on a unit.
•
Disconnect the actuator power supply cable.
-
230 V type actuator used with the Carrier
numeric controller: Disconnect the actuator
power supply cable fitted with a quick connector.
-
230 V actuator used with an electronic
thermostat: Remove the plastic protection cover
held in place with two screws. Disconnect the
actuator power supply cable connected to the
quick connector. This can be done by pressing
down the spring tongue using a screwdriver and
pulling out the wire from the appropriate terminal.
•
Uncouple the faulty actuator. Refitting is by the reversal
of the procedure described above.
WARNING: Ensure that the actuator is firmly screwed to
the valve body (maximum torque 15 N·m).
4.6.4 - Valve body replacement procedure
•
Disconnect the power supply before carrying out any
work on a unit.
•
Close the isolating valves on the manifolds.
•
Unscrew the union nuts to disconnect the flexible water
pipes.
•
Remove the valve actuators taking care to identify the
cooling and heating valves.
•
Disconnect the flexible condensate drain pipe which is
held in place by a collar (the collar is not supplied by
Carrier).
•
Remove the two-way or four-way water flow control
valve bodies. Depending how the unit is configured,
the four-way valve coupling may be fitted with a
heating/cooling changeover switch, if so do not
remove it.
•
Fit the new valve body to the coil (fit new gaskets).
•
Reconnect the flexible condensate drain pipe which is
held in place by a collar (the collar is not supplied by
Carrier).
•
Refit the valve actuators taking care to ensure that
they are correctly fixed to the valve body.
•
Reconnect the flexible water pipes by tightening the
union nuts. Retighten all the water connections and
ensure that all gaskets have been changed and correctly
fitted (maximum torque 15 N·m).
•
Open the isolating valves on the manifolds and purge
all air from the system.
•
Check that there are no leaks and reconnect the power
to the unit.
WARNING: When replacing a valve always ensure that
the direction of flow through the valve is as shown by the
arrow on the valve body. If the direction of flow is wrong,
the valve body will deteriorate rapidly.
4.7 - Flexible pipe option
Minimum bending radius:
•
non-insulated pipes 72 mm
•
insulated pipes 106 mm.
4.8 - Optional
electric heater
WARNING: Disconnect the power supply before carrying
out any work on the unit.
If the electric heater develops a fault, it must be replaced;
this requires the removal of the fan motor assembly: Fig. 17
(17a = screw).
CAUTION: Do not touch the live metal heater elements
when the electric heater is connected to the power supply.
Electric heater replacement procedure:
•
Remove the filter.
•
Remove the fan motor assembly access panel.
•
Identify and note the fan speeds wired to the auto-
transformer terminal block. Disconnect the power
supply cable.
•
Remove the fan motor assembly.
NOTE: Be careful not to touch the fan blades during
the removal process to avoid unbalancing the fans.
•
Disconnect the electric heater power supply cables
and remove them through the cable conduit.
•
Unscrew the defective heater(s) and replace it (them).
•
Replacement of the fan motor assembly is by the
reversal of the above procedure.
WARNING : Carrier Electronic thermostat type B and D
are embedded with Electric heater relay 8 Amps.
Accordingly, Carrier requires an additional protection
relay for electric heater 2000W and 3200W.
WARNING : In case of customer supplied controller,
Carrier recommends to set up an additional protection
relay corresponding to the electric heater capacity.
4.9 - Optional condensate pump (fig. 26)
According to the fig. 26, the condensate pump installation
require the following actions:
• Press the pump at the lowest position according to the
available height in the false celling (fig. 26b)
• Check the sealing of the hydraulic connection of the
condensate pump and condensate recovery
The meaning of the electrical wires is described below:
• Brown - Blue wires : Electrical supply 230V 50/60Hz
• Black - Grey wires : Alarm contact Normally Closed
(NC) 250V/8A maxi