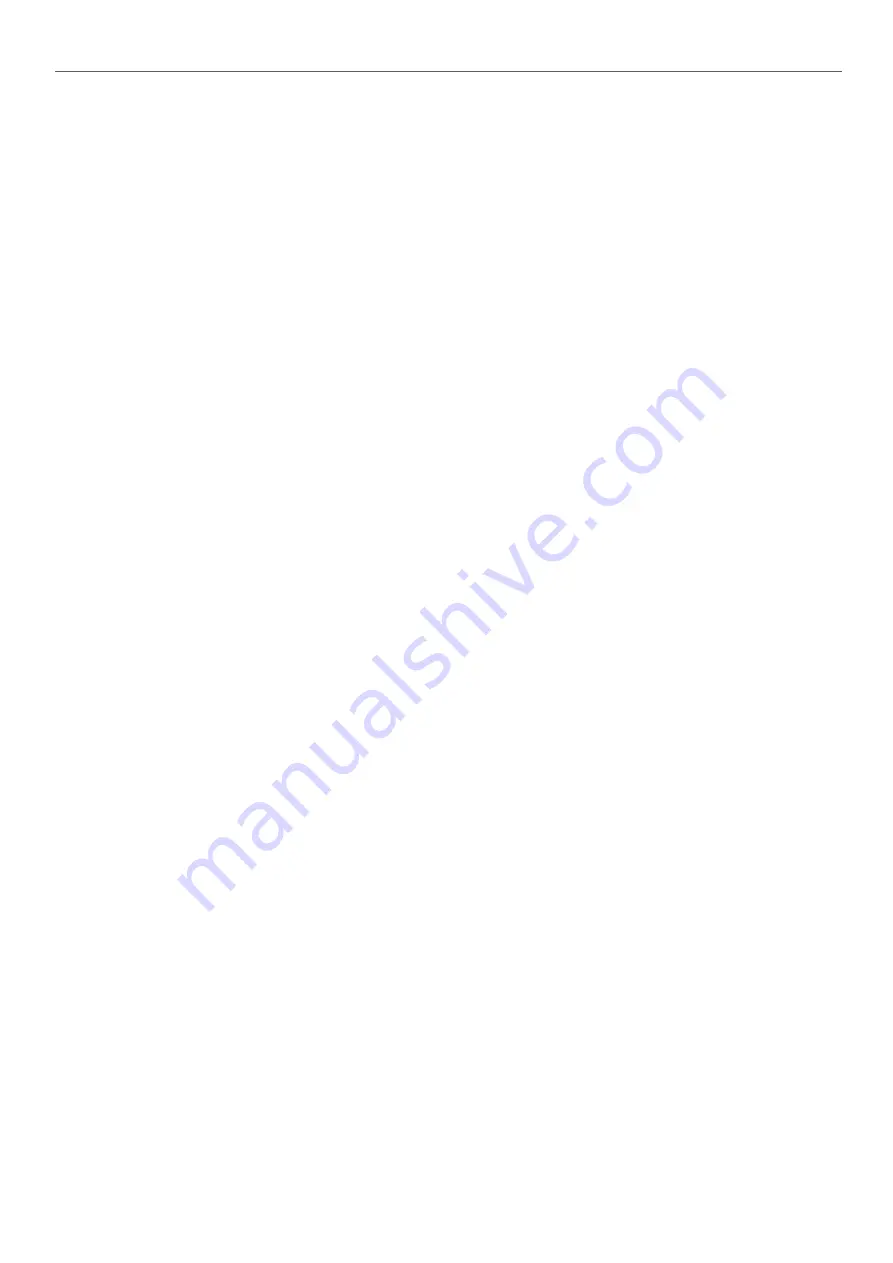
9
2 - PRELIMINARY CHECKS
2.1 -
Check equipment received
■
Inspect the unit for damage or missing parts. If damage is
detected, or if shipment is incomplete, immediately file a claim
with the shipping company.
■ Confirm that the unit received is the one ordered. Compare the
name plate data with the order.
■
The unit name plate must include the following information:
-Version number
- Model number
- CE marking
- Serial number
- Year of manufacture and test date
- Fluid being transported
- Refrigerant used and refrigerant class
- Refrigerant charge per circuit
-
Containment fluid to be used
- PS: Min./max. allowable pressure (high and low pressure
side)
- TS: Min./max. allowable temperature (high and low pressure
side)
- Pressure switch cut-out pressures
- Unit leak test pressure
- Voltage, frequency, number of phases
- Maximum current drawn
- Maximum power input
-Unit net weight
■ Confirm that all accessories ordered for on-site installation have
been delivered, and are complete and undamaged.
The unit must be checked periodically during its whole
operating life to ensure that no shocks (handling accessories,
tools etc.) have damaged it. If necessary, the damaged parts
must be repaired or replaced. See also chapter “Standard
maintenance”.
2.2 -
Moving and sitting the unit
2.2.1 -
Moving
See chapter “Installation safety considerations”.
CAUTION: Only use slings at the designated lifting points
which are marked on the unit.
2.2.2 - Sitting the unit
Always refer to the chapter “Dimensions and clearances” to confirm
that there is adequate space for all connections and service
operations. For the centre of gravity coordinates, the position of
the unit mounting holes, and the weight distribution points, refer
to the certified dimensional drawing supplied with the unit.
Typical applications of these units are in refrigeration systems,
and they do not require earthquake resistance. Earthquake
resistance has not been verified.
Before siting the unit check that:
■
the permitted loading at the site is adequate or that appropriate
strenghtening measures have been taken.
■
the unit is installed level on an even surface (maximum
tolerance is 5 mm in both axes).
■ there is adequate space above the unit for air flow and to ensure
access to the components.
■
the number of support points is adequate and that they are in
the right places.
■ the location is not subject to flooding.
CAUTION: Lift and set down the unit with great care. Tilting
and jarring can damage the unit and impair unit operation.
2.2.3 -
Checks before system start-up
Before the start-up of the refrigeration system, the complete
installation, including the refrigeration system must be verified
against the installation drawings, dimensional drawings, system
piping and instrumentation diagrams and the wiring diagrams.
During the installation test national regulations must be followed.
If no national regulation exists, standards such EN-378 or ISO-
5149 can be used as a guide.
External visual installation checks:
■
Ensure that the machine is charged with refrigerant. Verify on
the unit nameplate that the ‘fluid being transported’ is not
nitrogen.
■
Compare the complete installation with the refrigeration system
and power circuit diagrams.
■
Check that all protection documents and equipment provided
by the manufacturer (dimensional drawings, P&ID, declarations
etc.) to comply with the regulations are present.
■
Verify that the environmental safety and protection and devices
and arrangements provided by the manufacturer to comply with
the regulations are in place.
■ Verify that all document for pressure containers, certificates,
name plates, files, instruction manuals provided by the
manufacturer to comply with the regulations are present.
■
Verify the free passage of access and safety routes.
■
Check that ventilation in the plant room is adequate.
■
Check that refrigerant detectors are present.
■
Verify the instructions and directives to prevent the deliberate
removal of refrigerant gases that are harmful to the environment.
■
Verify the installation of connections.
■ Verify the supports and fixing elements (materials, routing and
connection).
■ Verify the quality of welds and other joints.
■
Check the protection against mechanical damage.
■
Check the protection against heat.
■
Check the protection of moving parts.
■
Verify the accessibility for maintenance or repair and to check
the piping.
■
Verify the status of the valves.
■
Verify the quality of the thermal insulation and of the vapour
barriers
■
Check the condition of the insulation of the 400 V cables.